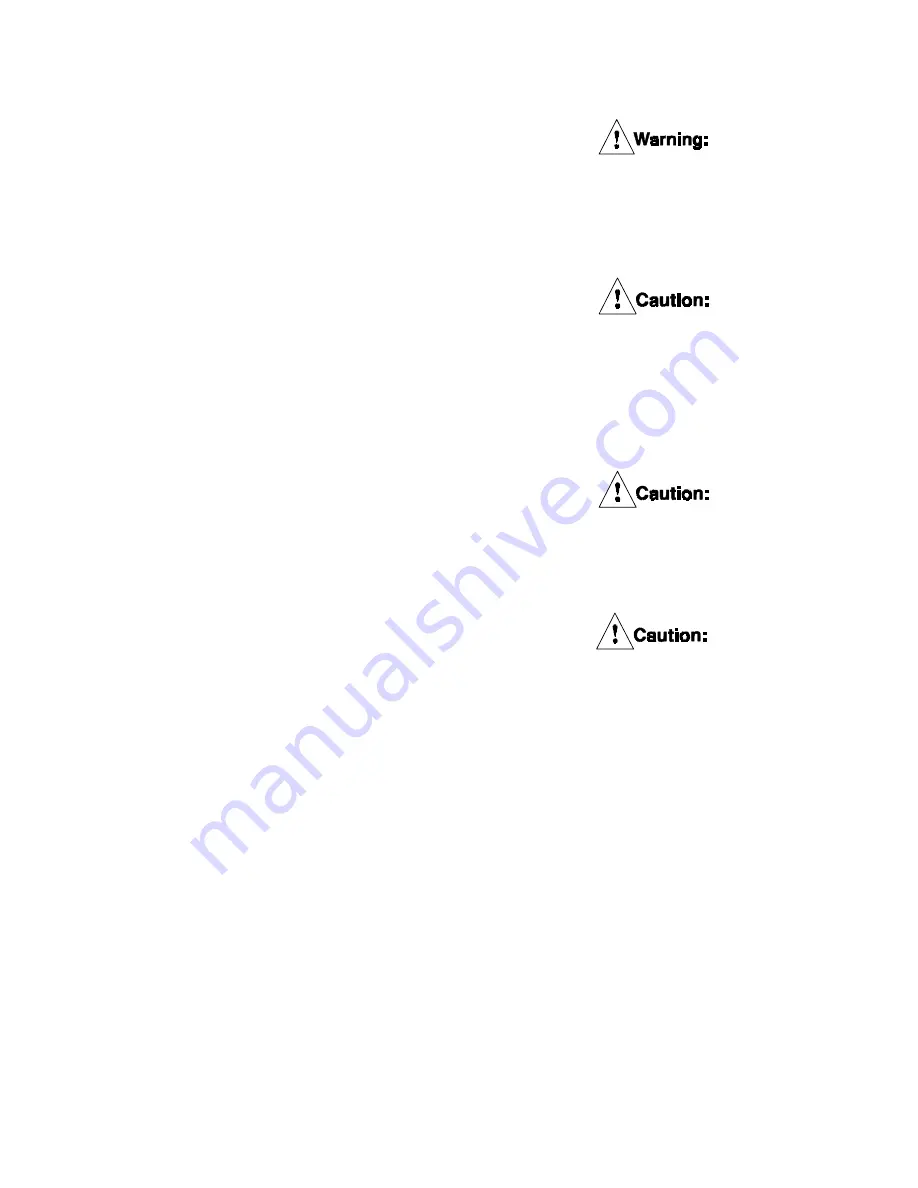
1.2.4
114 WCB Models w ith " H" (146XXXH)
designator have a special friction disc core for
mating w ith a 112.5 WC gear. The friction
disc core (9) P/N is 416126 and the friction
disc sub-assembly (7) P/N is 416125, all other
parts are the same as the " B" model WCB.
1.2.5
WCB models w ith " J" (146XXXJ) designator
have Corrosion Resistant Pistons and Standard
screw ed on friction linings. Contact
Airflex for piston (33) P/N’s.
1.2.6
WCB models w ith " K" (146XXXK) designator
have Corrosion Resistant Pistons and High
Coefficient screw ed on friction linings(8). Call
Airflex for piston (33) P/N’s.
1.2.7
WCB models w ith part list numbers, not just
alphanumeric designator, other than listed on
cover use WC 11040.
1.3
Upgrades
1.3.1
18, 24 and 36 WCB elements ending w ith a
" B" (146XXXB) alphanumeric designators
have been discontinued, how ever, existing
models may be upgraded to new standards.
To upgrade the element you must change the
friction disc subassembly w ith cores having
screw ed on linings. See table X, all disc’s must
be changed. Also stop tubes (59) & (80), w ear
rings (58) must be installed. See the part list in
section 9.0 for part numbers and quantities for
the individual elements.
Note: If these changes have been made stamp
out the " B" letter designator and stamp the
" E" designator.
1.4
How It Works
1.4.1
Refer to Figure 1. Air is introduced to the unit
causing the pressure plate assembly (13) to
move and make contact w ith the friction discs
(8). Torque is transmitted through the studs (6)
to the mounting flange (2). The release springs
(34) assist in disengagement and retraction of
the piston and pressure plate. High heat
dissipation is accomplished by passing w ater
through a special cavity behind copper w ear
plates (3).
2.0
INSTALLATION
Only qualified maintenance personnel
should install, adjust or repair these
units. Faulty workmanship will result in
unreasonable exposure to hazardous
conditions or personal injury.
Read these instructions thoroughly and
review until you fully understand the
installation sequence before proceeding
with the work described in this section.
Failure to follow these instructions will
result in unreasonable exposure to
hazardous conditions or personal injury.
Do not paint the clamp tubes (12) or
the springs (34), as this may hinder the
engagement or disengagement of the
tensioner.
Maximum ambient temperature is 110
o
F
(43
o
C ). Minimum ambient temperature
for closed loop systems using ethylene
glycol antifreeze is 0
o
F (-18
o
C). For open
loop systems using water, the minimum
temperature is 45
o
F (7
o
C).
Note: Some three and four disc units may
require support on the cylinder end of the
tensioner in certain high torque applications.
Contact the factory for specific application
information.
2.1
Preparation
2.1.1
Table 2 show s the relationship betw een the
tensioner mounting surface and the end of the
gear (dimension " A" on Figure 1, 3-6 ). The
gear is bored and keyed for a resulting Class
FN2S interference fit for inch shafting and ISO
System S7h6 for metric shafting.
PDF FORMAT
10
© Copyright Eaton Corp., 1995. All rights reserved.
Summary of Contents for 146246A
Page 5: ...18 24 36 WCB Single Disc Figure 4 PDF FORMAT 4 Copyright Eaton Corp 1995 All rights reserved ...
Page 6: ...18 24 36 WCB Dual Disc Figure 5 PDF FORMAT 5 Copyright Eaton Corp 1995 All rights reserved ...
Page 7: ...18 24 36 WCB Triple Disc Figure 6 PDF FORMAT 6 Copyright Eaton Corp 1995 All rights reserved ...
Page 8: ...Figure 7 18 24 36 WCB Quad Disc PDF FORMAT 7 Copyright Eaton Corp 1995 All rights reserved ...