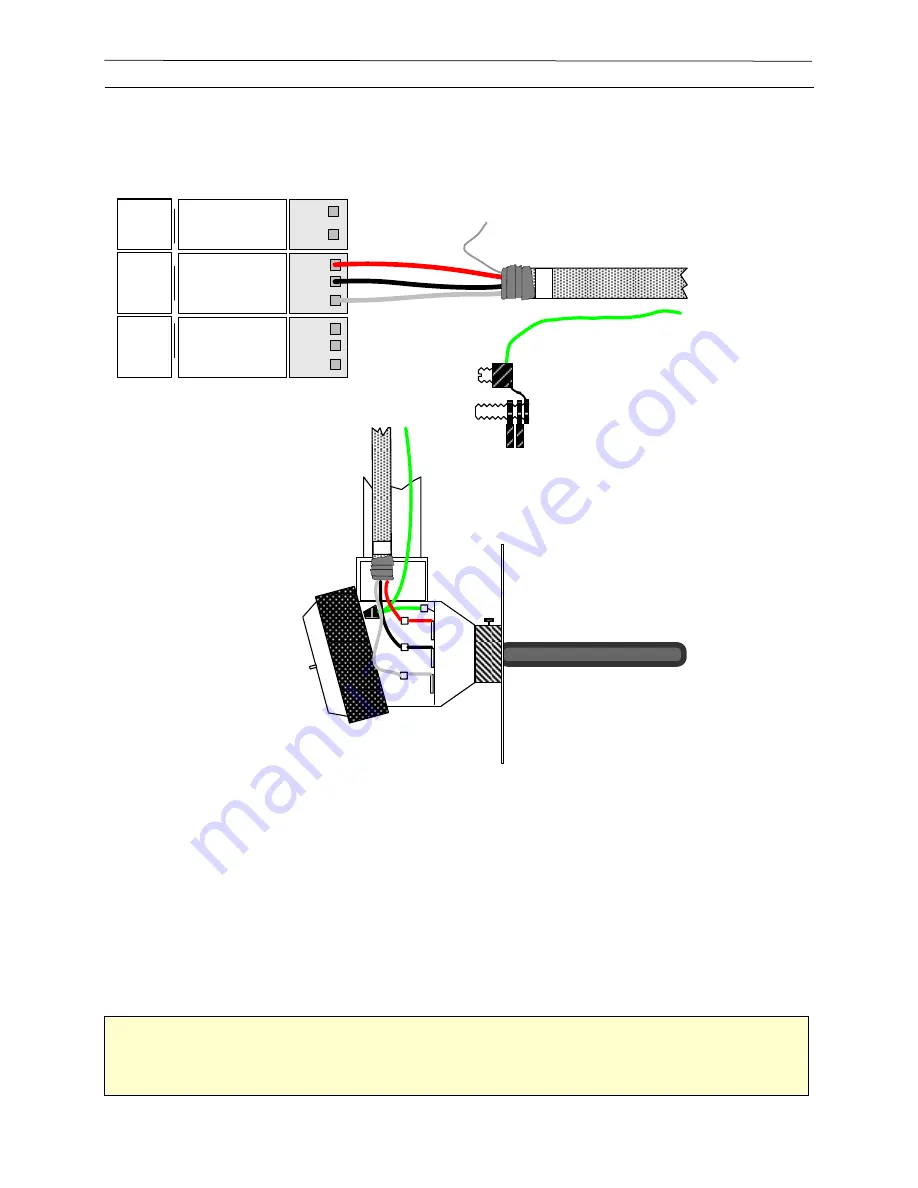
Page | 60
Dryer Master DM510
Installation Manual
Connecting to a Drying Air Temperature Sensor
GND
+24VDC
Temp
GND
Rate Out
Output 2
Gnd.
Rate In
GND
S
p
e
e
d
S
e
n
s
e
Rate In
S
p
e
e
d
C
o
n
tr
o
l
A
ir
T
e
m
p
Rate Out
G
N
D
Output 2
+24VDC
TEMP
GND
G
N
D
Drying Air Temperature
4
RED
BLACK
WHITE
GROUND
SHIELD
GROUND
Drying Air
Temperature
Sensor
4
RED
BLACK
WHITE
To pigtail in vertical
wire tray
Solid State Temperature probe
Signal specification
Red
= 18 to 30 vdc, 2mA
Black = Gnd.
White = Temperature signal
Dryer Master DM510
This device measures the temperature of the drying air in the air plenum. If the temperature
controller for the dryer does not have a scaled output use the Drying Air Temperature Sensor
supplied with the DM510. For both options remember to attach the Multi-cable shield to ground at
Dryer Master end and insulate it on the other end.
Mount the Drying Air Temperature Sensor within one foot of the existing temperature sensor in the
hot zone of the dryer. Both sensors should be at the same height. Use high temperature wire from
the Drying Air Temperature Sensor to the outside of the hot zone. At this point the standard two
pair shielded cable can be used.
Hint
Caulk the conduit entry into the hot zone of the dryer with silicone. This avoids a hot draft
heating up the conduit near your splice.
Figure 43 - Drying Air Temperature Sensor Wiring
Summary of Contents for DM510
Page 1: ...INSTALLATION GUIDE ...