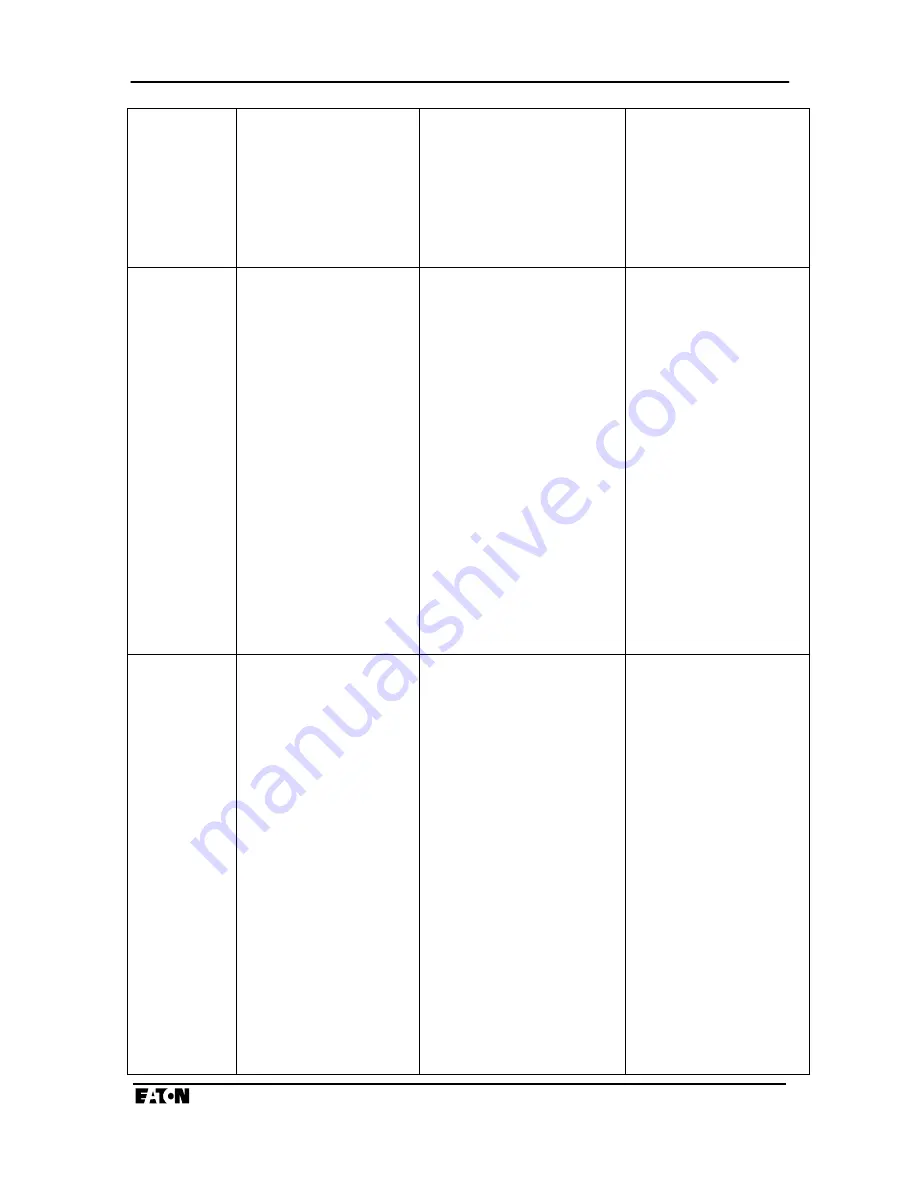
Page 120
I.L. 17562
PR 0.3 Effective 8/99
(emptied) below the user-set
I2T alarm level. This time
depends on motor
nameplate values entered
as setpoints.
in supply currents or
voltages causing
negative-sequence
heating.
•
Check for abnormal
system voltage level.
•
Check for cooling air
blockage or abnormal
ambient.
INC SEQ
INCOMPLETE
SEQUENCE TRIP
Discrete input 2 has been
set for the incomplete
sequence timing function
via setpoint P7L1. The 120
Vac feedback signal from
the process or starter,
expected within the user-set
time delay, was not
received in time after the
start or transition.
