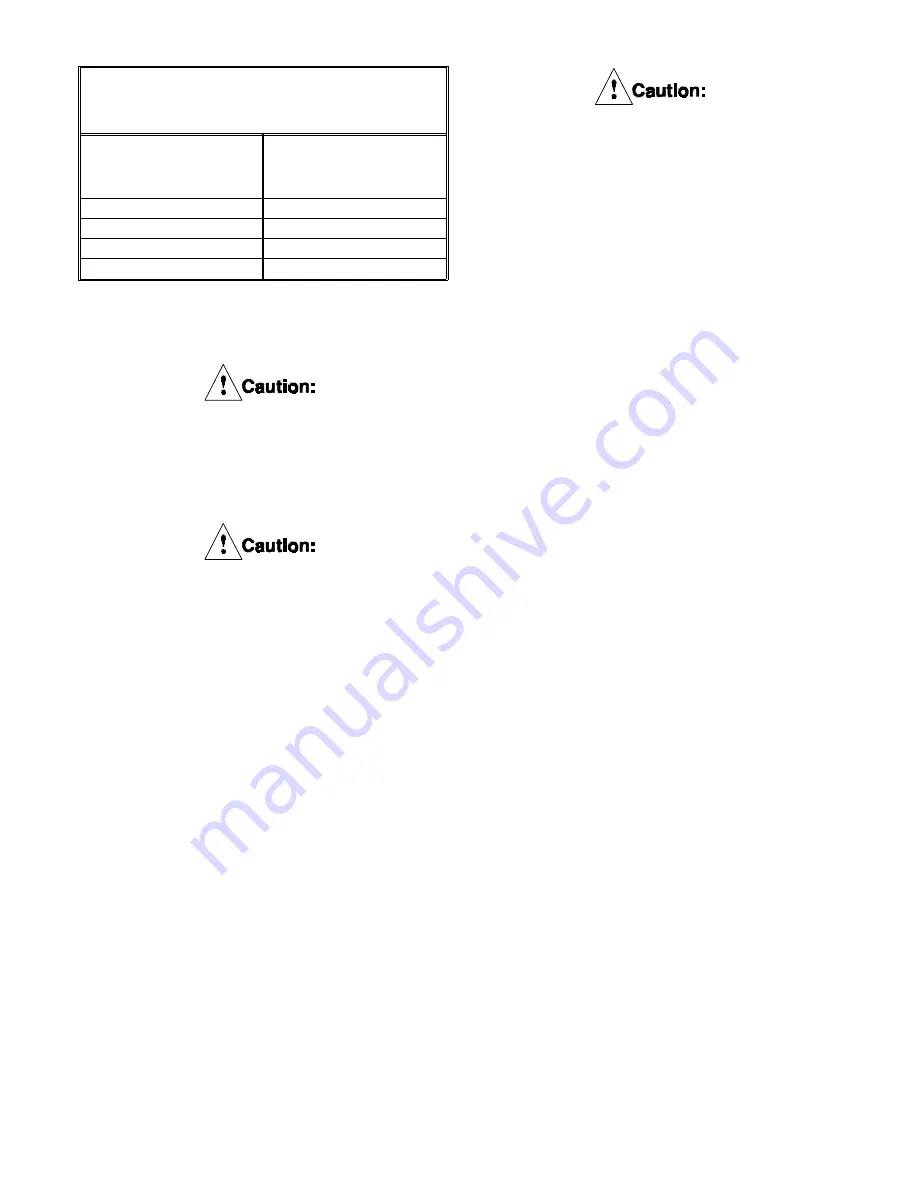
2.5.2
Figure 10 show s the flow control valve settings
for each type of element depending on the
number of friction surfaces to be cooled.
Improper or low coolant temperature can
cause condensation to occur on the
friction surfaces which will affect torque
and wear performances. Coolant should
be shut off when element is not in use.
