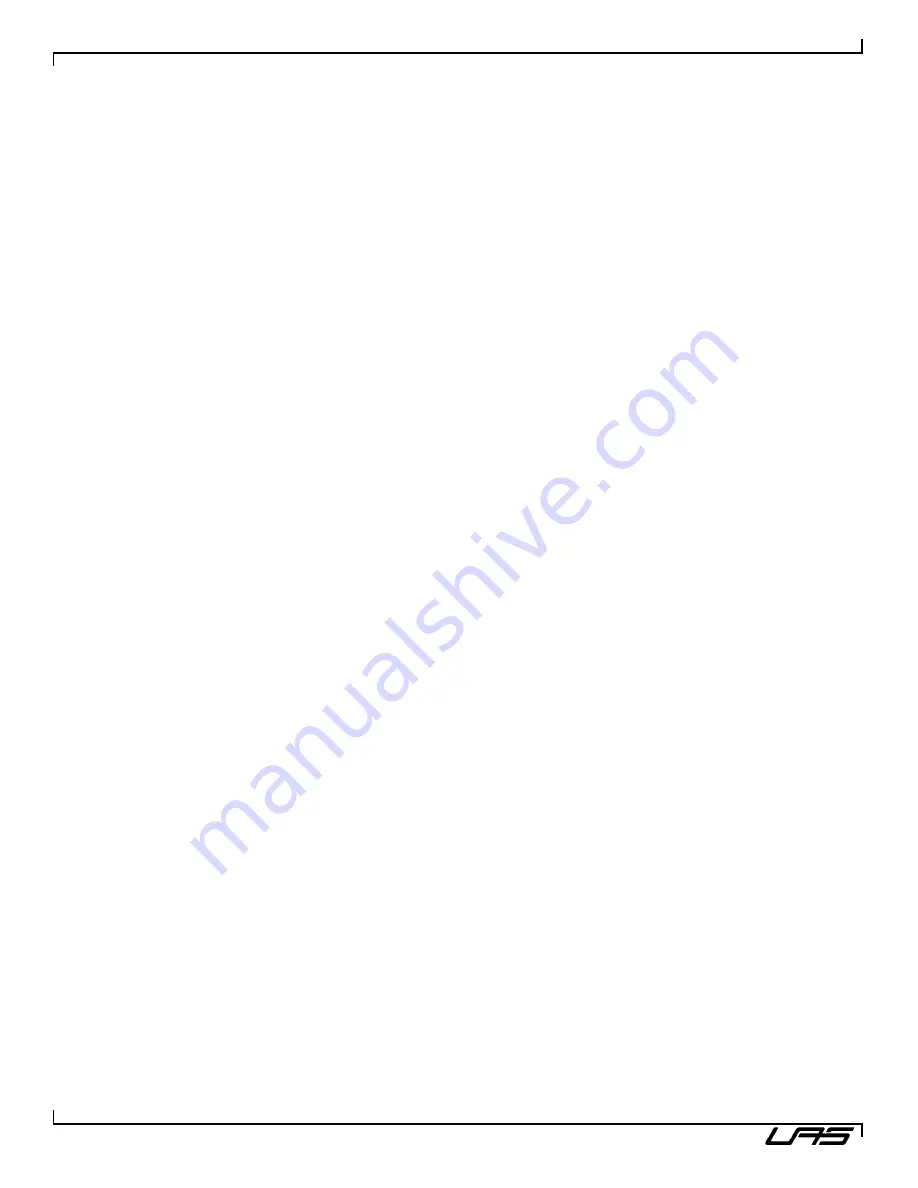
17
United Air Specialists, Inc.
Revised 9/02
Porta-Hog
®
Supra-Conic
®
Cartridge Dust Collector
6. The second pulse cleaning operation is now
energized. The diaphragm valve(s) will activate for 1
second (“pulse” LED will illuminate during pulse
discharge operation). The second pulse multi-cycle
downtime cleaning operation is now complete. The
“system” LED will now stop flashing and de-energize,
indicating cleaning system is complete.
For the third pulse multi-cycle downtime cleaning
configuration, the controller card will initiate a 210
second time delay to allow the air manifold reservoir
to recharge from the plant compressed air system.
7. The third pulse cleaning operation is now energized.
The diaphragm valve(s) will activate for 1 second
(“pulse” LED will illuminate during pulse discharge
operation). The third pulse multi-cycle downtime
cleaning operation is now complete. The “system”
LED will now stop flashing and de-energize, indicating
cleaning system is complete.
CARTRIDGE FILTERS
On certain applications, it may be beneficial to “seed” or
pre-coat the original or replacement cartridge filter(s).
Seeding is the process of introducing a light
concentration of coating particulate (usually crushed
limestone, agricultural lime or other specifically marketed
filter pre-coat) to the filter media. Seeding deposits a
thin coating to the media, also known as a “dust cake,”
which acts as an aid to filtration. The deposited
dustcake keeps the dust from loading on the surface of
the cartridge filter. This increases filter life and efficiency
while allowing the cleaning system to operate more
effectively. For filter seeding procedures, refer to Section
6.2.
