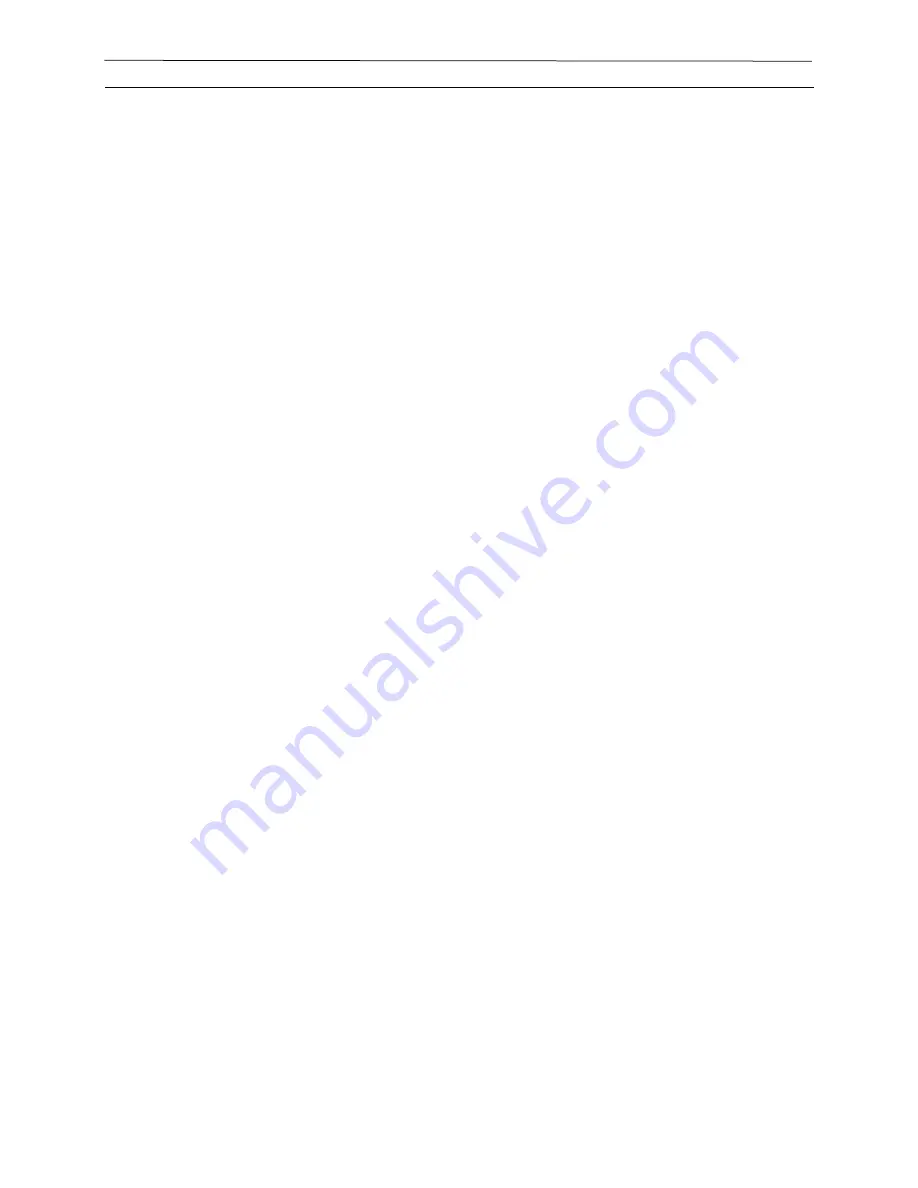
Page | 27
Dryer Master DM510
Installation Manual
Outlet Moisture Sensor Installation
Sensor Types
The standard fin type outlet moisture sensor for new installations is identical to the inlet fin sensor.
The two sensors are typically interchangeable.
The sensor is designed to fit into a 6" X 6" chute. It will also fit the standard GSI/Zimmerman chute
(with only a slight modification to the chute).
Dryer Master also offers a Round Cell moisture sensor with a restrictor plate (see Appendix 4. Figure 59 -
Round Cell Sensor) This may be appropriate for some installations. If you are in doubt about which sensor
to use call us at the Dryer Master Support Center and we will go over the pros and cons of each option
with you.
There are a number of installation requirements which are outlined below. If at any time you have
questions about the preferred option for installing the outlet sensor contact us at the Dryer Master
Support Center.
Outlet sensor mounting requirements:
Dryer Master offers 2 versions of its outlet sensor chute with a rotary feed. The two versions
(“Bypass” and “In
-
line”) are explained in Appendix 3. The use
of one of these chute options is
strongly recommended and will greatly simplify the installation.
Any outlet sensor installation needs to fulfill a number of requirements as outlined below:
1
. The chute needs to hold a compacted yet flowing sample of grain (minimum possible airspace
between kernels)
2
. Sample size needs to be large enough to have statistical relevance
3
. Sensor needs to be mounted in a
vertical
position to minimize the influence of fines on the
moisture reading
4
. Operator must be able to physically confirm the product flow through the sensor chute
5
. Operator needs to be able to sample product at the sensor for calibration purposes
6
. Operator should be able to shut the flow of grain off in the sensor chute to service the sensor
and/or clear debris
7
. Operator should use a rotary metering device to restrict/meter flow or have several restrictor
plates with varying hole sizes to be able to adjust the flow rate to accommodate changing kernel size
or a change in commodity
8
. Flow rate must be fast enough to keep the measured sample relevant yet slow enough to ensure
product compaction and minimize mechanical wear
(less than 1” per second)
9
. When using restrictor plates to adjust the flow rate the restrictor plate should be 6+ inches below
the sensor fin to minimize the fines building up into the sensing area and influencing the moisture
readings
10
. Sensor chute must remain completely full and overflowing to give consistent readings, even at
the lowest unload rate expected in use.
Summary of Contents for DM510
Page 1: ...INSTALLATION GUIDE ...