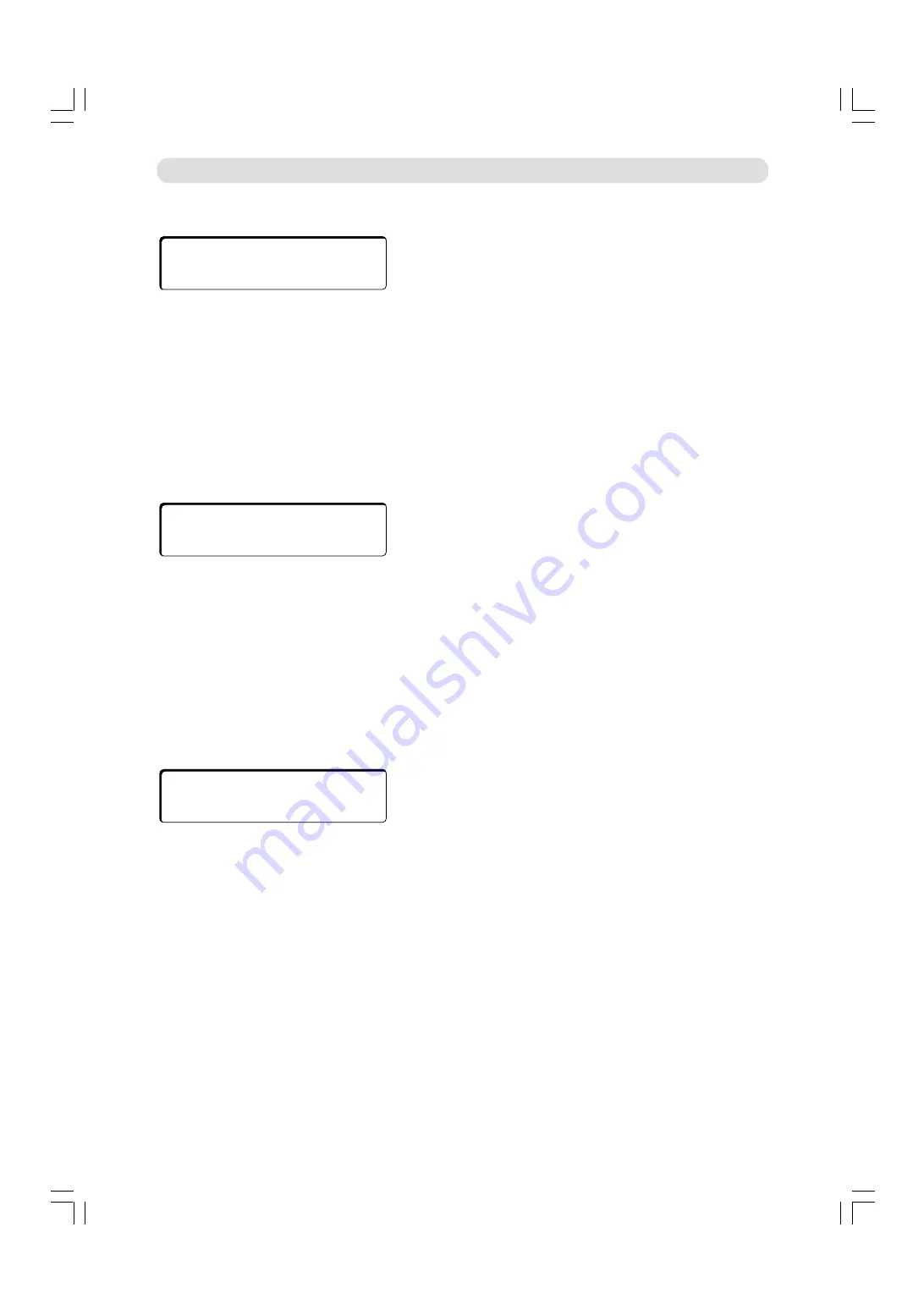
34
––– J 7 –––
CUTTER LOCK
Cause
•
Paper does not meet specifications
•
Cutter motor is defective
•
Cutter position switch is defective
•
Main PWB unit is defective
Problem detected
1. There was no response from the cutter position switch even though the specified time (0.6 seconds) elapsed after
cutting started.
––– J 8 –––
CREASE LOCK
Cause
•
Paper does not meet specifications
•
Creaser motor is defective
•
Creaser sensor is defective
•
Main PWB unit is defective
Problem detected
1. There was no response from the creaser sensor even though the specified time (2.0 seconds) elapsed after scoring
started.
––– E 1 –––
COVER OPEN
Cause
•
Actuator (N4-L224*&N4-225*) installation is incorrect
•
Interlock is defective
•
Main PWB unit is defective
Problem detected
1. One of the covers was open while the machine was operating.
2. One of the covers was open when the start button was pushed.
Error Messages
Docu Cutter(HCEX) 4_30-52
03.12.8, 3:10 PM
34