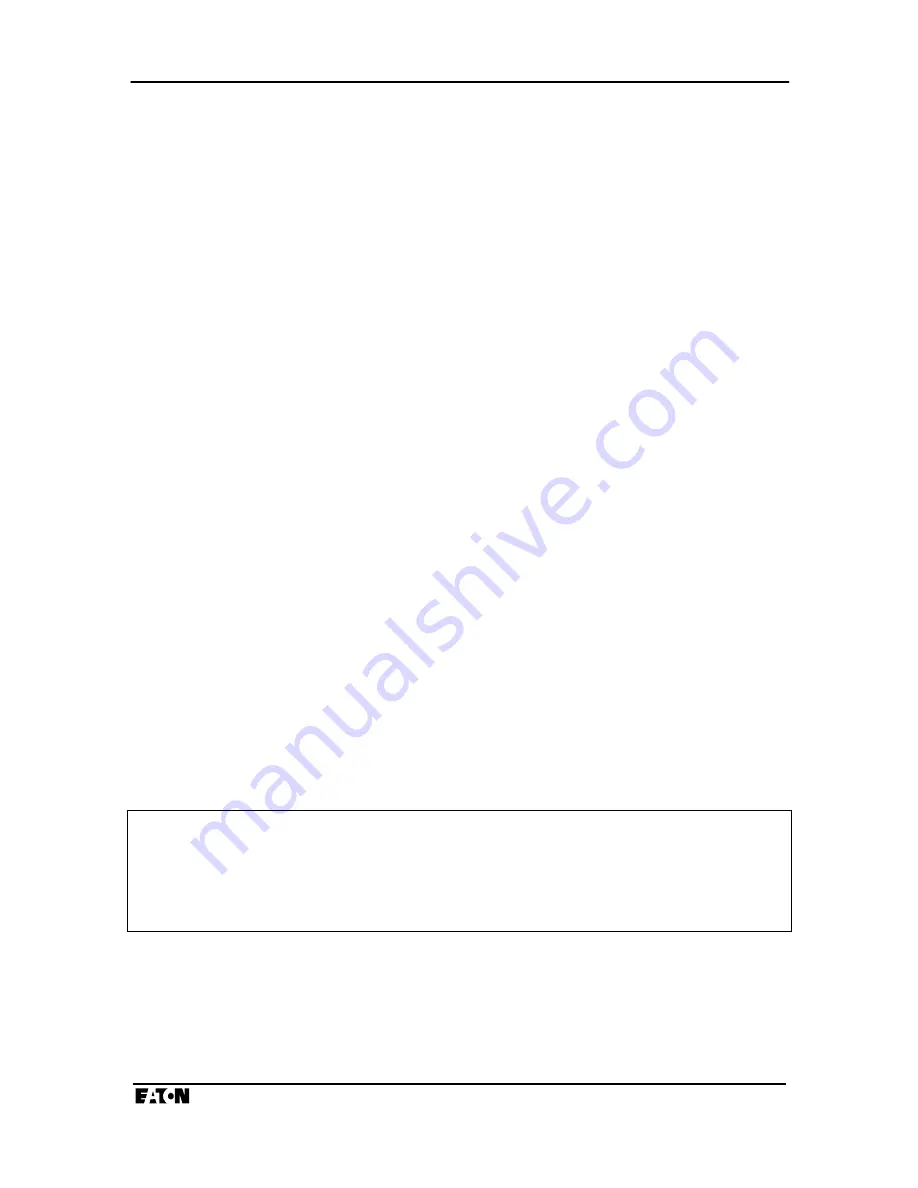
Page 56
I.L. 17562
PR 0.3 Effective 8/99
5.5.4 Setpoint P5L4, Number of Cold Starts Allowed (NOCS) —
Sets the number of cold
starts allowed from 1 to 5. Most motors can tolerate some number of consecutive cold starts
before the time between starts is enforced. The MP-3000 treats a start as the first in a sequence
of cold starts if the motor has been stopped for at least the time period which is the
greatest
of:
•
Setpoint P5L2, Time Allowed For Starts Count (T/ST).
•
Setpoint P5L3, Time Between Starts (TBS)
•
One hour.
Subsequent starts are treated as additional cold starts in the same sequence only if they follow
the previous start by ten minutes or less, until the set number of cold starts is reached. Starts
after this are subject to time and count limits imposed by settings P5L1 through P5L3 above.
