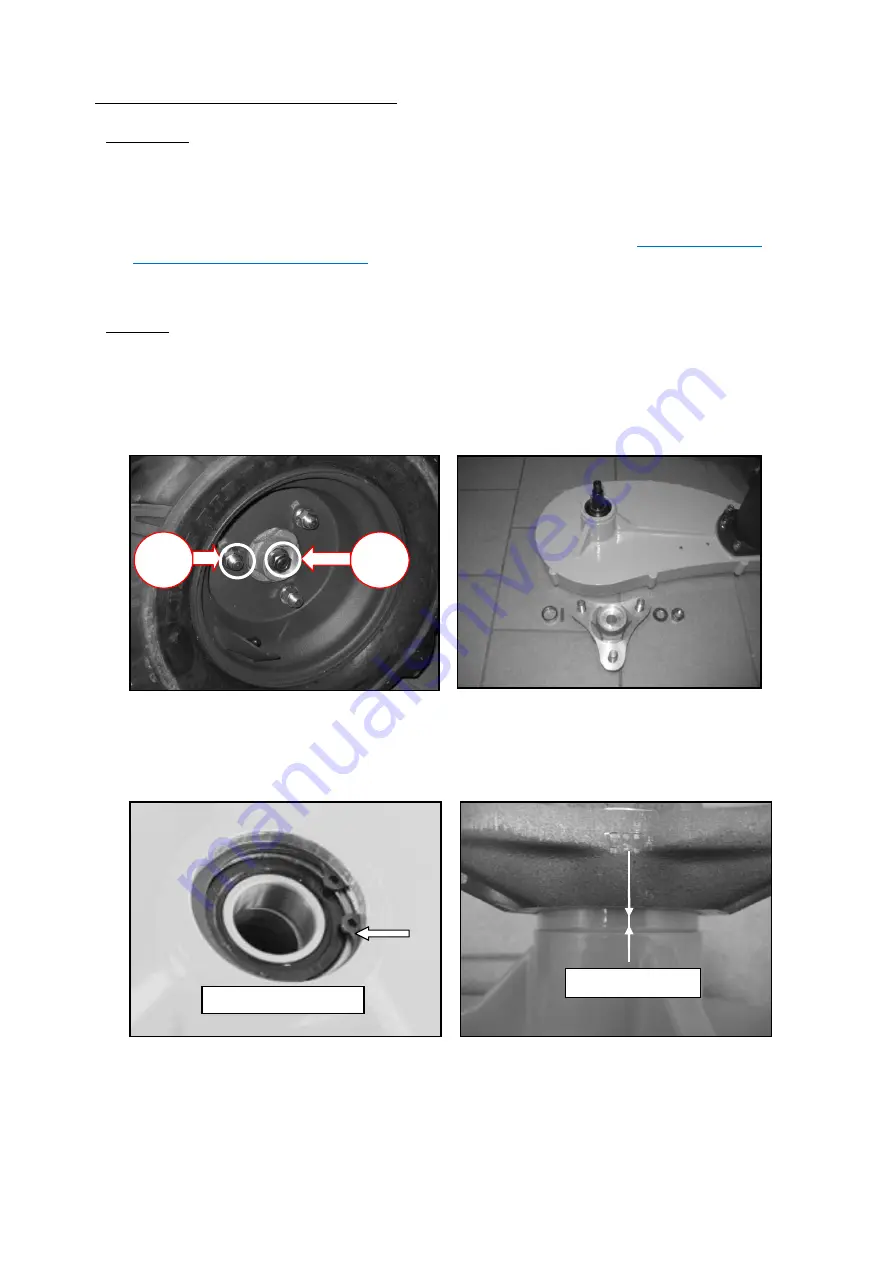
49
/
84
SM-SG-2 Ev3/25062014
6.19 REPLACEMENT OF THE WHEEL SHAFT
Dismounting:
-
Remove the wheel (3 bolts holding the wheel)
-
Undy the main wheel nut (Fig. 99)
-
Remove the wheel hub (use wheel hub puller, if necessary heat up the hub for easier dismounting ), spacing
ring and key
-
Clean the wheel shaft (it must be able to slide through the bearings)
-
Remove the wheel suspension housing cover, tensioning segment and the chain see
6.18 Adjustment and
replacement of the wheel driving chain
-
Pull the wheel shaft with the chain sprocket out of the bearings
-
If the bearings need to be replaced, remove the securing ring of the bearings and press the bearings out.
Mounting: (take the above steps in reverse order)
-
Lubricate the shaft with grease
-
Degrease the taper seating of the wheel shaft and the wheel hub
-
Install a new spacing ring, key, wheel hub and washer
-
Ensure a good seating of the wheel hub onto the taper of the wheel shaft
-
Secure the main wheel nut with LOCTITE 243 and torque to 115 Nm (Fig. 99)
Fig. 99
Fig.100
Fig. 101
Fig. 102
Clearance 1-2 mm
Securing the bearings
1
-2
m
m
115
Nm
60
Nm
Summary of Contents for ILD02 SG
Page 1: ...SM SG 2 Ev3 25062014 SERVICE MANUAL SPIDER ILD02 SG...
Page 7: ...7 84 SM SG 2 Ev3 25062014 Ampere meter CEM DT 9701 Voltmeter Ben electronic DT 830 D...
Page 23: ...23 84 SM SG 2 Ev3 25062014 Fig 35 60Nm 70Nm...
Page 33: ...33 84 SM SG 2 Ev3 25062014 Fig 59 Fig 60 Fig 61 Loctite the pulley bolt 50Nm...
Page 81: ...81 83 SM SG 2 Ev3 25062014 7 19 NBB ELECTRIC DIAGRAM ILD02 SG...
Page 82: ...82 83 SM SG 2 Ev3 25062014 7 20 ELEVATION AND SKID STEERING MODULE NBB ILD02...