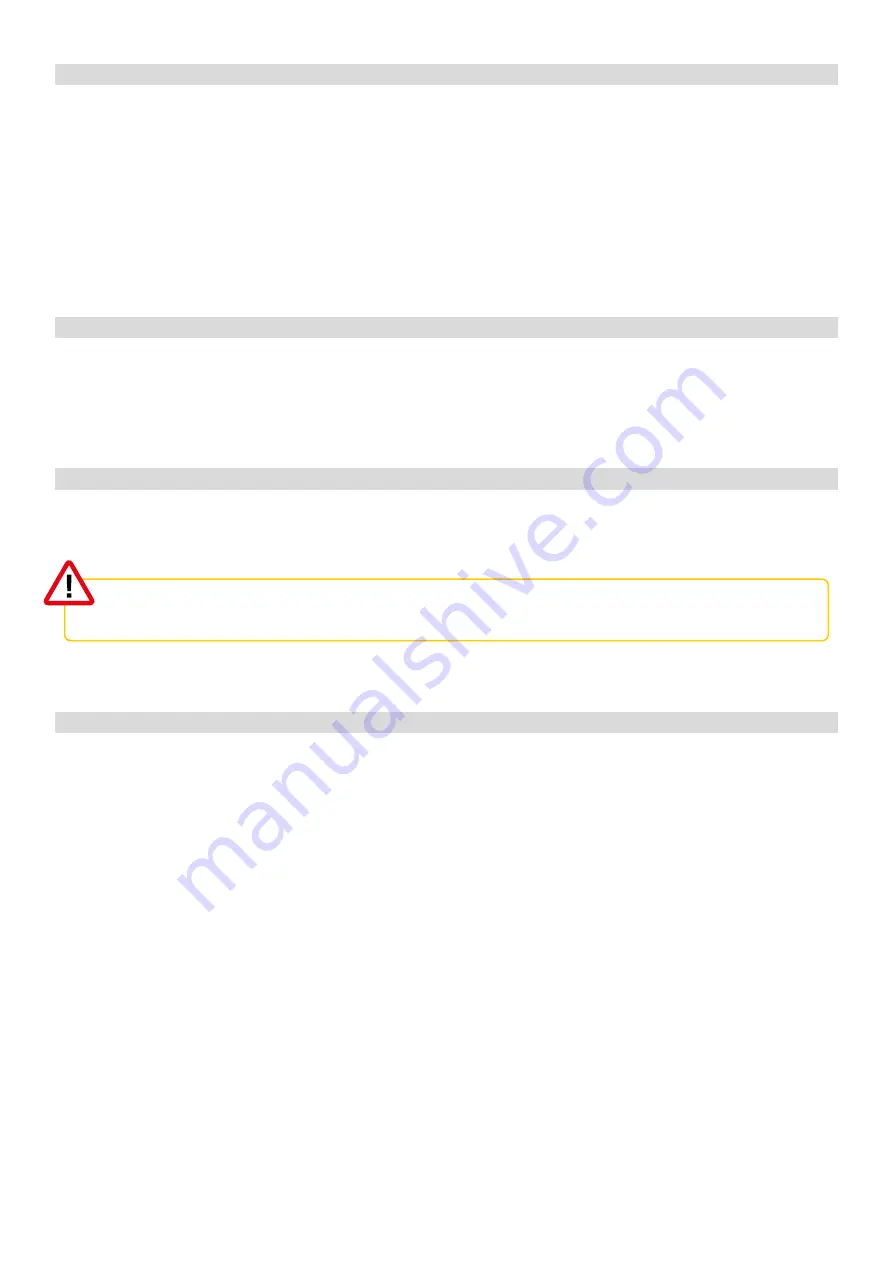
XRGI® COMMISSIONING INSTRUCTION
VERSION 1.0 2019
7
2.3.3
A C T I O N S W I T H F I R E O R I N G R E S S O F W AT E R
2.3.4
A C T I O N S W I T H S M E L L O F E X H A U S T G A S I N B U I L D I N G S
Please proceed as follows in the event of fire or the ingress of water:
■
Switch off the all-pole breaker!
