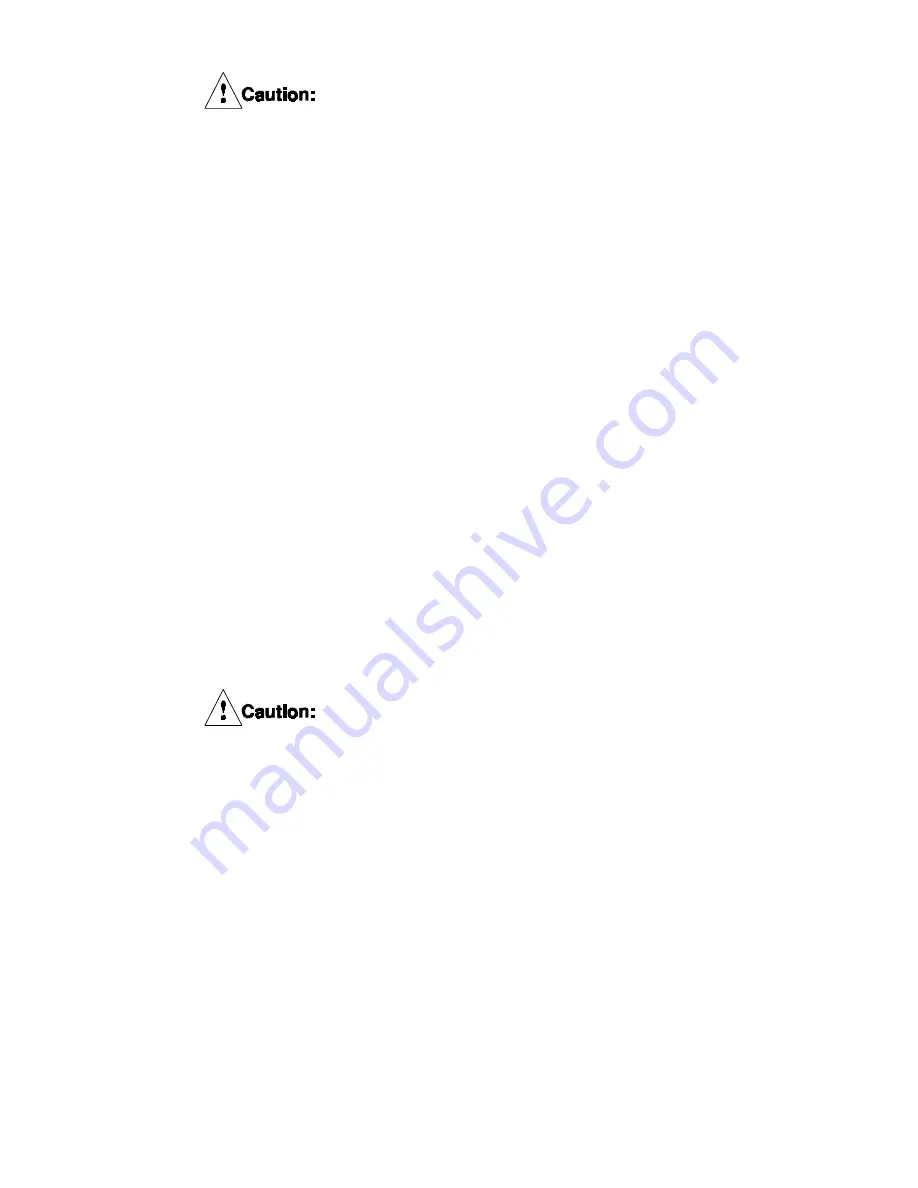
Loctite
®
#262 may irritate sensitive skin.
Refer to the product label for proper
safety precautions.
5.2.3
Using lifting equipment, remove the pressure
plate assembly (13) and carefully place it on a
suitable w ork surface w ith the w ear plate (3)
facing up. Do not damage the w ear plate.
5.2.4
Remove the friction disc assembly, the reac-
tion plate assembly (30), release springs (34),
stop tubes (59) or (80) and w ear rings (58)
(if present) and set aside.
