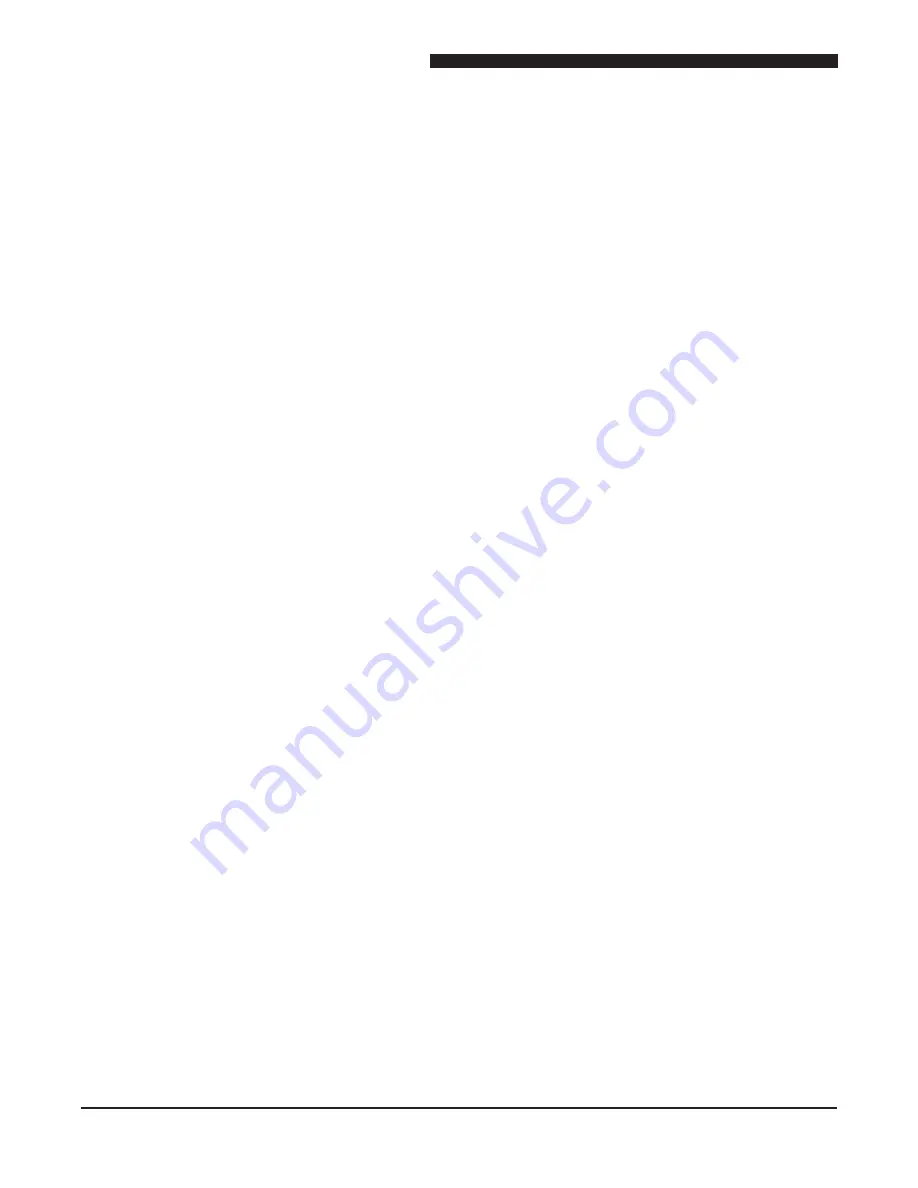
Service Manual for Subway Front Counters
14
Recharging Refrigeration System – Duke
Service Bulleting Number 26
General
To analyze the performance of a refrigeration
system, temperature readings are recorded and
converted to pressure readings using a standard
pressure/temperature chart.
When it is necessary to service a factory sealed
refrigeration system and return it to its properly
sealed condition, strictly adhere to the following
approved procedure.
Tools
Standard hand and refrigeration tools
Refrigerant Type: R-404A
Charging Procedure
NOTE:
Prior to refrigeration system service,
special care must be taken during the evacuation
process to remove air, moisture and other
non-condensables from the system. Duke
Manufacturing recommends the following
triple evacuation method. Failure to follow this
procedure may result in poor refrigeration system
performance.
1. Evacuate system to 1500 microns
2. Break vacuum to 2 psig with dry nitrogen. If
dry nitrogen is unavailable, use same type of
refrigerant as used in system.
3. Evacuate system to 1500 microns.
4. Break vacuum to 2 psig with dry nitrogen. If
dry nitrogen is unavailable, use same type of
refrigerant as used in system.
5. Evacuate system to 500 microns.
The system is now ready to receive refrigerant
charge according to information on data plate.
CAUTION: Never use oxygen or acetylene
in place of dry nitrogen or
refrigerant for leak testing. A
violent explosion may result
causing property damage,
personal injury or death. When
using nitrogen to pressure test,
always use a pressure regulator.
Failure to do so will result in
extremely high pressure of the
compressor or other system
components and result in
property damage, personal injury
or death.
NOTICE:
Prior to repair, ensure there is enough
process hose (approximately 12”) present to
complete the repair using the above procedure.
If not, install a new process hose before repair
sequence.
1. Install a temporary access valve on the high
and low side of process hoses as close to
factory crimps as possible.
2. Use temporary valves to perform repair. Duke
Manufacturing will not reimburse the cost of
permanently installed valves.
3. After completing repair, evacuate system using
the triple evacuation method described in Duke
Manufacturing Service Bulletin Number 26.
4. After completing proper evacuation method,
recharge system, using proper refrigerant
according to information on data plate.
5. Continue crimping process hose just below
temporary valve and again 2” below crimp.
6. With crimp tool in place, remove temporary
valve.
7. Braze shut end of process hose.
8. Allow to cool for about 5 minutes.
9. Remove crimp tool.
10. Check brazed end for leaks.