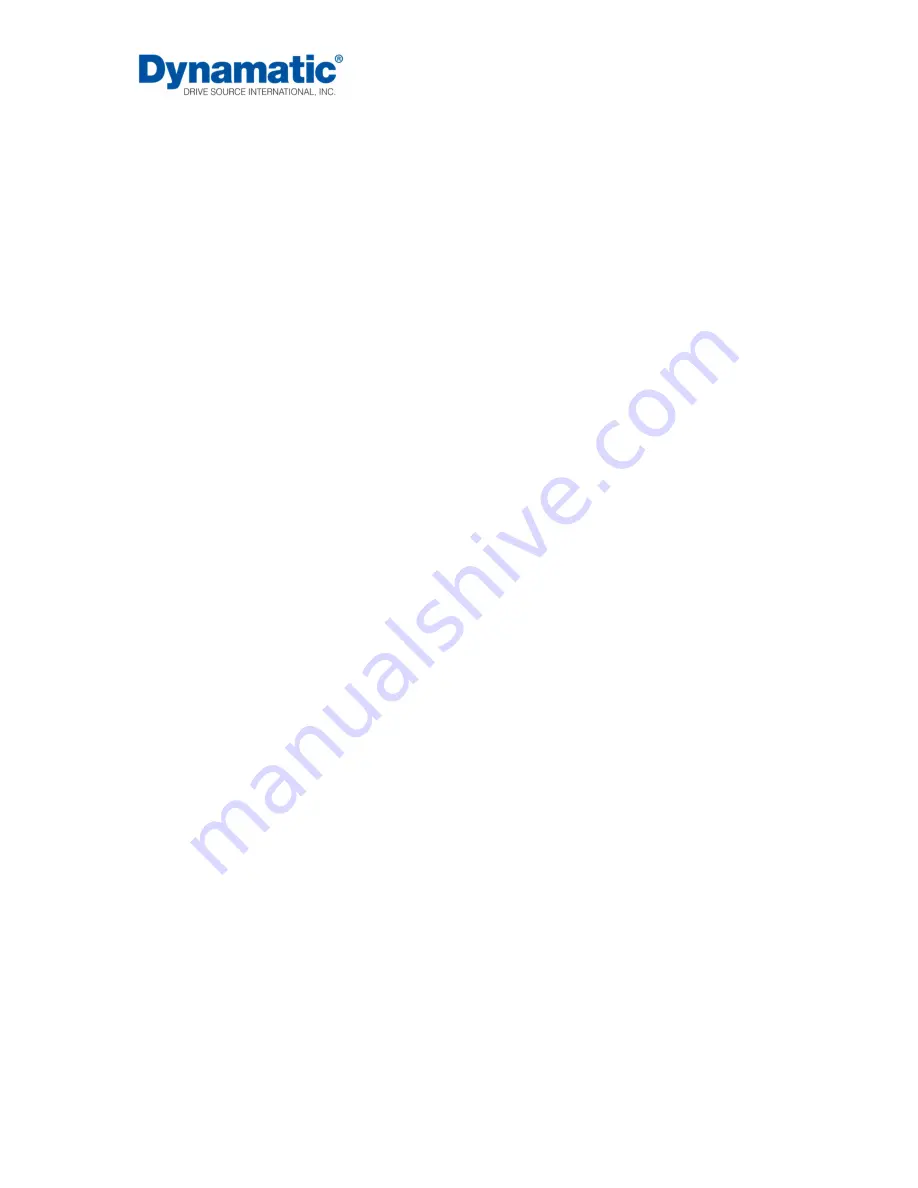
EC-2000-CES MANUAL
29
9.
BRAKE DEADBAND
Offset Between the actual set point and the beginning of clutch action for the PID loops.
Used to prevent oscillation between clutch and brake when running at steady speed
(Default = 50 RPM)
10.
BRK OFF DLY
This is a programmable delay from issuance of the stop command to release of the
clutch contactor by the control. Note that this timer is overridden by the contactor on
input from the press control.
Default = 0.50 Seconds
8.5
Menu F: PROCESS
The EC-2000-CES Control operates in strokes per minute. It uses RPM X gear ratio to establish a
operating speed in strokes per minute. All of the speeds set in process are multiplied by the
gear ratio to establish an operating speed. Note the control can also display an output speed is
strokes per minute from the resolver. This can be used to correct the gear ratio if the proper
value is not known to obtain the proper output speed. Max RPM / Gear Ratio = Max SPM
1.
INCH SPEED 0 to Max SPM
2.
MICRO INCH SPEED 0 to Max SPM
3.
ANGLE #1
The control has six programmable angle and speeds. For example, when the control
sees Angle #1 as the last position it has passed, it will run at Speed #1
Range: 0 to 360 Degree (Note 360 DEG is ignored)
4.
SPEED #1
Programmed Speed for Angle #1
0 to Max SPM
5.
ANGLE #2
Angle and Speed #2 thru 6 work the same as Angle #1 and Speed #1
6.
SPEED #2
7.
ANGLE #3
8.
SPEED #3
9.
ANGLE #4
10.
SPEED #4
11.
ANGLE #5
12.
SPEED #5
Summary of Contents for 015-000248-2002
Page 7: ...EC 2000 CES MANUAL 7 Figure 1 Eddy Current Drive Block Diagram ...
Page 8: ...EC 2000 CES MANUAL 8 Figure 2 EC 2000 CES Keypad Display ...
Page 12: ...EC 2000 CES MANUAL 12 ...
Page 16: ...EC 2000 CES MANUAL 16 Figure 4 Keypad Cutout Template to Scale Inches ...
Page 17: ...EC 2000 CES MANUAL 17 Figure 5 Keypad Dimensions to Scale ...