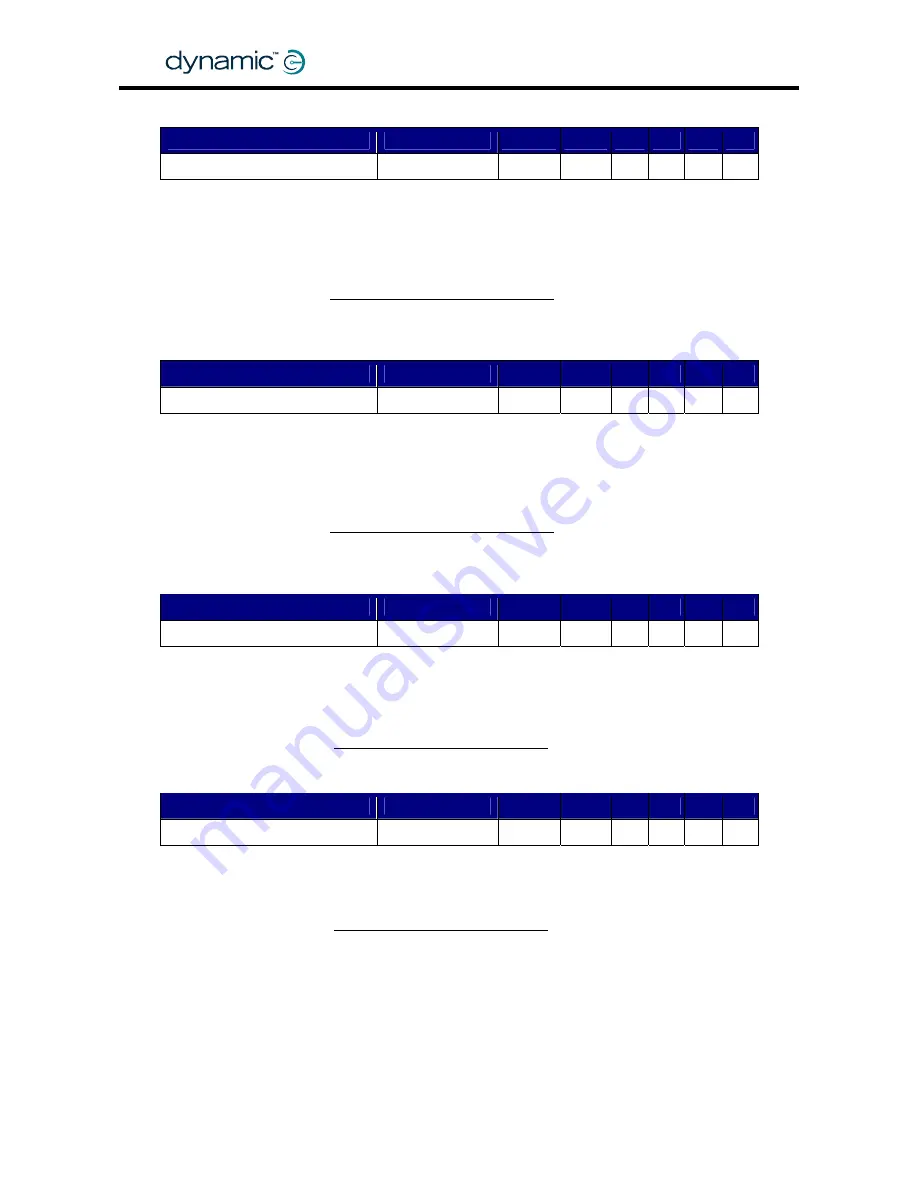
GBK60348
: Issue 1 – October 2007
68
5.3.7.9
Turning Speed @ Maximum
Parameter
Possible Values Default
Rev HHP Lite Std Adv
Turning Speed @ Maximum
20 – 100 %
N/A
-,A,C
Sets the turning speed of the powerchair when the joystick is fully deflected sideways
and the Speed Pot is in its Maximum position.
This parameter must be set for every Drive Profile.
See also section 5.3.2.3: Speed setting recommendations.
5.3.7.10
Turning Speed @ Minimum
Parameter
Possible Values Default
Rev HHP Lite Std Adv
Turning Speed @ Minimum
5 – 100 %
5%
C
Sets the turning speed of the powerchair when the joystick is fully deflected sideways
and the Speed Pot is in its Minimum position.
This parameter must be set for every Drive Profile.
See also section 5.3.2.3: Speed setting recommendations.
5.3.7.11
Turning Acceleration
Parameter
Possible Values Default
Rev HHP Lite Std Adv
Turning Acceleration
10 – 70 %
40 %
-,A,C
Sets the rate at which the turning speed increases after the joystick has been
deflected sideways. 10% results in a very slow increase, 70% results in a very quick
increase.
See also section 5.3.1.3 : Acceleration and deceleration.
5.3.7.12
Turning Deceleration
Parameter
Possible Values Default
Rev HHP Lite Std Adv
Turning Deceleration
15 – 100 %
70 %
-,A,C
Sets the rate at which the turning speed decreases after the joystick has been
returned to the centre. 15% results in a very slow stop, 100% results in an instant stop.
See also section 5.3.1.3 : Acceleration and deceleration.