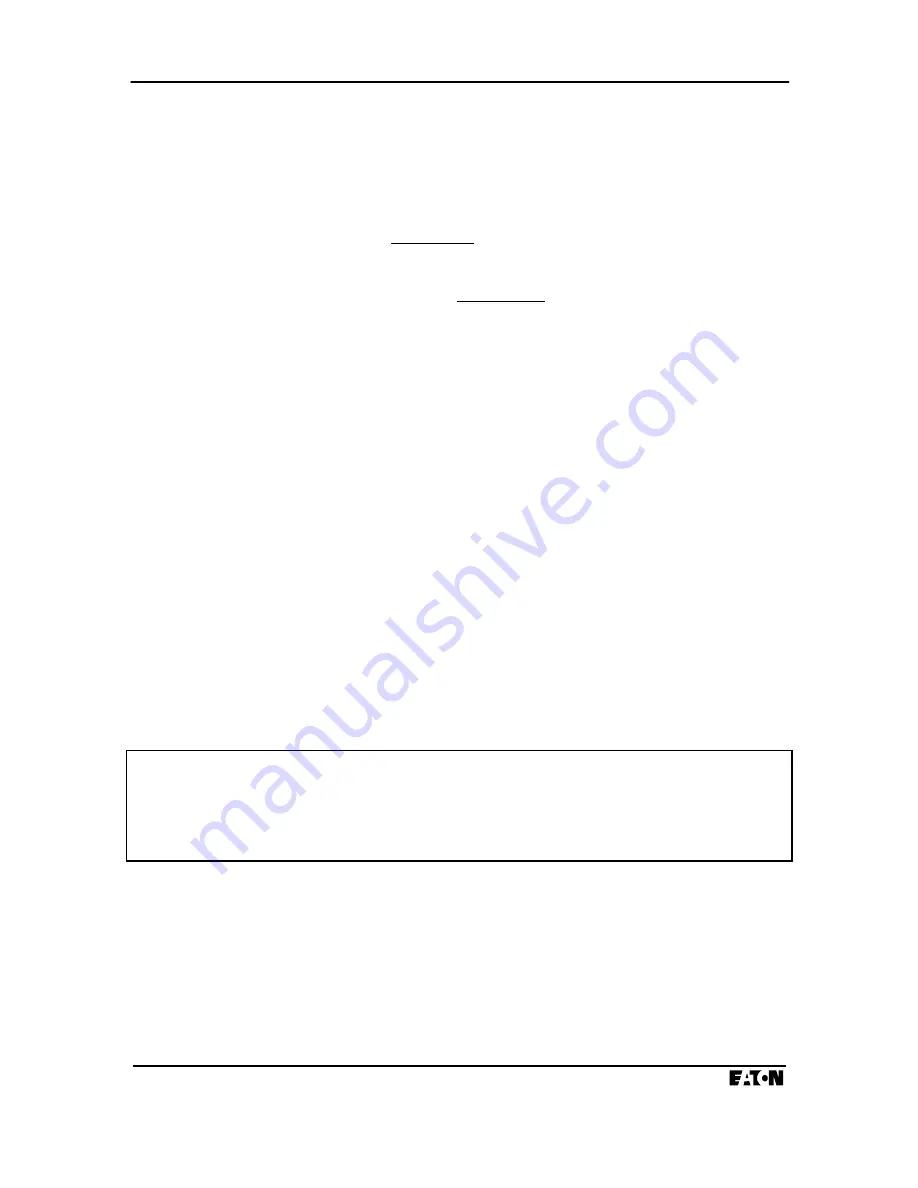
I.L. 17562
Page 57
PR 0.3 Effective 8/99
expected time. If a problem develops later on, the report-back contact opens. In either case, the
open contact state indicates that the motor should be tripped.
To use this function, set a time limit for report-back here. Set P5L9, next, to define the start of
report-back timing. Connect the report-back contact to MP-3000 Discrete Input 2. This input
must then be energized before the set time expires, or the relay trips for incomplete sequence.
Note that the input must be energized continuously after the time delay has expired to hold off
this trip.
Note that Discrete Input 2 setting P7L1 below is automatically assigned to the function INC SEQ
if a time delay is set here. All other alternate uses for Discrete Input 2 (P7L1) are suppressed
and not visible until INSQ is set to OFF.
