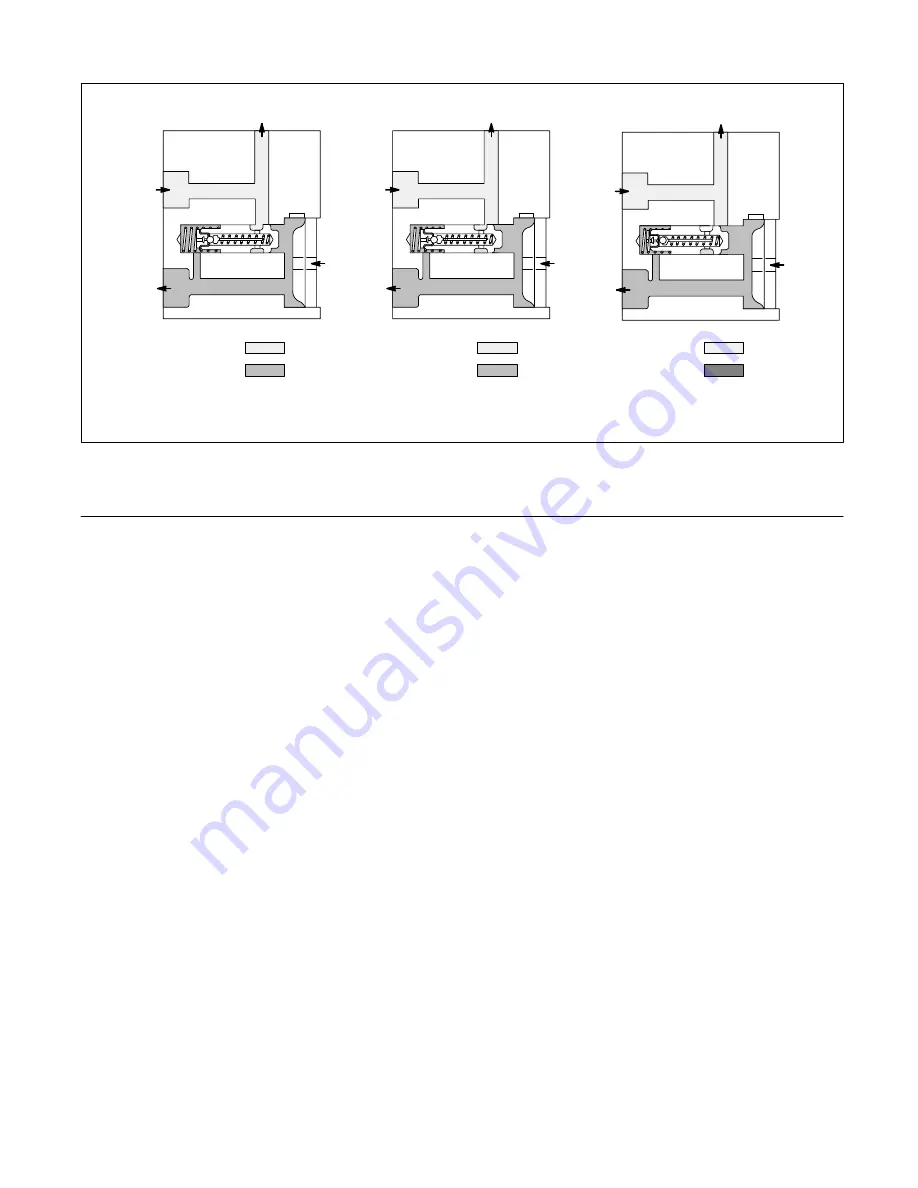
6
Figure 4.
A
All Pump
Delivery
B
Normal Operation
C
Operation causing excessive
pressure build-up
To Tank
Return
Port
Pressure
Port
Pressure
Code:
Return
Normal
From
Pump
To Tank
Return
Port
Pressure
Port
Pressure
Code:
Return
Normal
From
Pump
Pressure
Port
Return
Port
To Tank
From
Pump
Return
High
Pressure
Code:
Section IV - Installation and Operating Instructions
A. Drive Connections
Care must be exercised in pump mounting to insure correct
alignment with the driving medium. If indirect drive is used,
belts and pulleys must be properly aligned and adjusted to
prevent undue side loads being imposed on the shaft
bearings.
B. Shaft Rotation
1. Pumps are manufactured for either right hand or left
hand rotation. They must be driven in the direction of the
arrow on the pump ring or severe damage may result.
2. The direction of rotation can be changed by reversing
the pump ring and replacing the pressure plate with the cor-
rect plate for the desired direction of rotation (see parts cata-
log M-1370-S). Correct disassembly and assembly proce-
dures are given in Section VI of this manual.
C. Hydraulic Tubing
1. The number of bends in tubing must be kept to a mini-
mum to prevent excessive turbulence and friction of oil flow.
2. Tubing must not be bent too sharply. The minimum
radius for bends is three times the inside diameter of the
tube.
3. To minimize flow resistance and the possibility of leak-
age, only as many fittings and connections as are necessary
for proper installation should be used.
4. Tubing must not be sprung into position or undue
strain will result at the connections.
5. All tubing must be thoroughly cleaned before installa-
tion to remove dirt, rust and scale. Recommended methods
of cleaning are sand blasting, wire brushing and pickling.
D. Hydraulic Fluid Recommendations
1. Oil Type - Oils used in hydraulic systems perform the
dual function of lubrication and transmission of power. Oil
must be selected with care and with the assistance of a
reputable supplier.
Crankcase oils meeting or exceeding the ”Five Engine Test
Sequence” for evaluating oils for API (American Petroleum
Institute) service MS (Maximum Severity) best serve the
needs of mobile hydraulic systems. These engine sequence
tests were adopted by the Society of Automotive Engineers,
American Society for Testing Materials, and automotive
engine builders. The MS Classification is the key to selection
of oils containing the type of compounding that will extend
the operating life of the hydraulic system. Oils meeting
Diesel engine requirements, DG and DS classifications, may
or may not have the type of compounding desired for high
performance hydraulic systems.