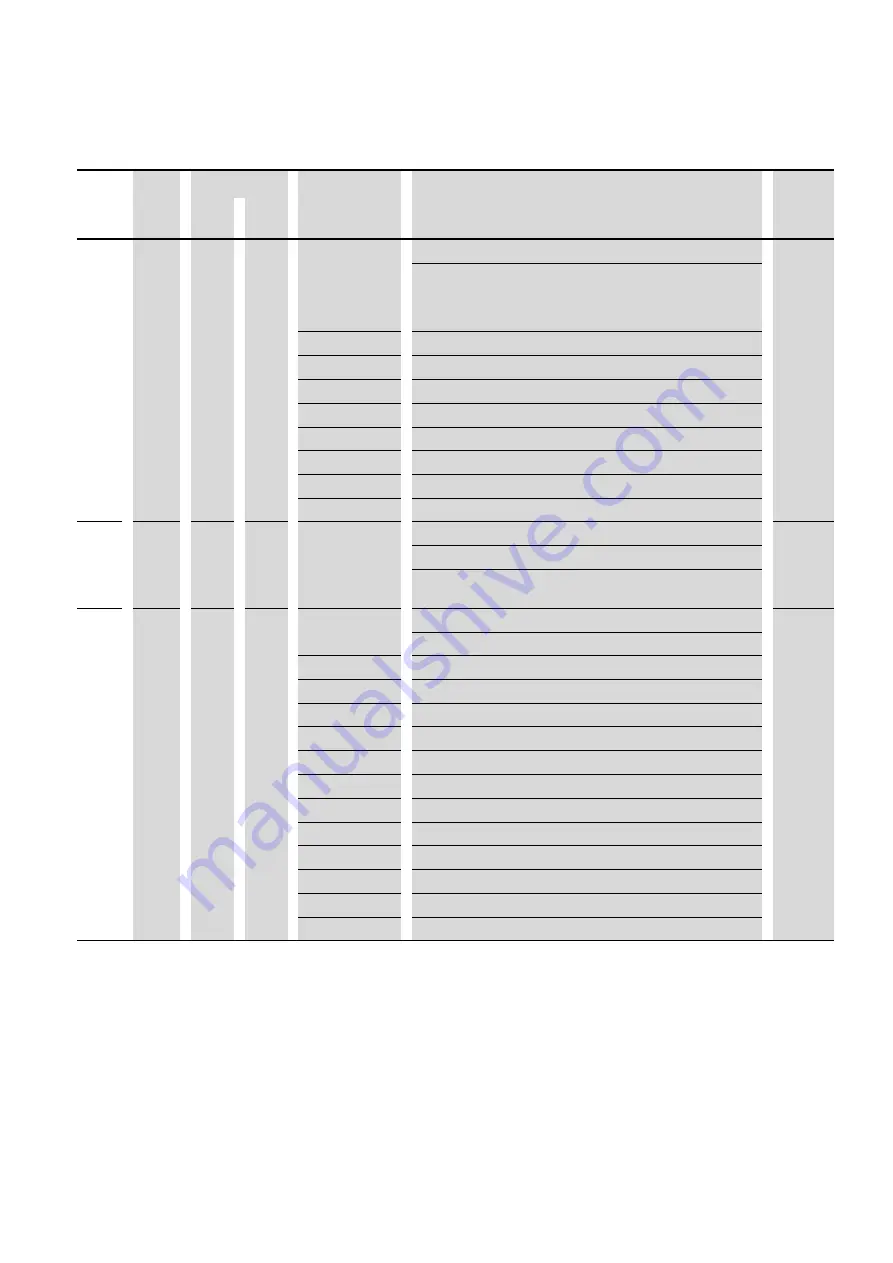
6 Parameters
6.2 Digital and analog inputs
DC1 Frequency Inverter
10/12 MN04020003Z-EN
www.eaton.com
117
PNU
ID
Access rights
Value
Description
DS
RUN
ro/rw
P-18
146
✓
rw
K1 signal (Relay Output 1)
0
Used to select the function assigned to the relay output.
The relay has two output terminals: Logic 1 indicates that the relay is
active: This is why terminals 10 and 11 are connected to each other.
Output terminals; logic 1 indicates that the relay is active.
0
RUN, enable (FWD, REV)
1
READY, frequency inverter ready for operation
2
Output frequency = frequency reference value
3
Error message (frequency inverter not ready)
4
Output frequency
≧
limit value (P-19)
5
Output current
≧
limit value (P-19)
6
Output frequency < limit value (P-19)
7
Output current < limit value (P-19)
P-19
147
✓
rw
K1-Limit value (relay)
100.0
P-02 - 200.0 %
The adjustable limit value that is being used in connection with
settings 4 to 7 of P-18 and P-25
P-25
153
✓
rw
AO1 signal (Analog Output 1)
8
Analog output
→
0 - 10 V DC (value 8 / 9)
8
Output frequency f-Out
→
0 - 100 % f
max
(P-01)
9
Output current
→
0 - 200 % I
e
(P-08)
Switch to digital output
DA4 (Digital output)
→
+24 V DC (Values 0 - 7)
0
RUN (Frequency inverter released and running / FWD, REV)
1
READY, frequency inverter ready for operation / no faults
2
Output frequency = frequency reference value
3
Error message (frequency inverter is not ready)
4
Output frequency
≧
limit value (P-19)
5
Output current
≧
limit value (P-19)
6
Output frequency < limit value (P-19)
7
Output current < limit value (P-19)
Summary of Contents for DC1-12011 Series
Page 1: ...Manual PowerXL DC1 Frequency Inverter 10 12 MN04020003Z EN...
Page 4: ...II...
Page 12: ...0 About this manual 0 5 Units 8 DC1 Frequency Inverter 10 12 MN04020003Z EN www eaton com...
Page 190: ...9 Appendix 9 9 Sinusoidal filter 186 DC1 Frequency Inverter 10 12 MN04020003Z EN www eaton com...