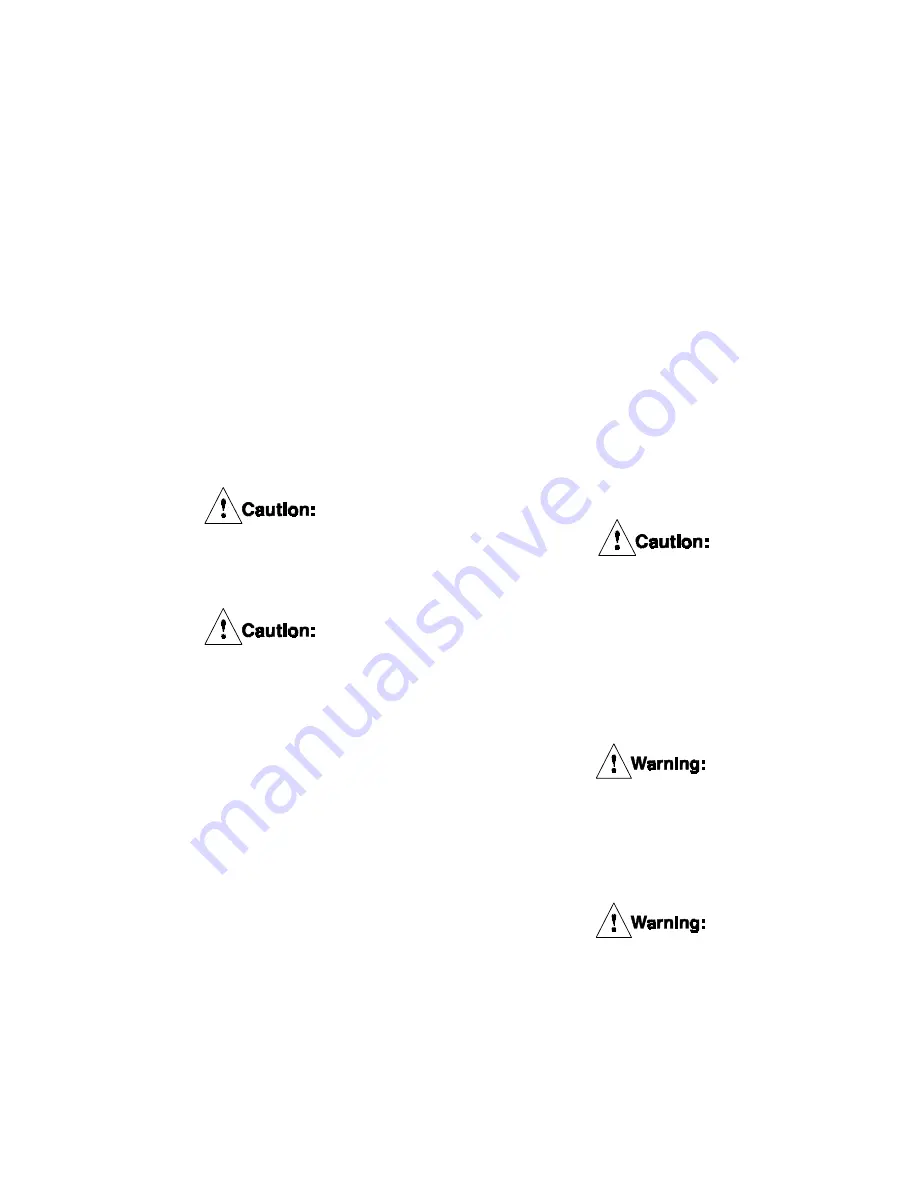
4.2.6
While supporting the cylinder, loosen the
locknuts (18) ONE TURN AT TIME and in an
alternating (crossw ise) pattern until the spring
force is completely relieved. Remove the
locknuts and w ashers (17). Mark all of the
w ater outlet ports for identification. Deep w ell
sockets are required. See table 9 for size and
depth of socket required.
4.2.7
Using lifting equipment, carefully remove the
cylinder (19) and piston (33) as an assembly.
Set aside in a clean area.
Note: If a stud (6) should happen to come
loose, remove it completely, clean the threads
on the stud and the threads in the mounting
flange. Apply Locquic
®
Primer Grade " T" to the
stud threads. After the threads have dried,
assemble to the mounting flange using Loctite
®
#262. The end of the stud must not extend
past the mounting surface of the mounting
flange.
Loctite
®
#262 must be shaken prior to
application.
Loctite
®
#262 may irritate sensitive skin.
Refer to the product label for proper
safety precautions.
4.2.8
Using lifting equipment, remove the pressure
plate assembly (13) and carefully place it on a
suitable w ork surface w ith the w ear plate (3)
facing up. Do not damage the w ear plate.
4.2.9
Remove the friction disc assembly, the
reaction plate assembly (30) and the release
springs (34) and set aside.
4.2.10
Slide the clamp tubes (12) off of the studs.
Remove one w ear spacer from each stud.
Reinstall the clamp tubes and set aside the
removed w ear spacers.
4.2.11
Place a release spring over every other clamp
tube and slide the reaction plate assembly
onto the clamp tubes.
4.2.12
Slide the friction disc assembly onto the gear.
4.2.13
For multi-disc units, repeat steps 4.2.5.7 and
4.2.5.8 for each additional friction disc and
reaction plate.
4.2.14
Place a release spring on every other clamp
tube and slide the pressure plate and the
cylinder/piston assembly onto the studs.
4.2.15
Lubricate the threads on the end of the studs
w ith 30 w t. oil or anti-seizing compound and
install the locknuts (18) w ashers (17) and the
w ear spacers removed in 4.2.5.6.
4.2.16
The w ear spacers are " stored" under the
locknuts for use after replacing the friction
discs. See Figure 12.
4.2.17
While supporting the w eight of the
cylinder/piston assembly, tighten the locknuts,
ONE TURN AT A TIME and in an alternating
(crossw ise) pattern until the cylinder is seated
firmly against the clamp tubes. Torque the
locknuts to the appropriate value. See Table 4.
The locknuts (18) must be tightened
gradually to prevent damage to the
tensioner components.
4.2.18
Reinstall the air and coolant lines per 2.0.
5.0
DISASSEM BLY, INSPECTION
& ASSEM BLY
Before doing any maintenance work on
the WCB unit, make sure that the
machinery will remain in a safe position.
Failure to do so could result is serious
injury or possibly death.
Only qualified maintenance personnel
should install, adjust or repair these
WCB units. Faulty workmanship will
result in unreasonable exposure to
hazardous conditions or personal injury.
PDF FORMAT
20
© Copyright Eaton Corp., 1995. All rights reserved.
Summary of Contents for 146246A
Page 5: ...18 24 36 WCB Single Disc Figure 4 PDF FORMAT 4 Copyright Eaton Corp 1995 All rights reserved ...
Page 6: ...18 24 36 WCB Dual Disc Figure 5 PDF FORMAT 5 Copyright Eaton Corp 1995 All rights reserved ...
Page 7: ...18 24 36 WCB Triple Disc Figure 6 PDF FORMAT 6 Copyright Eaton Corp 1995 All rights reserved ...
Page 8: ...Figure 7 18 24 36 WCB Quad Disc PDF FORMAT 7 Copyright Eaton Corp 1995 All rights reserved ...