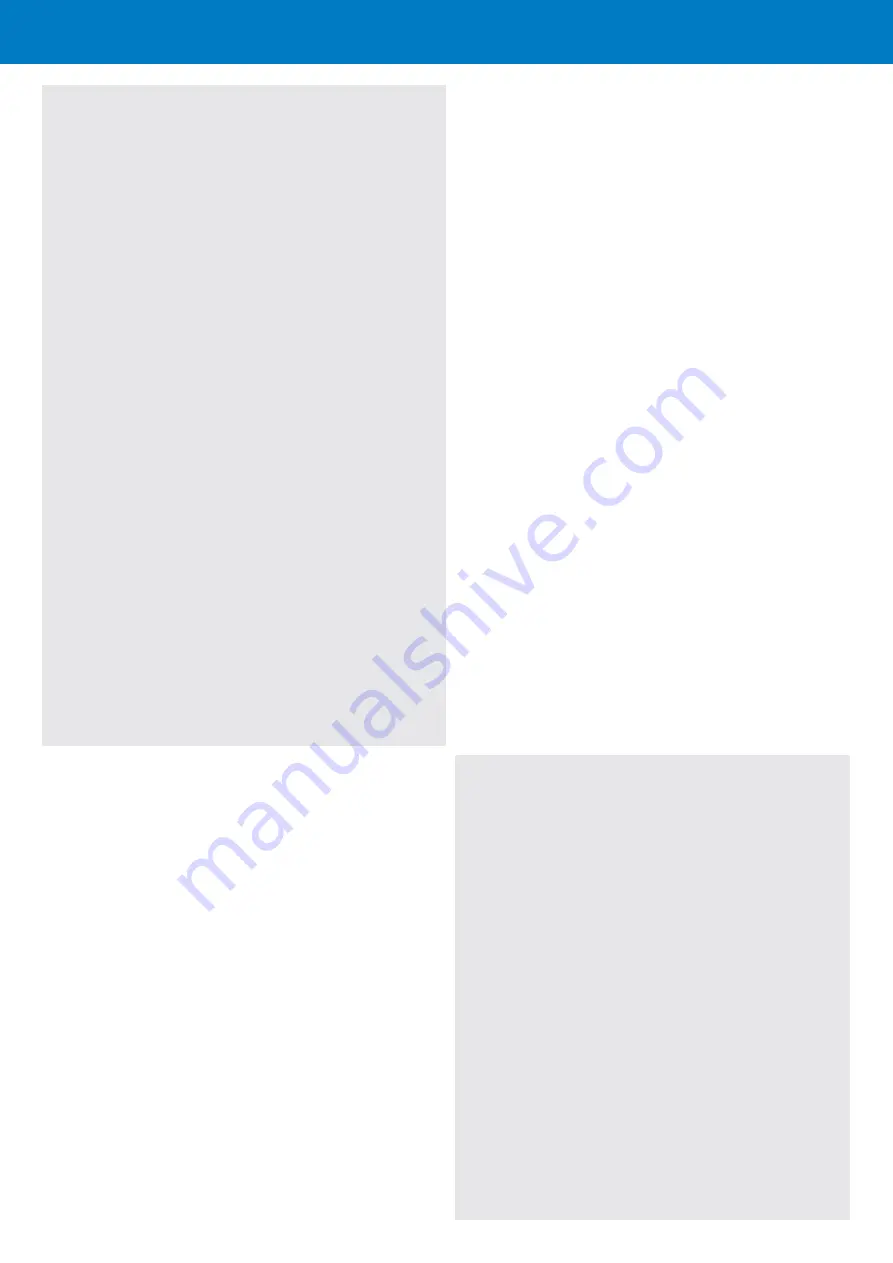
EATON
wb-xp2-en
11
Maintenance of Busbar
Prior to carrying any maintenance work (other than thermal
imaging), ensure the Busbar is completely electrically
isolated by isolation, verifi cation and lock off of the supply
device in accordance with isolation procedures / method
statement.
