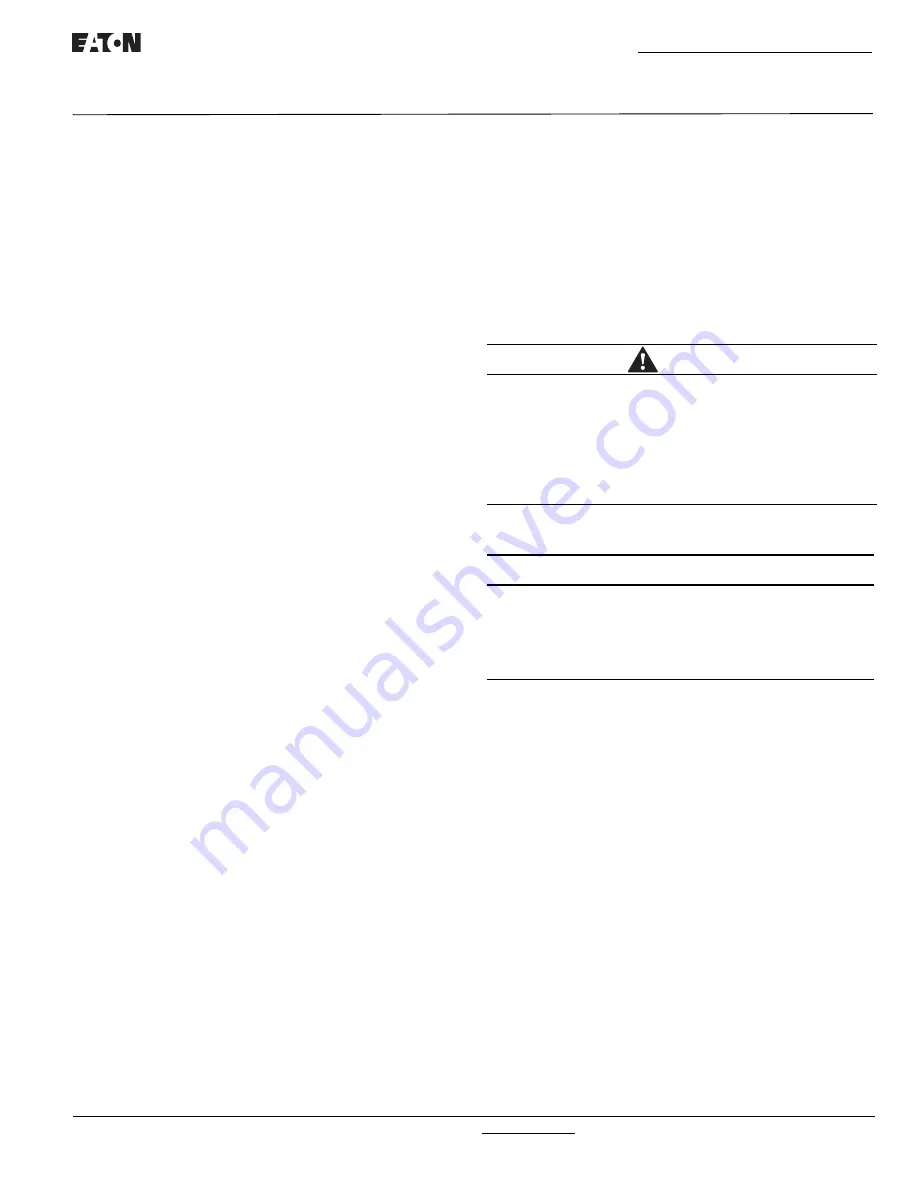
IB140024EN
For more information visit: www.eaton.com
Instruction Booklet
Effective: October 2014
Page
21
ATC-300/900 40-400A (480/600Vac)
3-Postion Contactor Based Transfer Switch
5.3 Automatic Transfer
The operating sequence of an ATS is dictated by the switch's
standard features and selected options. Operation of an ATS
during Source 1 power source failure and Source 1 power source
restoration will be described here with only standard options
included on the switch. Additional options, as described in Sec-
tion 3, can change sequences and timing, depending upon the
options selected. It is strongly suggested that you become famil-
iar with additional options selected with the particular ATS and
their effect on the normal operation of an ATS.