5.5.9 Setpoint P5L9, Incomplete Sequence Start Timer Event (INSQ TRN or INSQ ST) —
Choose either to start the incomplete-sequence timer when the motor start is declared (INSQ
ST), or when the transition from start to run is declared (INSQ TRN).
5.5.10 Setpoint P5L10, Long Acceleration Time (LAT) —
Sets a time interval during which the
motor is permitted to accelerate a high-inertia load, which is longer than the locked-rotor time.
This function can be set to OFF, and usually should be. If the thermal-model accumulator
bucket fills to 100% during the long acceleration time, it is limited to that value and the thermal
trip is held off until the LAT delay expires. By then, the thermal bucket level must have
decreased (thermal model cooled) below 100% or the motor trips.
The LAT function should be used only on motors with a zero-speed switch (normally-closed
contact which opens when the motor actually begins to spin). Connect the zero-speed switch
contact to MP-3000 Discrete Input 1. The Zero-Speed Switch function must be enabled (ZSW
ON)- see setting P5L11 below. The MP-3000 then requires the zero-speed switch to open within
LRT/2 (half of locked-rotor time setting P1L3) after a start, or the motor is tripped by the ZSW
function. This protects a completely stalled motor from being damaged when the LAT timer
blocks the locked-rotor thermal trip.
CAUTION
The Long Acceleration Time (LAT) function is capable of blocking the critical LRC-LRT rotor
thermal protection during a start and destroying the motor. Turn LAT OFF unless absolutely
needed, and motor suitability for this starting duty has been confirmed. Use ONLY with Zero-
Speed Switch function ZSW ON and switch input connected, to protect a stalled motor.
5.5.11 Setpoint P5L11, Zero Speed Switch On or Off (ZSW ON or ZSW OFF) —
Enables the
function which checks to see if the motor begins to physically spin after a start. Requires a zero-
speed switch on the motor which is closed at rest, and opens as the rotor begins to turn.
Connect the zero-speed switch contact to MP-3000 Discrete Input 1. If the contact fails to open
within LRT/2 (one half of locked-rotor time setting P1L3) after a start, the relay trips with a zero-
speed switch trip message.
Summary of Contents for MP-3000
Page 18: ...Page 18 I L 17562 PR 0 3 Effective 8 99 Figure 4 1 MP 3000 Pushbuttons...
Page 19: ...I L 17562 Page 19 PR 0 3 Effective 8 99 Figure 4 2 MP 3000 LED Indicators...
Page 72: ...Page 72 I L 17562 PR 0 3 Effective 8 99 Figure 6 1 Panel Cutout Dimensions...
Page 73: ...I L 17562 Page 73 PR 0 3 Effective 8 99 Figure 6 2 Faceplate Dimensions...
Page 74: ...Page 74 I L 17562 PR 0 3 Effective 8 99 Figure 6 3 MP 3000 Case Depth Dimensions...
Page 75: ...I L 17562 Page 75 PR 0 3 Effective 8 99 Figure 6 4 Universal RTD Module Mounting Dimensions...
Page 76: ...Page 76 I L 17562 PR 0 3 Effective 8 99 Figure 6 5 Rear Panel Terminals...
Page 78: ...Page 78 I L 17562 PR 0 3 Effective 8 99 Figure 6 7 Typical ac Supply and URTD Wiring...
Page 79: ...I L 17562 Page 79 PR 0 3 Effective 8 99 Figure 6 8 Alternatives for Discrete Input Wiring...
Page 80: ...Page 80 I L 17562 PR 0 3 Effective 8 99 Figure 6 9 RTD Wiring to URTD Module...
Page 100: ...Page 100 I L 17562 PR 0 3 Effective 8 99 Figure 9 1 Rotor Temperature Tracking...
Page 101: ...I L 17562 Page 101 PR 0 3 Effective 8 99 Figure 9 2 Motor Protection Curve...
Page 102: ...Page 102 I L 17562 PR 0 3 Effective 8 99 Figure 9 3 Underload Jam Protection Curve...
Page 104: ...Page 104 I L 17562 PR 0 3 Effective 8 99 Figure 9 5 Motor Protection Curve Example with RTDs...
Page 105: ...I L 17562 Page 105 PR 0 3 Effective 8 99 Figure 9 6 Motor Start and Run Cycles...
Page 109: ...I L 17562 Page 109 PR 0 3 Effective 8 99 P5L8 40 Incomplete Sequence time 1 60s OFF 1 240s...