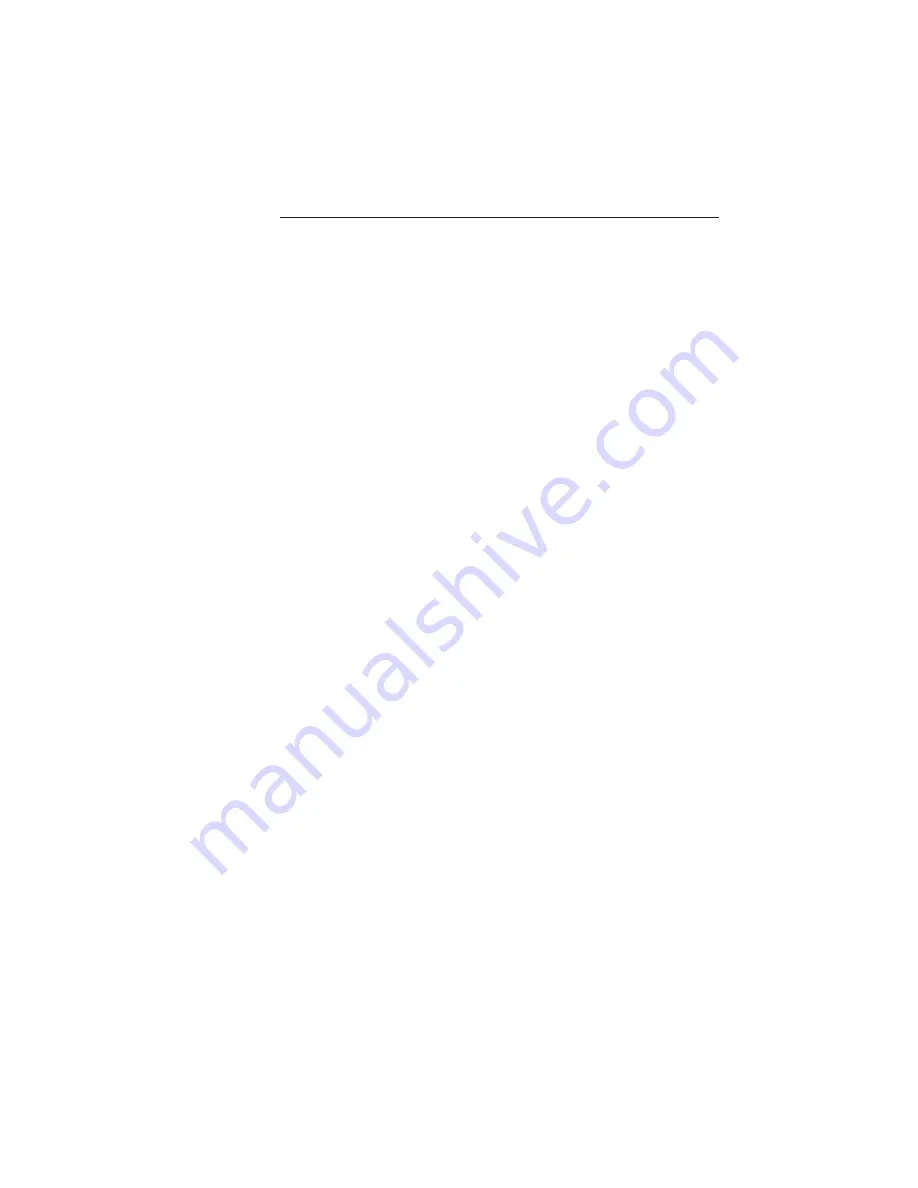
9
Warnings
Warning signs and labels shall be provided with enough light to be read, be conspicuously located, and maintained for
legibility. Do not remove any warning, caution, or instructional material attached.
TAKING CARE OF YOUR COMPRESSOR
ADDING OIL
A) Sightglass Type
Most Eagle compressors are equipped with a round or oval type sightglass oil level gauge. This sightglass gauge is located
on the crankcase opposite from the flywheel end of the compressor.
• Oil should always be visible in this sightglass, whether the compressor is operating or not.
• The top of the oil level sightglass indicates the maximum oil fill, the center indicates the normal operating level when
the compressor is at speed, and the bottom indicates the low oil operating level when the compressor is at speed. This
type of level 9 gauge allows you to check your oil level without having to stop the compressor.
• Always pull the motor disconnect switch to the Off position before adding oil to your compressor.
• Remove the oil fill plug and slowly add oil until a small air bubble is seen at the top of the sightglass.
CAUTION: Do not overfill; if in doubt remove the oil through the drain plug and slowly refill the
compressor.
• When the level has been reached, install the oil fill plug and re-start the compressor.
B) Dip Stick Type
• If your compressor is equipped with a dip stick type oil level gauge, stop and pull the motor disconnect each time you
check the oil level.
• The proper oil level is anywhere between the two marks. The top mark is the “full mark”, while the bottom mark is
the “add mark”.
• Never overfill your compressor.
Checking Belt Tension
ALWAYS TURN OFF AND LOCK OUT THE MAIN POWER DISCONNECT BEFORE WORKING ON THE BELTS
SO THE MOTOR CANNOT START UP UNEXPECTEDLY.
When belt tension is adjusted properly the belts can be depressed as follows:
• At a point midway between the motor pulley and the flywheel, apply 4 lbs. pressure to the outer surface of the belt
using a tensioning gauge and force the belt to deflect downwards:
The normal deflection is 3/8” to 1/2”.
• Loose belts will slip on the motor pulley and cause undue heat and wear. A loose belt will usually be hot and squeak.
• A belt that is too tight will overload the bearings and cause irreversible damage.
• Adjustments can be made by loosening the motor hold down bolts and sliding the motor along its base.
• When tightening the motor to its new location, always make sure that the two pulleys are perfectly aligned.
Installing New Belts
• When installing new belts, it is necessary that the motor bolts be loosened and the motor be moved towards the
compressor.
• The new belts can then be installed without damage or strain.
• As bolts will stretch, it is recommended that ALL belts be changed at the same time with matched belts.
• It is recommended that the belt tension be checked again after 8 hours and 40 hours of operation.
• Belt tension should be checked monthly, regardless of the amount of hours run.
Summary of Contents for RECIPROCATING
Page 2: ...2 ...
Page 15: ...15 TROUBLESHOOTING AND REPAIR ...
Page 16: ...16 TROUBLESHOOTING AND REPAIR ...
Page 17: ...17 TROUBLESHOOTING AND REPAIR ...
Page 19: ...19 ...