■
Switch off the master switch on the system!
■
Close the shut-off valve on the gas pipe!
■
Inform the responsible service department!
■
In the event of the outbreak of fire, immediately close the gas shut off valve on the connection panel and the main gas solenoid
valve on the gas pipe, cut off the supply of fresh air to the fire and inform the local fire service!
■
In case of flooding (e.g., flooding in the basement), do not step into the water!
■
Only use approved fire extinguishers to put out the fire!
■
Warn other occupants of the building and leave the building!
Due to a malfunction, exhaust gas can escape and lead to the risk of poisoning.
If you smell exhaust gas in buildings, proceed as follows:
■
Shut down the XRGI® system!
■
Open windows and doors!
■
Notify your heating company!
The monitoring systems are only activated when the system‘s master switch is turned to „I“ and the system has not
been isolated from the power supply.
2.3.5
F R O S T P R O T E C T I O N
2.3.6
C O N TA C T H A Z A R D
Ensure that the XRGI® system remains in operation and that the area is appropriately heated if you are absent during periods of frost
and/or the winter months.
Components that can cause injury on contact (hot and/or electrically conductive parts) are concealed behind panels that can only be
removed with keys or tools. Only permit authorised EC POWER specialists to remove these panels.
The door on the iQ-Control Panel is there for your protection and should only be opened by trained electricians. The main switch
disconnecter (red switch) is located on the left-hand side of the iQ-Control Panel. When it is switched on, there is a risk of you getting
an electric shock if touching any of the control components. The iQ-Control Panel contains sensitive electronic components. If they
are not handled professionally, the XRGI® system may be damaged.
The cover on the Power Unit is there for your protection. In particular, be aware of the following when opening the Power Unit:
■
The engine gets hot. You risk being burned if you touch it or any of the other components.
■
The protective cover conceals parts that start to rotate when the XRGI® system starts up and is running. Touching these parts
while the Power Unit is running can be fatal. Only permit authorised and trained personnel to touch components under the
protective cover when the system is running. Avoid wearing loose-fitting clothing, jewellery and untied long hair when checking
the Power Unit visually, as they could become caught up in rotating parts.
■
The generator and many other parts are connected to the power supply system. Touching non-isolated parts can be fatal.
■
There is a risk of damage to the hearing of anyone in the vicinity of a running Power Unit with an open cover. Please wear
approved hearing protection when the cover is open.
The installation of an equipotential bonding between the CHP and all metal parts near the XRGI® system, gas pipes, water pipes,
ventilation etc. must comply with applicable regulations and ordinances and is strongly recommended by EC POWER. The equipo-
tential bonding must be calculated and carried out professionally and depends on the type of soil protection used (TN-s, TT, etc.). The
equipotential bonding also contributes to the comprehensive protection of the XRGI® system against lightning strikes.
One option for providing frost protection would be to drain the XRGI® system. It must be ensured that the XRGI® system is completely
drained. Always take the advice of your authorised EC POWER specialist.
Summary of Contents for XRGI 6
Page 1: ...VERSION 1 0 2019 01DOC1075 01 COMMISSIONING INSTRUCTION...
Page 2: ......
Page 14: ...XRGI COMMISSIONING INSTRUCTION VERSION 1 0 2019 12...
Page 47: ...XRGI COMMISSIONING INSTRUCTION VERSION 1 0 2019 45 N OT E S...
Page 48: ...XRGI COMMISSIONING INSTRUCTION VERSION 1 0 2019 46 N OT I Z E N...
Page 49: ......
Page 50: ...01DOC1075 01 09 2019 CO M M I S S I O N I N G I N S T R U C T I O N...