5.3.1 Source 1 Power Source Failure
Standard Source 1 power source failure is defined as a reduction
or loss of voltage. If this occurs, the sequence of operation is as
follows.
1. Failure of Source 1 is detected by the controller intelligence.
2. When the controller detects a failure, the engine contacts
close (after delay if programmed) and start the engine-driven
generator.
3. When the Source 2 voltage reaches its operation rating, the
K2 and K4 relays inside ATC 300 controller operate to start
transfer operation to Source 2. This operating sequence
causes the contactor to open Source 1 and close on
Source 2.
4. The load is now transferred to the Source 2 power source.
5.3.2 Source 1 Power Source Restoration
1. A return to the Source 1 power source begins when the volt-
age in all phases of a 3-phase sensing unit, or phase-to-
phase in a single sensing unit, is restored to a preset value.
2. At the preset voltage, K1 and K3 relays inside ATC 300 con-
troller operate to start transfer operation to Source 1.
3. During this sequence, the contactor opens Source 2 and
closes on Source 1.
4. Simultaneously, the engine cool-down timer initiates the shut
down of the engine driven generator.
5. Transfer of the load back to the Source 1 power source is
now complete.
Section 6: Testing and Problem Solving
6.1 Testing
After the ATS equipment is initially installed or during planned
outages, the installation should be tested to ensure that all equip-
ment operates properly. This attention to detail will help avoid
unexpected malfunctions. Mechanical and/or electrical tests
should be performed as described in this section.
The frequency of subsequent testing should be based on recom-
mendations of the Genset manufacturer. Use the test pushbut-
ton to check the electrical operation of the switch.
WARNING
HIGH VOLTAGES ASSOCIATED WITH OPERATIONAL TRANSFER
SWITCH EQUIPMENT PRESENT A SHOCK HAZARD THAT CAN
CAUSE SEVERE PERSONAL INJURY OR DEATH. USE EXTREME
CAUTION TO AVOID TOUCHING ELECTRICAL CONNECTIONS
WHENEVER INSPECTING OR TESTING THE EQUIPMENT.
IN ADDITION, IMPROPER OPERATION OF THE GENERATOR SET
PRESENTS A HAZARD THAT CAN CAUSE SEVERE PERSONAL
INJURY OR DEATH. OBSERVE ALL SAFETY PRECAUTIONS IN YOUR
GENERATOR SET OPERATIONS AND INSTALLATION MANUALS.
6.1.1 Mechanical and/or Electrical Testing
NOTICE
SINCE FEATURE 4 (TIME DELAY ENGINE COOL-OFF), AS
DESCRIBED IN SECTION 3, IS A STANDARD FEATURE, AN ENGINE
START SIGNAL WILL BE PRESENT FOR A PERIOD OF TIME WHEN
THE SWITCH IS FIRST ENERGIZED. THE PERIOD OF TIME IS EQUAL
TO THE TIMER SETTING. TO AVOID STARTING THE ENGINE DUR-
ING THIS TIME PERIOD, TURN THE GENERATOR CONTROLS TO
THE OFF POSITION.
Energize the ATS equipment as described iin the following sec-
tions. Insure that all safety precautions are taken and that all
WARNINGS
and
CAUTIONS
are observed.
6.1.2 No Voltage Steps
With no voltage available on either power source, proceed as fol-
lows.
Step 1:
The generator engine start controls should be in the OFF
position to prevent an undesired start.
Step 2:
Ensure that the ATS has been set to the proper applied
system voltage (See Section 4.7).
Step 3:
Check all ATS loads to ensure that they are ready to be
energized.
6.1.3 Connecting the Power Sources
Step 1:
Close the Source 1 power source upstream protection
device.
Step 2:
Connect the engine start battery cable.
Step 3:
With the emergency generator in the OFF position, close
the Source 2 power source upstream protective device,
assuming such a device used.