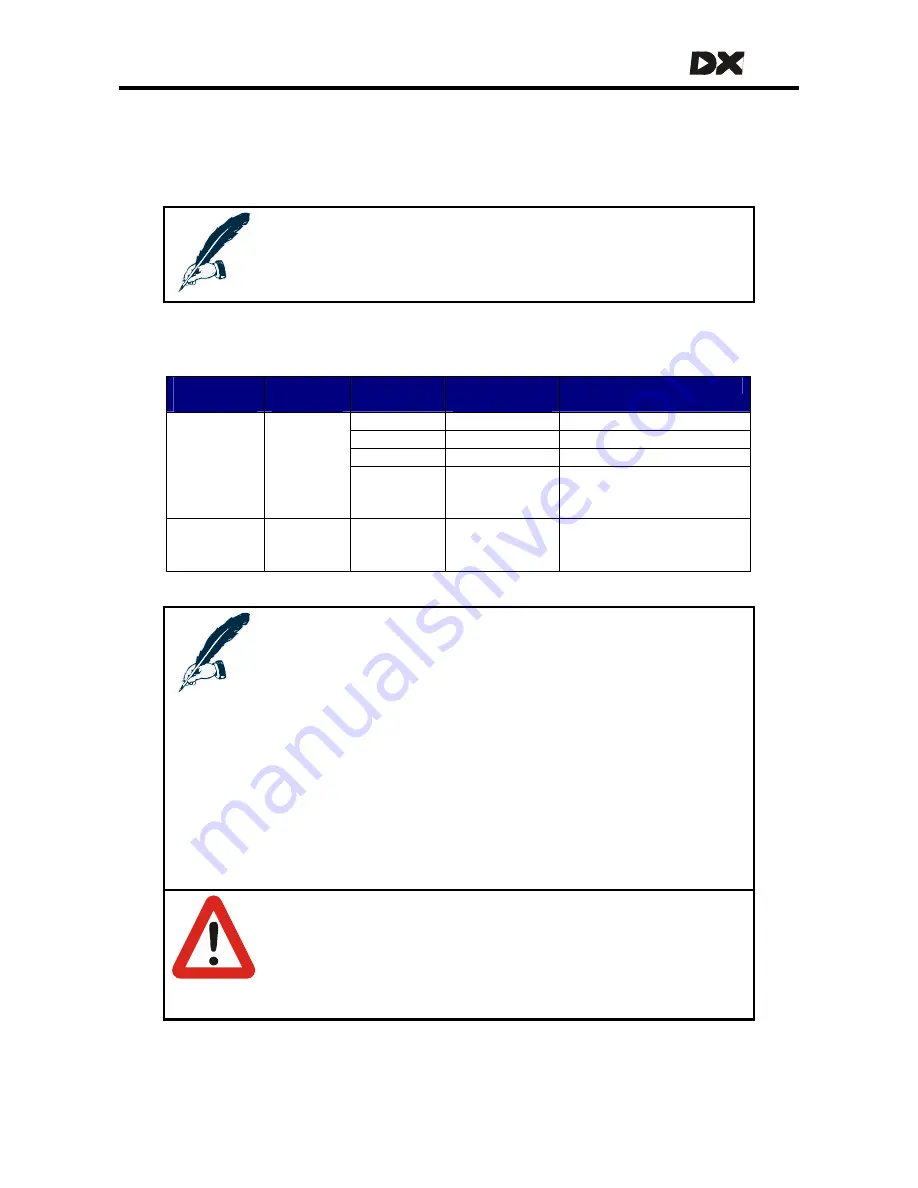
M
T
2.3
The motors
The wheel motors control the powerchair speed and direction. The motors are
connected to the DX Power Module.
Note:
If one of the motors is not connected to the DX Power Module, the
DX System detects a Motor Fault (see 9.6) and prevents driving.
2.3.1
Motor types
Drive motor
type
Motor
resistance
Current
Power
Module
Min. wire size
2 x 60A
DX-PMB
3 mm
2
2 x 75A
DX2-PMA75L
4 mm
2
2 x 80A
DX-PMB2
4 mm
2
24V DC*
0 – 0.5
Ω
1 x 120A
(2x 60A
parallel)
DX-PMB-S 3
mm
2
(two wires in parallel,
each carrying 60A)
24V AC
Gearless
Brushless
N/A
2 x 100A
DX-GB
6 mm
2
*12V DC motors can be used if the controller is programmed to half speed.
Notes:
1.
The motor wire sizes above are appropriate for motor loom
lengths up to 400 mm. For longer looms, increase the wire size
by 0.5 mm
2
for every additional 200 mm length. Generally, the
larger the wire size, the better the powerchair performance.
2.
The chosen size and length of the motor wires can affect the
optimum setting of the
Load Compensation
parameter (see
section 4.3.2.3).
3.
Gearless Brushless motors and the DX-GB Power Module are
not covered in this manual. Any reference to motors or motor
connectors in this manual is referring to DC motors and the
applicable Power Modules. Read the DX-GB manual for more
information about the Gearless Brushless system.
Warning:
The Power Module
must
be correctly configured for the
applicable motor resistance with the
Load Compensation
parameter, see section 4.3.2.3. Failure to set this parameter
correctly can be dangerous for the powerchair user, because
the chair can become uncontrollable.
17