Make sure that the water inlets and
outlets are at the 6 o’clock and 12
o’clock positions, respectively. This will
ensure that there will be no air pockets in
the water cavity during operation, which
would allow the tensioner to overheat.
2.5.3
The coolant supply and discharge pipe sizes,
along w ith minimum flow rates for the
tensioner rated horsepow er, are given in
Table 6.
2.5.4
Each coolant cavity of each WCB tensioner has
been statically tested at the factory before
shipment. If leakage is suspected, a static or
dynamic test may be made as follow s:
Static Pressure Test:
First, bleed all air from w ithin the coolant
cavity. Air bleeding must be accomplished by
running coolant through the cavity w ith the
tensioner secured in its operating position. Af-
ter the air has been removed, install a pipe plug
in the outlet and apply 45 PSIG (3.1 bar) cool-
ant pressure measured at the inlet to the w ater
cavity. Maintain this pressure for 30
minutes. Check for leakage at O.D. and I.D.
seal areas.
Do not apply air pressure to the
cylinder of the tensioner during static
coolant pressure testing. Surge pressures
exceeding 45 PSIG (3.1 bar) could be
developed within the coolant cavities
which will cause damage to the seals.
Dynamic Flow Test:
Dynamic flow testing of the tensioner should
be conducted at the required flow rate for the
rated HP dissipation and coolant quality, as
given in Table 6. Inlet pressure is not to exceed
45 PSIG (3.1 bar).
There should be no restrictions on the outlet
side of the brake to cause any back pressure to
the unit. Coolant inlet and hose size should be
as given in Table 6. Check for leakage at the
O.D. and I.D. seal areas.
2.5.5
The coolant supply temperature at the inlet
should be 100
o
F (38
o
C) or low er. The coolant
outlet temperature should not exceed the
values given in Table 6. How ever, in no event
should there be more than a 50
o
F (28
o
C)
temperature rise betw een inlet and outlet. See
Table 7 for maximum allow able outlet coolant
temperature w ith a w ater/ethylene glycol mix.
2.5.6
Open Loop Systems
For efficient operation of the WCB, an
adequate supply of filtered fresh w ater is
required. (See 2.5.1-2.5.2). Excessive w ater
hardness promotes the formation of scale
deposits, w hich, in time, w ill affect the service
life of the WCB unit. Water of high acidity may
cause electrolytic corrosion betw een the
dissimilar metals used in the WCB. Water
treatment should be considered if the proper-
ties of the w ater exceed the follow ing:
Equivalent calcium carbonate content
hardness): Maximum 100 p.p.m.
pH value: 7.0 to 9.0.
2.5.7
Closed Loop Systems
For efficient operation of the WCB in a closed
loop system, ethylene glycol coolant conform-
ing to SAE Standard J1034 should be used.
For preparation of the proper concentration of a
w ater/ethylene glycol mixture, use makeup
w ater w hich is low in corrosive ions such as
chlorides and sulfates.
TABLE 7
Maximum Mixture Outlet
Coolant Temperature
Water/Ethylene
Glycol Mixture
% by Volume
Maximum Outlet
Coolant Temperature
o
F (
o
C)
100/0
150 (66)
70/30
165 (74)
60/40
165 (74)
50/50
170 (77)
PDF FORMAT
14
© Copyright Eaton Corp., 1995. All rights reserved.
Summary of Contents for 146246A
Page 5: ...18 24 36 WCB Single Disc Figure 4 PDF FORMAT 4 Copyright Eaton Corp 1995 All rights reserved ...
Page 6: ...18 24 36 WCB Dual Disc Figure 5 PDF FORMAT 5 Copyright Eaton Corp 1995 All rights reserved ...
Page 7: ...18 24 36 WCB Triple Disc Figure 6 PDF FORMAT 6 Copyright Eaton Corp 1995 All rights reserved ...
Page 8: ...Figure 7 18 24 36 WCB Quad Disc PDF FORMAT 7 Copyright Eaton Corp 1995 All rights reserved ...