COMPRESSED AIR SUPPLY
For dust collectors supplied without an air compressor,
verify the existing plant compressed air supply to dust
collector is clean, dry and oil-free. The dust collector
requires 93-100 PSIG (6.4-6.9 BAR) of compressed air
at the dust collector air manifold reservoir.
For dirty, dusty environments, UAS recommends the use
of a customer-supplied compressed air system.
If optional pneumatic valve assembly (as sold by UAS) is
installed, verify pressure regulator valve is adjusted until
gauge reads 93-100 PSIG (6.4-6.9 BAR).
DUST STORAGE CONTAINER
Make certain the dust drawer is in place. For units with a
hopper assembly, make certain all connections are
airtight and the dust drum or pail is in place. If the dust
collector has a slide gate, make certain it is open.
MAGNEHELIC
®
GAGE KIT
If the dust collector has been ordered with a field-
installed Magnehelic Gage (shipped loose Magnehelic
Gage Kit to be customer installed), follow the field
installation instructions found in Section 7.2.
COMPRESSED INLET AIR FILTER
The air compressor is equipped with a small round black
filter assembly which is used to filter the compressor inlet
air. This air filter should be changed when filter media
(foam pad/cloth) becomes dirty. Open filter and check
foam pad/cloth for dirt build-up. Replace filter every
three months of duty (200 hours) or as needed.
5.2 CHECK LIST
COVER PANEL
Verify the exhaust air cover panel of the Supra-Conic
®
dust collector is clear and free of obstruction. Initially
some dust may discharge from the dust collector as the
filter(s) is seasoned. This may last several minutes, after
which the discharge air should remain visibly clean.
AIRFLOW AND STATIC PRESSURE
Measure the total airflow and static pressure at the
inlet(s) of the Supra-Conic
®
dust collector. Adjust the
ductwork design conditions or optional volume control
damper to achieve desired system airflow.
Check to ensure that adequate air is being drawn into
each of the collection points of the system. Adjust
individual dampers for each operation to balance the
system airflow. Recheck the total system airflow and
adjust ductwork design or optional volume control
damper for desired design airflow. This procedure may
need to be repeated several times until entire system is
within airflow design specifications.
FILTER CLEANING SYSTEM
Check the filter cleaning system for proper operation.
The built-in air compressor should pressurize the air
manifold reservoir to 93 PSIG (6.5 BAR) before triggering
the pressure switch. Follow adjustment instructions
printed on the pressure switch enclosure (inner surface)
to allow the pressure switch to open at 93 PSIG (6.5
BAR) +
_ 2 PSIG (0.1 BAR). Connect the temporary
pressure gauge to the pressure switch unloader line tube
(1/4" tube fitting) to set pressure switch range (refer to
Figure 8). Reassemble the pressure switch unloader
assembly.
Summary of Contents for SUPRA-CONIC
Page 1: ...SUPRA CONIC Cartridge Dust Collector Installation and Operation Manual ...
Page 8: ...Revised 9 02 Porta Hog Supra Conic Cartridge Dust Collector 3 United Air Specialists Inc ...
Page 9: ...Revised 9 02 Porta Hog Supra Conic Cartridge Dust Collector 4 United Air Specialists Inc ...
Page 14: ...9 United Air Specialists Inc Revised 9 02 Porta Hog Supra Conic Cartridge Dust Collector ...
Page 15: ...10 United Air Specialists Inc Revised 9 02 Porta Hog Supra Conic Cartridge Dust Collector ...
Page 16: ...11 United Air Specialists Inc Revised 9 02 Porta Hog Supra Conic Cartridge Dust Collector ...
Page 17: ...12 United Air Specialists Inc Revised 9 02 Porta Hog Supra Conic Cartridge Dust Collector ...
Page 19: ...14 United Air Specialists Inc Revised 9 02 Porta Hog Supra Conic Cartridge Dust Collector ...
Page 27: ...22 United Air Specialists Inc Revised 9 02 Porta Hog Supra Conic Cartridge Dust Collector ...
Page 28: ...23 United Air Specialists Inc Revised 9 02 Porta Hog Supra Conic Cartridge Dust Collector ...
Page 29: ...24 United Air Specialists Inc Revised 9 02 Porta Hog Supra Conic Cartridge Dust Collector ...
Page 30: ...25 United Air Specialists Inc Revised 9 02 Porta Hog Supra Conic Cartridge Dust Collector ...
Page 31: ...26 United Air Specialists Inc Revised 9 02 Porta Hog Supra Conic Cartridge Dust Collector ...
Page 32: ...27 United Air Specialists Inc Revised 9 02 Porta Hog Supra Conic Cartridge Dust Collector ...
Page 33: ...28 United Air Specialists Inc Revised 9 02 Porta Hog Supra Conic Cartridge Dust Collector ...