Also, the discrete input 2
must remain energized
during the run cycle, until
the motor stops. An
interruption over 25 cycles
will cause an incomplete
sequence trip.
•
Check to be sure this
function has been
intentionally enabled.
•
Check process
feedback wiring to be
sure 120 Vac signal is
delivered in the
expected time.
•
Use DI 2 test to
confirm that relay sees
input.
•
Check setpoint P5L8
against process
feedback time.
•
Check setpoint P5L9
to be sure correct timing
start point is selected -
start or transition.
•
If timing from
transition, be sure
transition current and
time settings are correct.
ZSW TRIP
ZERO SPEED SWITCH
INPUT FAILED TO BE
FALSE WITHIN 1/2 OF
LOCKED ROTOR TIME,
OR WAS FALSE AT
START.
Discrete input 1 has been
set for zero-speed switch
sensing via setpoint P6L1.
The 120 Vac zero speed
switch contact input was not
present at the moment of
the start; or it did not go
away in one-half of the set
locked rotor or stall time
P1L3. This may be due to a
motor which is unable to
start spinning when it is
energized.
•
Check to be sure this
function has been
intentionally enabled.
•
If ZSW trip occurs at
the moment of starting,
check process wiring
and contact to be sure
120 Vac signal is
delivered to DI 1 when
the motor is stopped.
•
Check to be sure the
motor isn't stalled and
actually begins to spin.
•
If ZSW trip occurs
after 1/2 the locked rotor
time setting, check to be
sure the contact on the
motor opens and the 120
Vac signal goes away
before this time.
Usually, a zero-speed
switch should open when
the motor has reached
5% to 10% of its normal
Summary of Contents for MP-3000
Page 18: ...Page 18 I L 17562 PR 0 3 Effective 8 99 Figure 4 1 MP 3000 Pushbuttons...
Page 19: ...I L 17562 Page 19 PR 0 3 Effective 8 99 Figure 4 2 MP 3000 LED Indicators...
Page 72: ...Page 72 I L 17562 PR 0 3 Effective 8 99 Figure 6 1 Panel Cutout Dimensions...
Page 73: ...I L 17562 Page 73 PR 0 3 Effective 8 99 Figure 6 2 Faceplate Dimensions...
Page 74: ...Page 74 I L 17562 PR 0 3 Effective 8 99 Figure 6 3 MP 3000 Case Depth Dimensions...
Page 75: ...I L 17562 Page 75 PR 0 3 Effective 8 99 Figure 6 4 Universal RTD Module Mounting Dimensions...
Page 76: ...Page 76 I L 17562 PR 0 3 Effective 8 99 Figure 6 5 Rear Panel Terminals...
Page 78: ...Page 78 I L 17562 PR 0 3 Effective 8 99 Figure 6 7 Typical ac Supply and URTD Wiring...
Page 79: ...I L 17562 Page 79 PR 0 3 Effective 8 99 Figure 6 8 Alternatives for Discrete Input Wiring...
Page 80: ...Page 80 I L 17562 PR 0 3 Effective 8 99 Figure 6 9 RTD Wiring to URTD Module...
Page 100: ...Page 100 I L 17562 PR 0 3 Effective 8 99 Figure 9 1 Rotor Temperature Tracking...
Page 101: ...I L 17562 Page 101 PR 0 3 Effective 8 99 Figure 9 2 Motor Protection Curve...
Page 102: ...Page 102 I L 17562 PR 0 3 Effective 8 99 Figure 9 3 Underload Jam Protection Curve...
Page 104: ...Page 104 I L 17562 PR 0 3 Effective 8 99 Figure 9 5 Motor Protection Curve Example with RTDs...
Page 105: ...I L 17562 Page 105 PR 0 3 Effective 8 99 Figure 9 6 Motor Start and Run Cycles...
Page 109: ...I L 17562 Page 109 PR 0 3 Effective 8 99 P5L8 40 Incomplete Sequence time 1 60s OFF 1 240s...