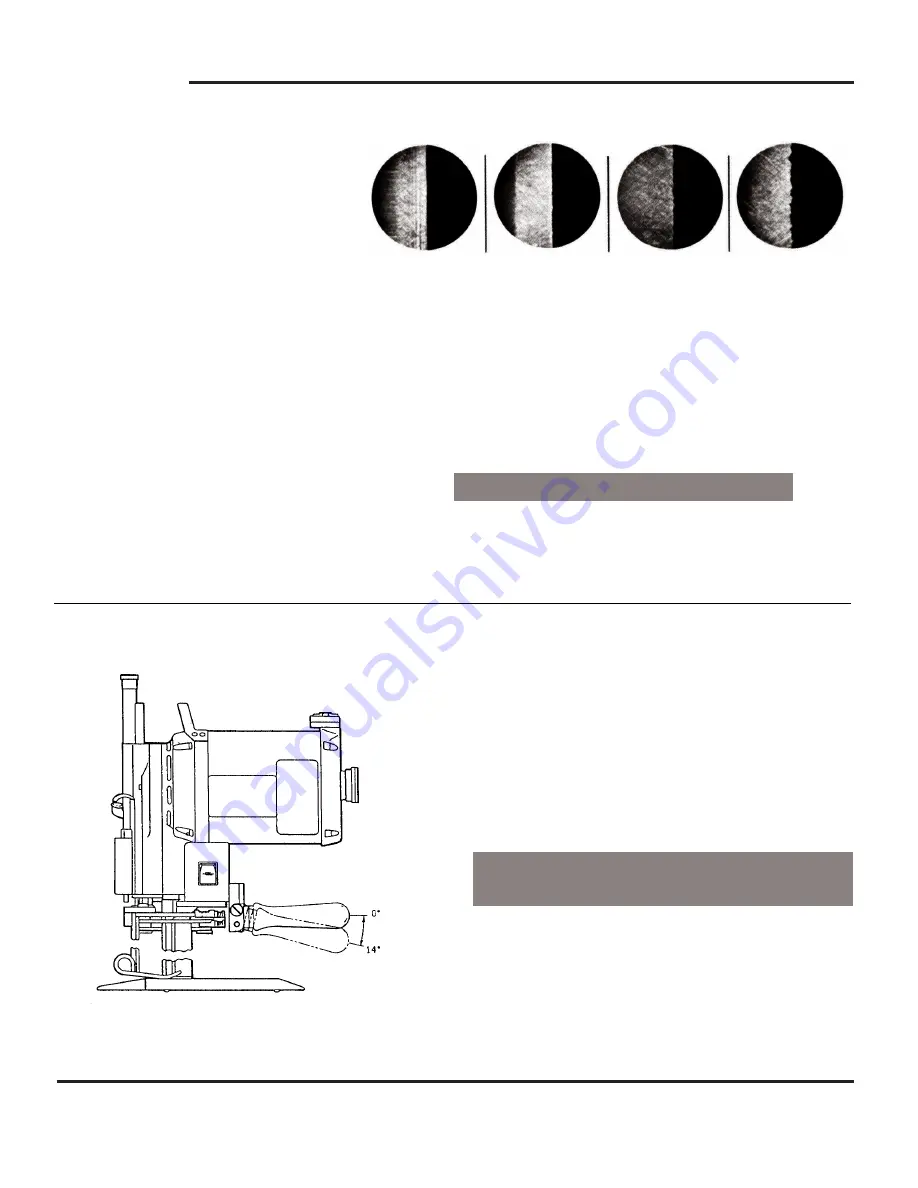
EASTMAN
Form C-1572
The 250X microphotographs (Figure 16)
show four different edges, as produced
by Eastman’s four abrasive belt grits.
FINE BELT
FINE EDGE
Slices thru
synthetics and
blends, for knitted
or loosely woven
cloths, and for
silks, high-pile
fabrics, quilting,
etc.
BLUE
181C2-5
MEDIUM BELT
MEDIUM EDGE
Shears thru the
general run of
rayons, cottons,
light woolens,
tropicals, suitings,
and similar
materials
GREEN
181C2-2
COARSE BELT
COARSE EDGE
For heavier weight
variations of the
"medium" materials
at left, and for
lightly woven
cloths, pocketing,
light denims,
over-coatings,
light leatherette,
and rubberized
fabrics
RED
181C2-1
ROUGH BELT
ROUGH EDGE
The edge that
practically SAWS
thru heavy denim,
coated fabrics,
treated canvas,
simulated heavier
leathers, etc.
where the going
gets tough!
BLACK
181C2-6
SPECIAL PERFORMANCE BELTS: Electrostatically Coated
FINE BELT
MEDIUM BELT
COARSE BELT
BLUE
GREEN
RED
181C2-5SP
181C2-2SP
181C2-1SP
Figure 16. Edges Produced by Different Belt Grits
Available as an option on new machines or for retrofitting to
any existing Eastman straight knife, the Ergo-Handle al-
lows the operator to adjust the handle downward from the
standard horizontal through a 14-degree range. Adjusting
the handle’s angle to suit the operator’s preference allows
for more effective use of the arm muscles, while placing
less strain on the wrist and thumb.
PART NO.
DESCRIPTION
531C1-87
Regular Ergo-Handle
531C1-88
Cushion Ergo-Handle
Ergo-Handle
Figure 17. Ergo-Handle
18