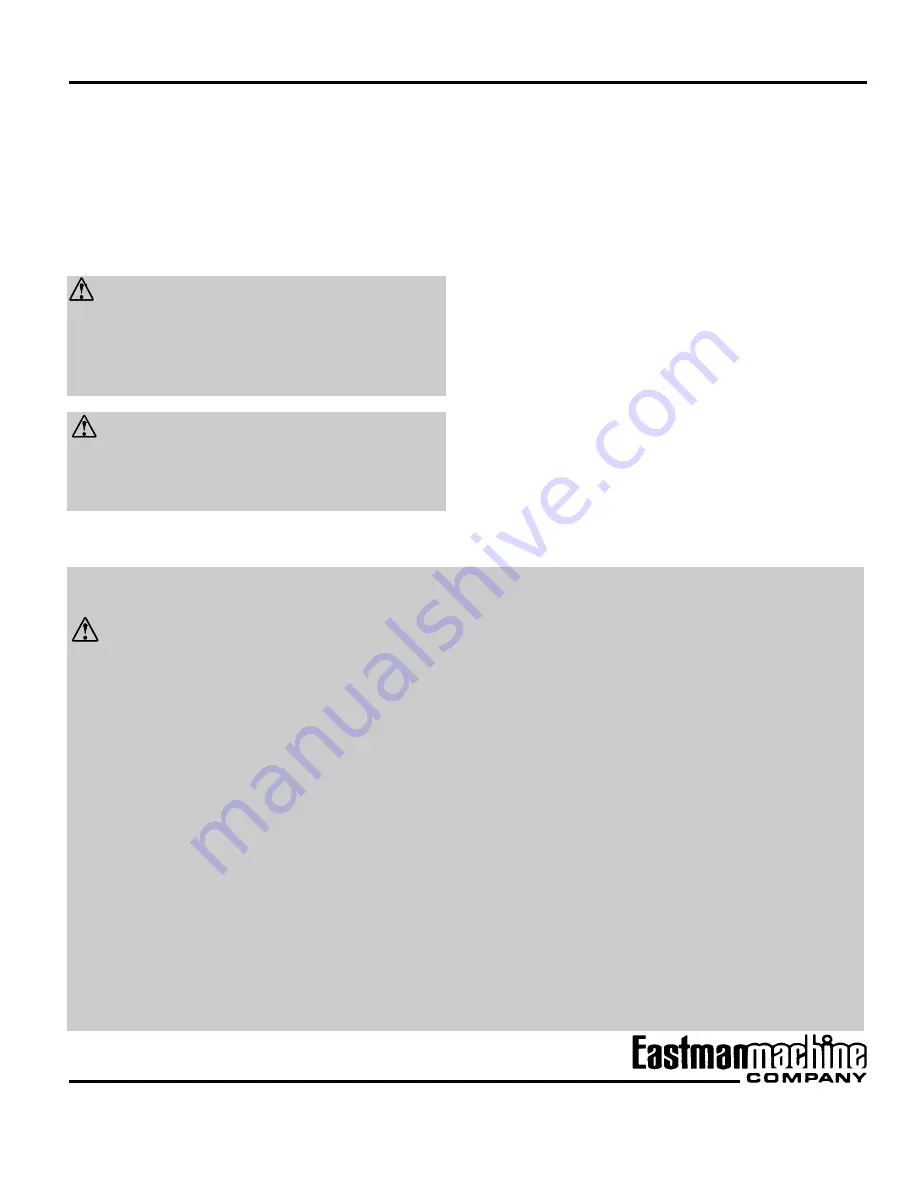
1
Form C-1555
Throughout this manual, safety information is presented by
use of the terms
Warning, Caution,
and
Note.
These terms
have the following meanings:
WARNING
A warning contains critical information regarding poten-
tial safety hazards that can occur during proper use or
misuse of the machine. Failure to follow these proce-
dures may result in serious personal injury to the user.
CAUTION
A caution contains instructions for the use or mainte-
nance of the machine. Failure to follow these procedures
may result in damage to the machine.
Safety and Indemnification
During the life of the machine, the purchaser agrees to pro-
vide to all machine users (including its own employees and
independent contractors) all relevant safety information, in-
cluding warning labels and instruction manuals. The pur-
chaser also agrees to maintain the safety features and work-
ing condition of the machine, and to adequately train all
users in the safe use and maintenance of the machine. The
purchaser agrees to defend, protect, indemnify, and hold
Eastman Machine Company harmless from and against all
claims, losses, expenses, damages, and liabilities to the
extent that they have been caused by the purchaser’s fail-
ure to comply with the terms and instructions of this manual.
Safety Information
• The purchaser must provide appropriate safety mea-
sures and equipment as recommended in this manual.
Observe all statutory requirements concerning the use
of hazardous machinery that apply to your location.
• Do not modify this machine or disable safety fea-
tures. Unauthorized modification may result in seri-
ous personal injuries to the user. Electrical connec-
tions to this machine must be made by a qualified
electrician familiar with applicable codes and regula-
tions. To prevent electrocution, a ground lead must
be connected to terminal “E” on the attachment plug.
• This machine is intended ONLY for hand-held opera-
tion. Misuse of this machine or use of this machine
as part of another machine may result in serious per-
sonal injuries to the user.
• Safety labels must be kept clean and legible at all
times. Call the Eastman Machine factory to order
replacement labels.
WARNING
• This machine is equipped with a very sharp and dan-
gerous knife. Keep hands, arms, and hair away from
the knife area at all times. When the machine is not
in use, keep the pressure foot knife guard lowered
and locked at all times. Safety gloves and glasses
and appropriate clothing may prevent serious personal
injuries.
• Disconnect the power supply from the machine when
it is not in use or during routine maintenance, includ-
ing lubrication.
• The purchaser must instruct all operators in the proper
use of the machine according to the instructions on
the machine and in this manual. This training must
include instruction on the potential safety hazards aris-
ing from the use or misuse of the machine. In addi-
tion to such training, the purchaser should provide
written work instructions as necessary to ensure cor-
rect use of the machine for specific cutting applica-
tions.
General Safety Precautions
Summary of Contents for Blue streak II 629X
Page 1: ......
Page 19: ...15 FormC 1555 Figure 12 Single Phase Electrical Configuration...
Page 40: ......