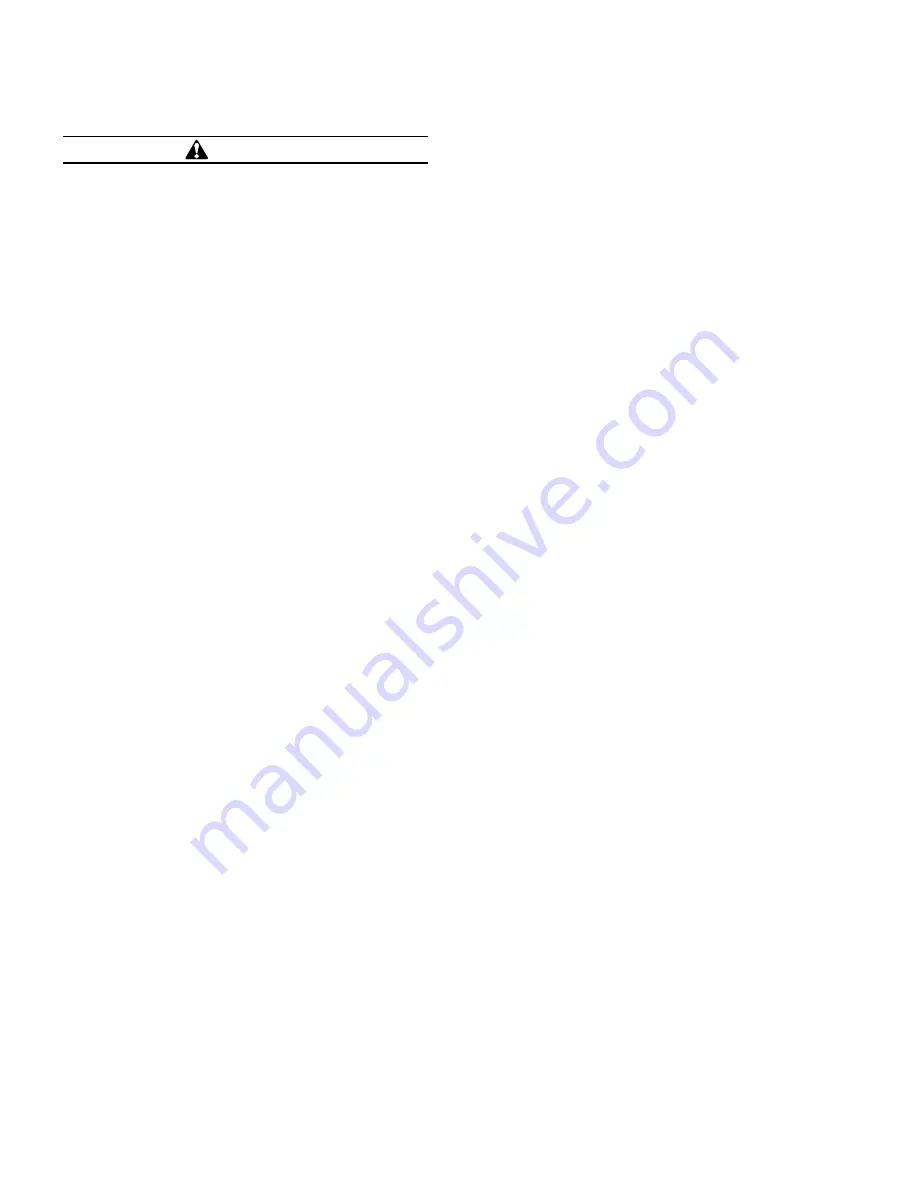
PowerXL DG1 Series VFD
xii
PowerXL DG1 Series VFD
MN040002EN—March 2014
www.eaton.com
CAUTION
Improper drive operation:
●
If the drive is not turned on for a long period, the
performance of its electrolytic capacitors will be reduced.
●
If it is stopped for a prolonged period, turn the drive on at
least every six months for at least 5 hours to restore the
performance of the capacitors, and then check its
operation. It is recommended that the drive is not
connected directly to the line voltage. The voltage should
be increased gradually using an adjustable AC source.
Failure to follow these instructions can result in injury
and/or equipment damage.
For more technical information, contact the factory or your
local Eaton sales representative.
Summary of Contents for PowerXL DG1-32011FB-C21C
Page 1: ...PowerXL DG1 Series VFD Installation Manual Effective March 2014 New Information ...
Page 2: ......
Page 83: ......