5.5.5 Setpoint P5L5, Motor Start Transition Current Level (TRNC) —
Sets the current level
defining the transition from the START to the RUN state. This setpoint, with setpoints P5L6 and
P5L7, determine when the MP-3000 declares a transition from START to RUN..
5.5.6 Setpoint P5L6, Motor Start Transition Timeout (TRNT)
— Sets the maximum duration
of the START state of the motor before transition to RUN. See P5L7 for further explanation.
5.5.7 Setpoint P5L7, Transition on Event (TRN TIME, TRN I, TRN T+C, or TRN T/C) —
This
setpoint is used with P5L5 and P5L6 to determine what events must happen for the MP-3000 to
declare a transition from START to RUN. Select one of four choices:
TRN TIME — Transition to RUN after time setting (P5L6) only. Ignore current.
TRN I — Transition when starting current drops below setting (P5L5) only. If the time set in
TRNT P5L6 expires before the current transition, trip the motor.
TRN T+C — Transition on time or current, whichever comes first.
TRN T/C — Transition on time and current. Both must occur, and the current must drop below
the setting before the time delay expires. If the timer expires before the current falls below the
set transition level, trip the motor.
In addition, the MP-3000 provides a transition control signal to a reduced-voltage starter,
allowing it to raise the voltage to the running value. To do this, the transition function activates
the contact output AUX2 (unless the function of AUX2 has been redefined by setting changes in
the AUX2 configuration settings page, Page 10).
NOTE
Even if the transition control output is not used, set the transition function to provide clear
indications of the actual state of the motor (START; RUN) on the front-panel display and via data
communications. A good way to do this is to use the factory default settings of P5L7 = TRN I
and P5L5 = 130% of FLA. Modify the latter, if needed, to lie at a transition value between the
starting current and post-start maximum load current.
5.5.8 Setpoint P5L8, Incomplete Sequence Report Back Time (INSQ) —
Sets the required
process report-back time in seconds. This function can be set to OFF.
The incomplete-sequence function requires a report-back contact from the process which the
motor runs - any indication that the process has proceeded to operate as expected some time
after the motor start. If the process doesn't start up correctly, the contact doesn't close within the
Summary of Contents for MP-3000
Page 18: ...Page 18 I L 17562 PR 0 3 Effective 8 99 Figure 4 1 MP 3000 Pushbuttons...
Page 19: ...I L 17562 Page 19 PR 0 3 Effective 8 99 Figure 4 2 MP 3000 LED Indicators...
Page 72: ...Page 72 I L 17562 PR 0 3 Effective 8 99 Figure 6 1 Panel Cutout Dimensions...
Page 73: ...I L 17562 Page 73 PR 0 3 Effective 8 99 Figure 6 2 Faceplate Dimensions...
Page 74: ...Page 74 I L 17562 PR 0 3 Effective 8 99 Figure 6 3 MP 3000 Case Depth Dimensions...
Page 75: ...I L 17562 Page 75 PR 0 3 Effective 8 99 Figure 6 4 Universal RTD Module Mounting Dimensions...
Page 76: ...Page 76 I L 17562 PR 0 3 Effective 8 99 Figure 6 5 Rear Panel Terminals...
Page 78: ...Page 78 I L 17562 PR 0 3 Effective 8 99 Figure 6 7 Typical ac Supply and URTD Wiring...
Page 79: ...I L 17562 Page 79 PR 0 3 Effective 8 99 Figure 6 8 Alternatives for Discrete Input Wiring...
Page 80: ...Page 80 I L 17562 PR 0 3 Effective 8 99 Figure 6 9 RTD Wiring to URTD Module...
Page 100: ...Page 100 I L 17562 PR 0 3 Effective 8 99 Figure 9 1 Rotor Temperature Tracking...
Page 101: ...I L 17562 Page 101 PR 0 3 Effective 8 99 Figure 9 2 Motor Protection Curve...
Page 102: ...Page 102 I L 17562 PR 0 3 Effective 8 99 Figure 9 3 Underload Jam Protection Curve...
Page 104: ...Page 104 I L 17562 PR 0 3 Effective 8 99 Figure 9 5 Motor Protection Curve Example with RTDs...
Page 105: ...I L 17562 Page 105 PR 0 3 Effective 8 99 Figure 9 6 Motor Start and Run Cycles...
Page 109: ...I L 17562 Page 109 PR 0 3 Effective 8 99 P5L8 40 Incomplete Sequence time 1 60s OFF 1 240s...