Familiarisation with IEE Wiring Regulations or similar Local
Safety Standards should be understood in order to ensure
safe isolation of the Busbar Trunking.
Thermal Imaging should be conducted along the Busbar
route to identify any possible problems.
Once identifi ed a preventative maintenance program should
be instigated with the Busbar isolated as described above
before carrying out any work.
If joints are found to be loose they should be re-torqued
to the correct torque level as outlined in the Installation
Detail. If a joint is found to be loose but it shows no sign
of overheating simply re-torque the joint and conduct an
Insulation Resistance test prior to re-energising.
If slight discolouration occurs remove the joint and clean the
conductor with a fi ne grade (240) abrasive paper. Re-install
the joint and megger test.
If adverse overheating has occurred, please contact Eaton
for further details.
Megger test results at this point could be lower than those
taken during the fi rst installation test. As long as the reading
does not measure below 5M
at 100VDC the system is
atisfactory for re-energisation.
Maintenance of Tap Off Module
As with the main Busbar system the joints require checking
on the Tap Off connections. Thermal Imaging can identify
localised heat spots.
As previously described, upon identifying a local
problem preventative maintenance should be
investigated with the busbar isolated.
If discolouration has occurred on the contact due to
overheating, ensure the gap between contact’s are
consistent and have not been damaged during transport,
if they have, please contact Eaton.
If the joints show slight discoloration, clean them and
re-tighten. If adverse overheating has occurred, please
contact Eaton for further instruction. Visually check
the installation of the Tap Off Module, check clamping
mechanism, check door-interlocking device to ensure it
still operates correctly. Check outgoing cable connections
and gland tightness / integrity. Check the operation of the
switching device positive ‘ON’, ‘OFF’ operation. Examine
protective device for sign of short circuit operation. If a
short circuit has occurred on the equipment connected
to the tap off module check operation of device and the
integrity of the device.
Energising
The Busbar should be energised immediately after following
steps 1 to 6 (shown above).
Only authorized, competent personnel should energise
electrical circuits in line with „switching procedures” and
„permit to work’ forms provided by the Site Electrical
Supervisor.
All connected load to the Busbar Trunking via tap offs for
example should be isolated prior to energizing the bar.
The Main Supply switch to the Busbar is to be energised
fi rst.
The Protection Settings should be at the circuit breakers
minimum protection level.
Only when the Busbar is being put into service are the
Protection Settings set to the specifi ed fi gures.
Following the successful closing off the supply breaker, close
the circuit breaker(s) supplying the connected loads (via Tap-
Offs) one by one.
Visually inspect the energised Busbar route to look for any
anomalies. Listen for noises from the system as this could
indicate untightened cover plates.
Prior to Energising
3 test must be completed prior to energising
Step 1.
A continuity test to verify the run is complete.
Step 2.
A ductor test to check the resistance of the joints
through the entire length.
Step 3.
A megger test, 1000VDC between each conductor
and Earth. Readings will vary widely between site to site due
to length of run, humidity, temperature and site conditions.
If readings less than 5M
are obtained, measures must be
taken to identify the location of the low resistance level and
take appropriate measures to increase the resistance level.
This test should only be carried out by competent personnel.
Step 4.
Ensure all tap off boxes have been correctly installed
as instructed and are in the ‘ON’ position for insulation
resistance testing.
Step 5.
Ensure all connections to the Busbar / tap offs have
been disconnected.
Step 6.
Verify that all joints have been torqued according to
the recommended setting and have not been subsequently
loosened. Ensure all joint covers are fi rmly secured.
Step 7.
When reconnecting the system prior to energisation,
ensure correct Phase Rotation is achieved by testing prior to
energising the supply.
Step 8.
Ensure all tap offs are turned off again prior to
Energising.
Step 9.
The testing procedure
should
be performed and
documented as per Eaton standard testing procedure
available on request.
Summary of Contents for Power Xpert XP2
Page 8: ...EATON wb xp2 en 8...