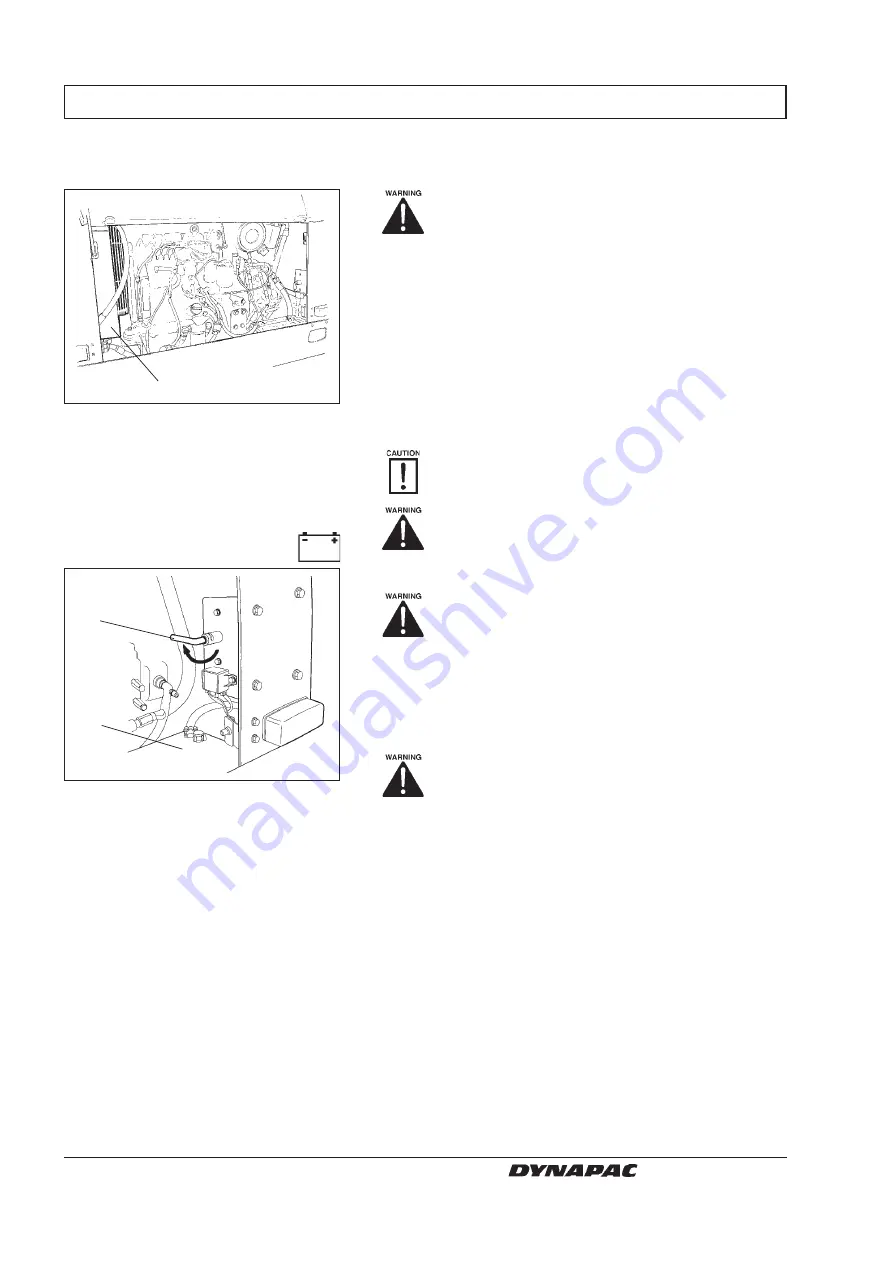
18
CP142 M142EN1
Hydraulic fluid cooler
Checking – Cleaning
Fig. 22 Engine compartment
1. Hydraulic fluid cooler
1
EVERY 250 HOURS OF OPERATION (Monthly)
Battery
– Check electrolyte level
Fig. 23 Battery
1. Master switch
2. Battery
1
2
Place the roller on a level base. The engine
must be switched off and the reserve/
parking brake knob pushed in for all check-
ing and adjustments on the roller unless
otherwise specified.
Check the radiator for leakage, damage or
accumulation of dirt.
Clean a dirty radiator using compressed air or a high-
pressure water jet.
Blow or wash the radiator in the opposite direction to
that of the cooling air.
Take care when using a high-pressure water
jet; do not hold the nozzle too near the cooler.
Wear protective goggles when working
with compressed air or with high pressure
washing.
Make sure there are no open flames in the
vicinity when checking the electrolyte
level. An explosive gas is formed in the
battery during the charging process.
Open the engine cover at the far rear of the machine.
Wipe the top of the battery (2).
Use protective goggles. The battery con-
tains corrosive acid. In the event of con-
tact, rinse with water.
Summary of Contents for CP142
Page 2: ...19 ILF015WO1...
Page 29: ...19 ILF015WO1...