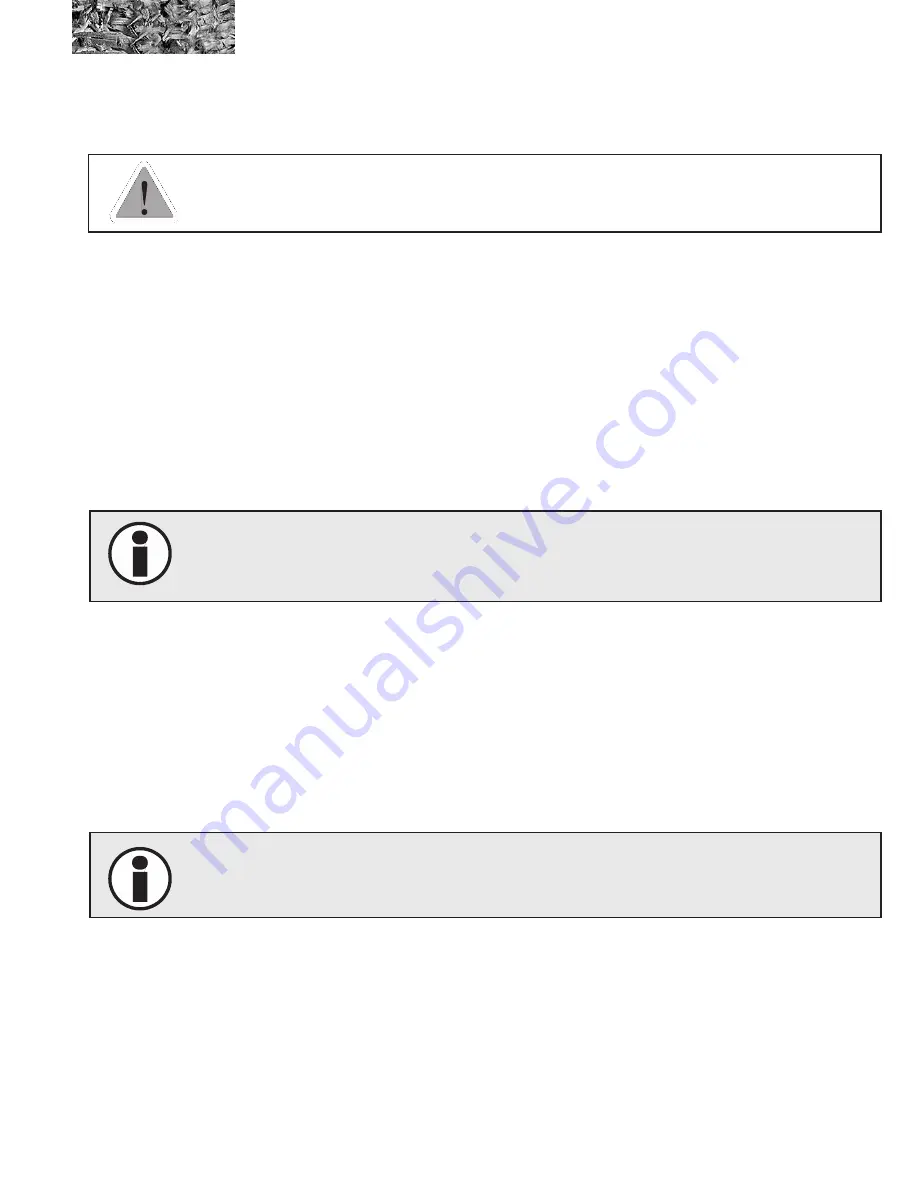
27
T C - 1 2 T R E E C H I P P E R
O P E R A T I N G I N S T R U C T I O N S
Section 5: General Maintenance
Warning:
Before servicing the TC-12 TREE CHIPPER, read the Service and Maintenance section of
the Safety Instructions.
5.1 Welding Procedure
Welding on a machine that is equipped with an Electronic Engine.
Proper welding procedures are necessary in order to avoid damage to the computerized equipment. Computerized
equipment includes but not limited to the following; the Engine Control Unit (ECU), HPTO Control Module and au
-
tofeed controller.
If at all possible, the component that is to be welded should be removed from the machine for welding. If removal of
the component is not possible, the following procedure must be followed when welding on a machine that is equipped
with electronic engine. This procedure is considered and safest and should provide minimum risk of electronic compo
-
nent damage.
Note:
Do not ground the welder to electrical components such as the ECU or sensors. Improper
grounding can also damage the drive train bearings or hydraulic components. Clamp the ground
cable from the welder to the component that will be welded. Place the clamp as close as possible to
the weld. This will help reduce the possibility of damage.
1. Stop the engine. Turn the battery disconnect switch to the OFF position.
2. Disconnect the negative battery cable from the battery.
3. Disconnect the connectors from the computerized equipment listed on the pervious page. Move each har
-
ness to a position that will not allow the harness to accidentally move back and make contact with any of
the connector pins.
4. Connect the welding ground cable directly to the part that will be welded. Place the ground cable as close
as possible to the weld in order to reduce the possibility of welding current damage to the bearings, hy-
draulic components, electrical components, and ground straps.
Note:
If the electrical/electronic components are used as a ground for the welder, or electrical/elec
-
tronic components are located between the welder ground and the weld, current flow from the welder
could damage the components.
5. Protect the wiring harness and hydraulic hoses from welding debris and spatter.
6. Use standard techniques to weld the materials.
Summary of Contents for TC-12
Page 2: ...Clearing the Way for a Better Tomorrow...
Page 4: ...Clearing the Way for a Better Tomorrow...
Page 51: ...41 T C 1 2 T R E E C H I P P E R O P E R A T I N G I N S T R U C T I O N S...
Page 52: ...42 T C 1 2 T R E E C H I P P E R O P E R A T I N G I N S T R U C T I O N S...
Page 68: ...58 T C 1 2 T r e e C h i p p e r P A R T S R E F E R E N C E D I S C A S S E M B L Y...
Page 150: ...140 T C 1 2 T r e e C h i p p e r P A R T S R E F E R E N C E D E C A L L O C A T I O N S...
Page 151: ...141 T C 1 2 T r e e C h i p p e r P A R T S R E F E R E N C E D E C A L L O C A T I O N S...