5.2.5
For multi disc units repeat step 5.2.4 for each
reaction plate and friction disc set until all are
removed.
5.2.6
Slide the clamp tubes (12) and w ear
spacers (29) off each of the studs.
5.2.7
Place the cylinder and piston assembly w ith
the piston facing dow n on blocks approxi-
mately 6" (150 mm) high. The blocks must
only contact the cylinder (19) so that the
piston (33) w ill be free to move out of
the cylinder bore.
5.2.8
If a regulated air line is available, the piston
can be partially ejected from the cylinder by
applying no more than 15 PSIG (1.0 bar) to
the cylinder.
Application of a higher pressure may
cause damage to the components.
5.2.9
To complete the removal of the piston from
the cylinder, open all air inlets.Alternately in-
sert a 0.50" (12 mm) diameter by 6" (150
mm) long w ood dow el into each air inlet and
gently tap the piston w ith a mallet so that it
moves evenly out of the cylinder. Be careful
not to damage the sealing surfaces of the pis-
ton or cylinder by cocking the piston in the
cylinder.
5.2.10
Inspect the cylinder sealing surface condition
for nicks or scratches or any other defect
w hich may prevent the seals from being
effective. Refer to the Wear Limit tables in
section 7.0. Replace the cylinder, if necessary.
5.2.11
Noting how the lips of the seals are oriented in
the piston grooves, remove the seals.
5.2.12
Thoroughly clean the seal grooves in the piston
and apply a thin, even coat of Parker " O" Lube
®
to the seal grooves, the seals, the sealing
surfaces of the cylinder and to the chamfer
on the piston.
5.2.13
See section 5.4 for inspection and section 5.5
for assembly.
5.4
Inspection of WCB components
Note: Wear limit tables for the following
paragraphs are in section 7.0.
5.4.1
Inspect the friction disc assemblies (8) for w ear
or contamination. On single and multi-disc
units, the friction material must be replaced
w hen w orn to the bottom of the groove on the
friction lining. See Figure 11.
5.4.2
For friction disc repair see section 6.5 for
elements w ith riveted linings or section 6.4
for elements w ith screw ed-on lining.
5.4.3
Inspect the w ear plate (3) for w ear. Wear plates
must be replaced if they exceed the w ear
limits. See section 6.6 for repair procedures.
5.4.4
Inspect the cylinder (19) seal area. Inspect the
cylinder sealing surface condition for nicks or
scratches or any other defect w hich may
prevent the seals from being effective. Refer
to section 6.1 for repair procedures.
5.4.5
Inspect the reaction hole diameters in the
reaction plate (31) and pressure plate (14).
5.4.6
Inspect the clamp tubes (12) for w ear on the
reaction area.
5.4.7
Inspect the friction disc core (9) and the gear
for excessive backlash.
5.4.8
Inspect the release springs (34) for free height.
5.5
Assembly of WCB 18, 24 & 36 WCB’s
(with Stop Tubes)
Note: Item numbers (#) are show n on
Figures 4, 5, 6 and 7.
5.5.1
Position mounting flange (1) w ith studs (6)
installed, on a level w orking surface, mounting
face dow n.
PDF FORMAT
22
© Copyright Eaton Corp., 1995. All rights reserved.
Summary of Contents for 146246A
Page 5: ...18 24 36 WCB Single Disc Figure 4 PDF FORMAT 4 Copyright Eaton Corp 1995 All rights reserved ...
Page 6: ...18 24 36 WCB Dual Disc Figure 5 PDF FORMAT 5 Copyright Eaton Corp 1995 All rights reserved ...
Page 7: ...18 24 36 WCB Triple Disc Figure 6 PDF FORMAT 6 Copyright Eaton Corp 1995 All rights reserved ...
Page 8: ...Figure 7 18 24 36 WCB Quad Disc PDF FORMAT 7 Copyright Eaton Corp 1995 All rights reserved ...