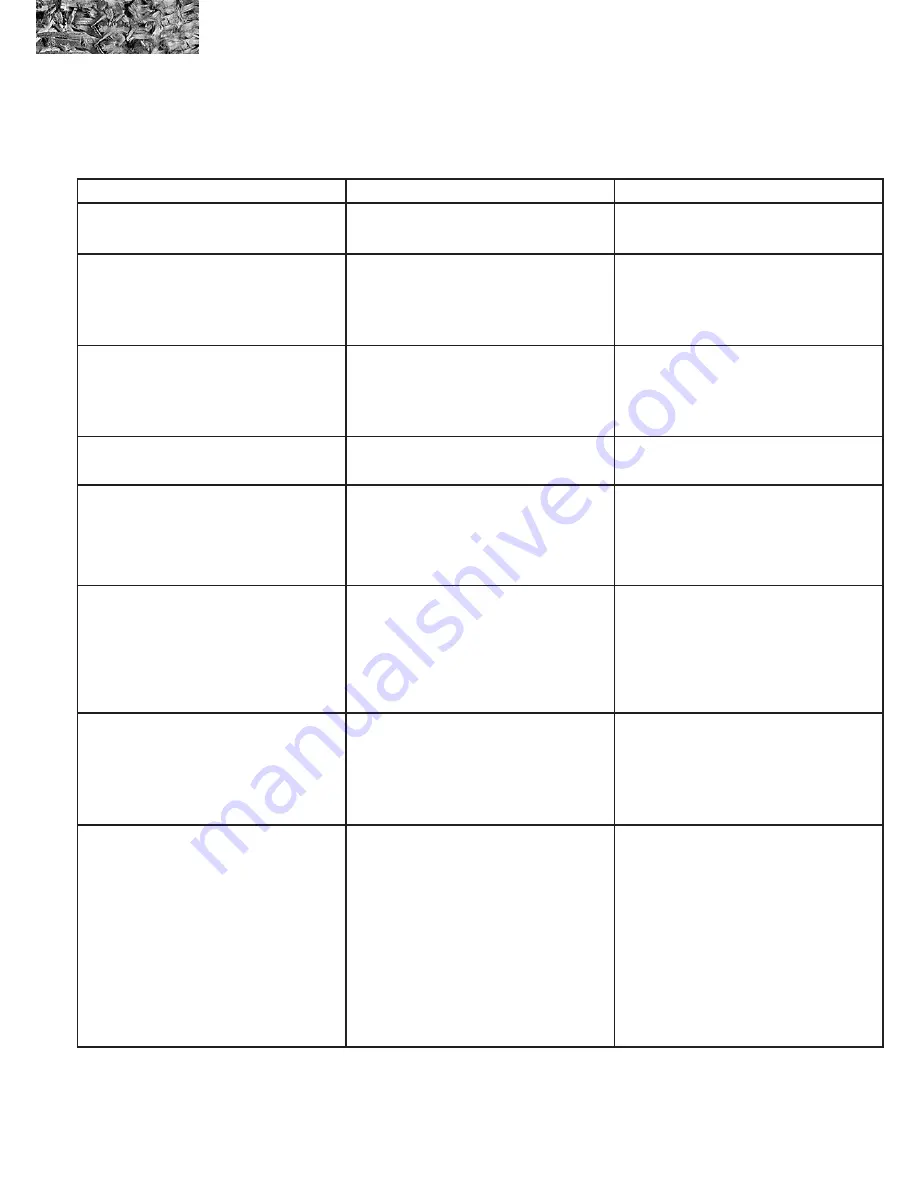
38
T C - 1 2 T R E E C H I P P E R
O P E R A T I N G I N S T R U C T I O N S
Section 6: Troubleshooting the TC-12
6.1 General trouble shooting
Problem
Possible cause
Solution
Chipper disc will not turn.
1. Obstruction in chipper housing
1. Check chipper housing and clean out
2. Check for seized chipper bearings
2. Lubricate or replace
Chipper disc wobbles.
1. Disc hub loose
1. Re-torque to 1620 in-lbs
2. Bearing loose
2. Re-torque to 270 ft-lbs
3. Chipper bearings worn
3. Replace
4. Knife pocket or paddle is plugged with material
4. Unplug pockets
Chipper bearings running too hot.
1. Improper lubrication
1. Purge bearings once a day with lithium grease
2. Belt too tight
2. Set belt tension with tension gauge
3. Bearing lock collar may be loose
3. Tighten bearing lock collar set screws
4. Bearings worn out
4. Replace
Discharge plugs or does not throw chips properly.
1. Knives are dull or worn
1. Sharpen knives or replace with new ones
2. Obstruction in discharge chute
2. Remove access cover on chute to remove obstruction
Chipper knife hits anvil
1. Anvil not set properly
1. Follow anvil adjustment procedure.
2. Shaft misaligned
2. Disc should have same clearance side to side. Adjust
pillow block bearing.
3. Disc is not properly set on shaft.
3. Disc should have min. 11/16” clearance to housing on
feed side. Slide disc on shaft
Chipper makes poor quality chips or does not feed
properly.
1. Knives lost their edge
1. File, grind or replace knives
2. Knife anvil worn or need adjustment.
2. Rotate, repair or replace
3. Knives are at wrong angle
3. Use DuraTech knives and sharpen to 30 degree angle
4. Not sufficient feedwheel down pressure
4. Increase spring tension
5. Material being chipped is small, dry or rotting
5. Type of material does not produce good quality chips
Feedwheel slow or stops when feeding.
1. Dull knives
1. Replace knives/Resharpen
2. Relief valve is worn or dirty
2. Clean, rest or replace
3. Pump is worn
3. Replace
4. Motors are worn
4. Replace
5. Feedwheel springs to tight
5. Adjust
Feedwheel turns slowly or not at all.
1. Relief valve stuck open
1. Clean or replace
2. Worn hydraulic motor
2. Replace
3. Pump worn
3. Replace
4. Pinched hydraulic or damaged hydraulic hose
4. Replace
5. Feedwheel valve worn and leaking internally
5. Replace
6. Low hydraulic oil level
6. Fill 7/8 full minimum
7. Plugged oil screen
7. Replace
8. binding such as worn bearing, etc,
8. Repair
9. Hydraulic oil is cold
9. Should warm up while running
10. Speed sensor is out of adjustment/not working or
program set points are wrong
10. Turn senor in until it contacts side of flywheel and turn
out one turn.
Summary of Contents for TC-12
Page 2: ...Clearing the Way for a Better Tomorrow...
Page 4: ...Clearing the Way for a Better Tomorrow...
Page 51: ...41 T C 1 2 T R E E C H I P P E R O P E R A T I N G I N S T R U C T I O N S...
Page 52: ...42 T C 1 2 T R E E C H I P P E R O P E R A T I N G I N S T R U C T I O N S...
Page 68: ...58 T C 1 2 T r e e C h i p p e r P A R T S R E F E R E N C E D I S C A S S E M B L Y...
Page 150: ...140 T C 1 2 T r e e C h i p p e r P A R T S R E F E R E N C E D E C A L L O C A T I O N S...
Page 151: ...141 T C 1 2 T r e e C h i p p e r P A R T S R E F E R E N C E D E C A L L O C A T I O N S...