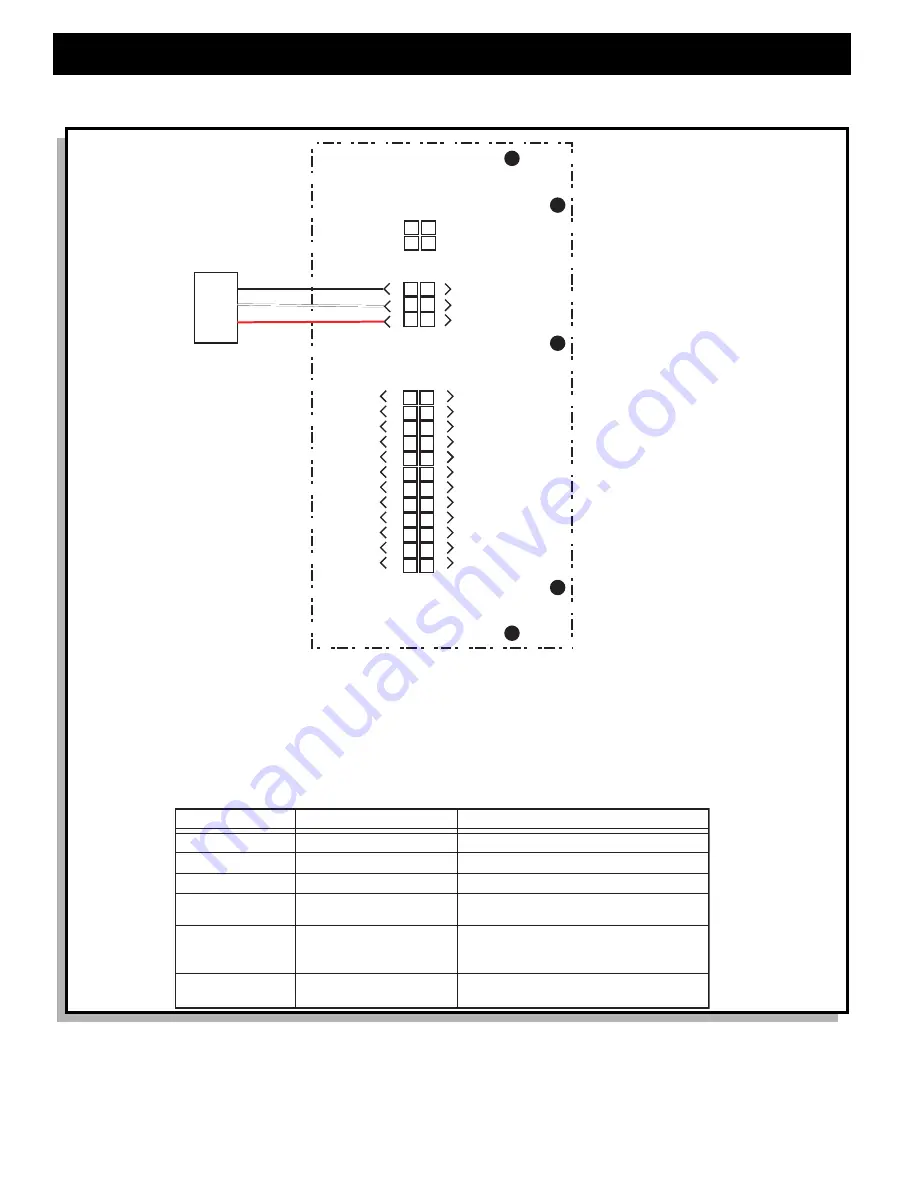
Page F-12
ELECTRONIC SPEED CONTROL
Repair and Service Manual
Read all of Section B and this section before attempting any procedure. Pay particular attention to all Notices, Cautions, Dangers and Warnings.
Fig. 13 J-2 Pin Connector Diagnostics
+
+
-
-
B
B
F2
M-
RED
Motor
Speed
Sensor
OUT
SPARE
SPARE
SPARE
WHT
F1
BLK
J3
J2
J1
1
2
3
1
2
3
4
5
6
4
5
6
7
8
9
10
11
12
13
14
15
16
17
18
19
20
21
22
23
24
All tests are to be performed with the negative lead of the DVOM connected to the negative side
of battery pack voltage.
The positive lead of the DVOM is used to probe the controller connections. Leave connections
plugged in the controller
Armature will need to be rotated for this test. Jack vehicle up on the passenger side and rotate
the rear wheel by hand
Pin number
Voltage
If not/ Then
J2-1
Spare
J2-2
Spare
J2-4
0 volts
Verify sensor harness and connection.
This connection serves as the sensor ground
J2-6
16 - 17 volts
Verify sensor harness. Possible faulty
controller
J2-3
Spare
J2-5
0 - 6.5 volts
Verify the speed sensor and harness . This
connection provides the flash voltage from
the sensor while the armature rotates.