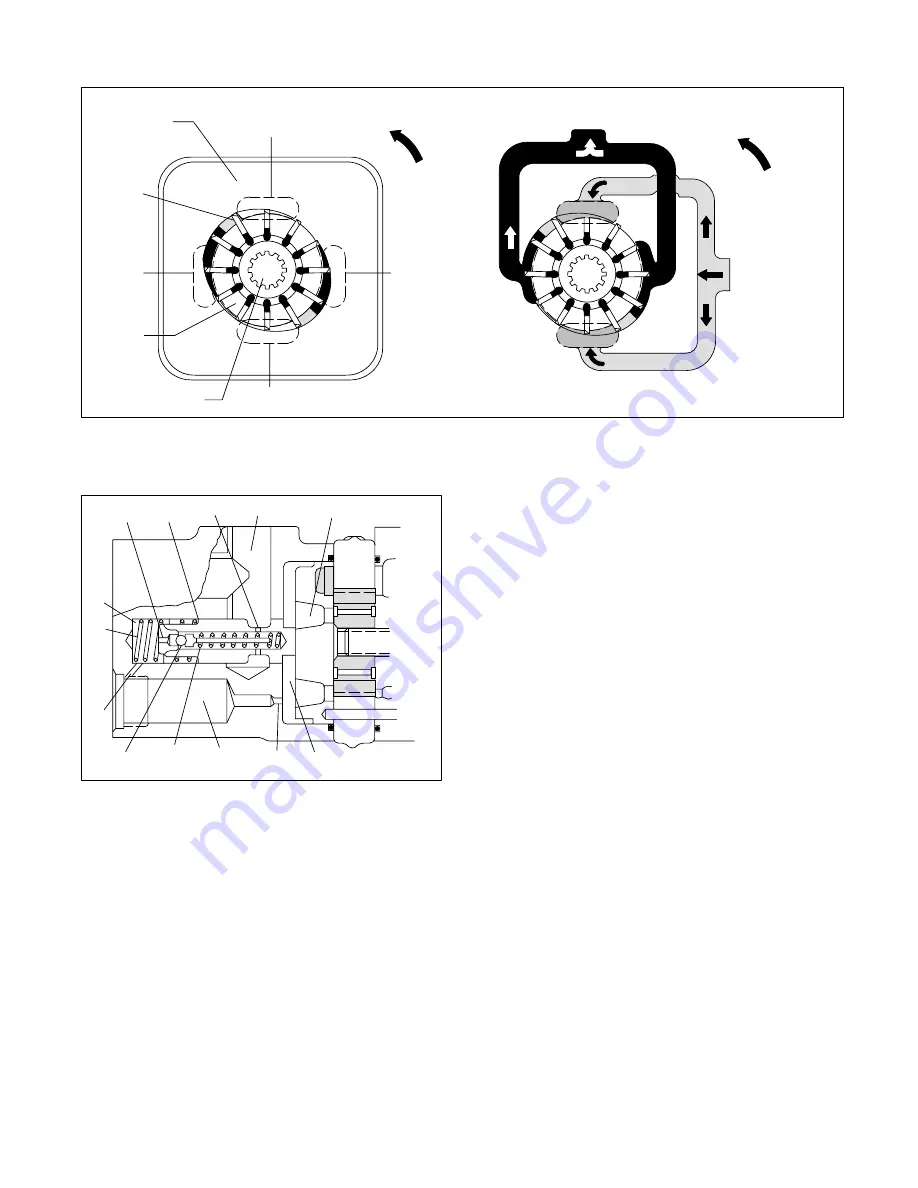
5
Figure 2. Schematic View Showing Oil Flow and Vickers Hydraulic Balance Construction.
Cam Ring
Inlet
Outlet
Outlet
Rotor
Drive Shaft
Inlet
Rotation
Vane
Outlet
Inlet
Rotation
Figure 3.
H
F
2
G
4
3
E
D
B
A
C
1
J
D. Flow Control and Relief Valve
1. Maximum fluid delivery and maximum system pres-
sure are determined by the integral flow control and relief
valve (Figure 3). The rate of flow depends on the sizes of the
restriction (D) in the cover. Excess oil is ported past the slid-
ing spool (1) to the return circuit by way of passage C.
2. When all pump delivery can pass through the restric-
tion to the load, the spool is held in the closed position by the
large spring (2) and passage C is blocked from chamber B.
This is the condition illustrated in Figure 4-A.
3. When pump delivery is greater than the flow rate de-
termined by the restriction (D), a pressure build-up in cham-
ber B forces the spool open against the large spring force.
Excess fluid is throttled past the spool to passage C and
back to inlet, as shown in Figure 4-B.
4. Figure 4-C shows the condition when pressure in the
system builds up to the relief valve setting. Pressure is trans-
mitted through sensing orifices G and H and forces the ball
(4) from its seat. Fluid flow is then from chamber B, through
orifice D, passage E, orifices G, H and J to passage C and to
inlet. The pressure drop across restriction D resulting from
this flow causes a differential pressure on the spool ends
and the spool is shifted against the large spring, permitting
the remainder of pump delivery to flow from chamber B to
passage C.
5. A second function of the valve sub-assembly and #2 is
to hold the pressure plate against the pump cartridge until
pressure builds up in chamber B.