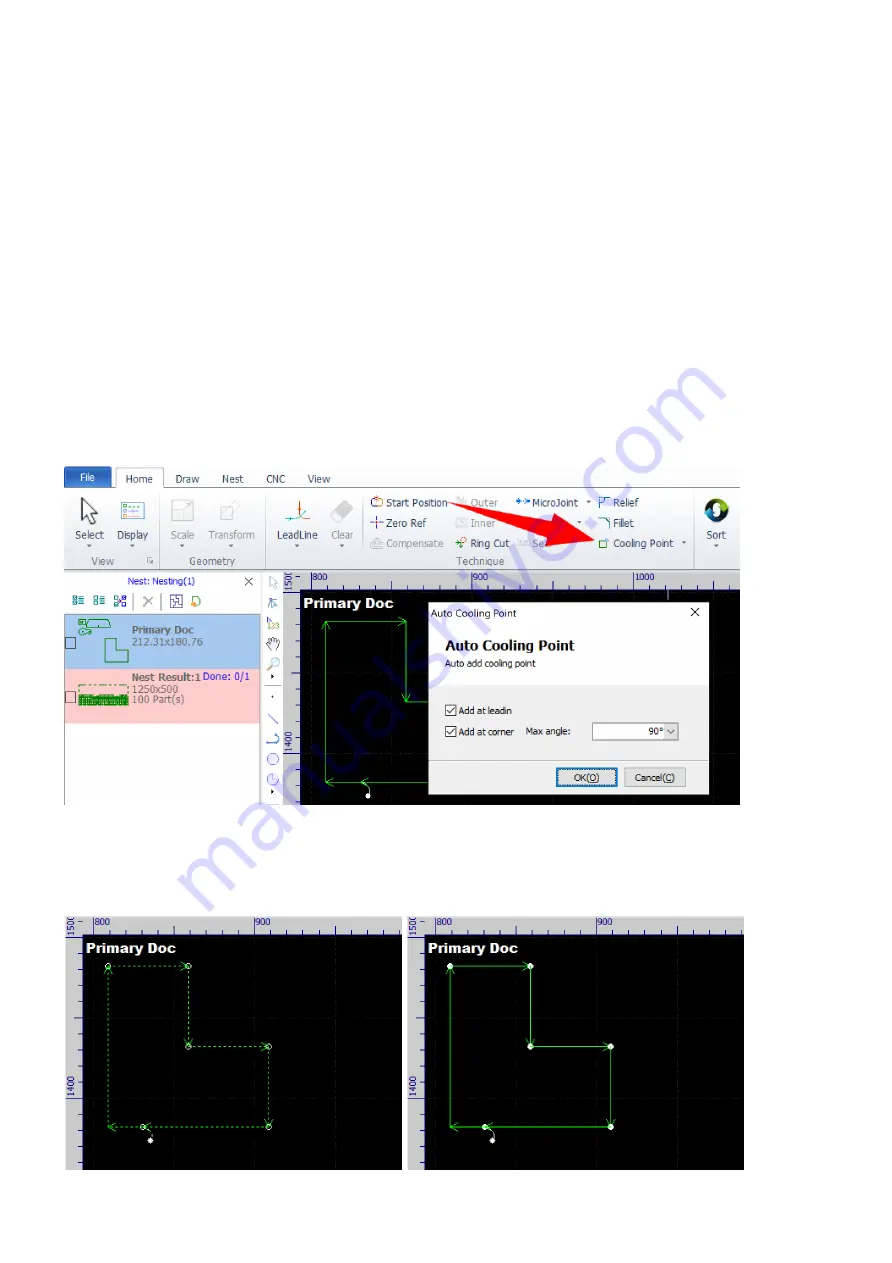
rev_0.6
100 / 135
Technologies for Getting Good Corners
In general, you would get bad quality when cutting sharp corners on thin materials in high speed, and on
thick materials in low speed, especially on mild steel with O
2
as the assist gas because too much heat
accumulated up there in a very small area which results in over burnt.
CypCut provides several functions to solve this problem from different points of view. If the geometry of a
corner has to be kept precisely, you can use the cooling point or the ring cut functions; otherwise, you can use
the fillet function, and incorporate the relief function if the part is prepared for bending.
Cooling Point
The cooling point function is to add stops in the cutting process and let the assist gas help cool the material
down a little more.
Select the contours and then select the command Auto Cooling Point in the pulldown-menu
Home>Cooling Point.
In the pop-up dialog, check the option Add at leadin if you want to set a cooling point at the start position,
check the option Add at corner if you want to set cooling points at sharp corners and set the angle range in
the option Max angle.
Cooling points appear as small circles when the contours are selected, and as solid ones when not.
Summary of Contents for EV-30
Page 41: ...rev_0 6 41 135 Machining Now you can start machining the parts...
Page 126: ...rev_0 6 126 135 3 Remove the access panel on top of the Z axis...
Page 127: ...rev_0 6 127 135 4 Remove the covers of the X axis drag chain...
Page 129: ...rev_0 6 129 135 7 Remove the corner access panel of the X Y intersection...
Page 133: ...rev_0 6 133 135 2 Remove the laser head from the Z axis slider...