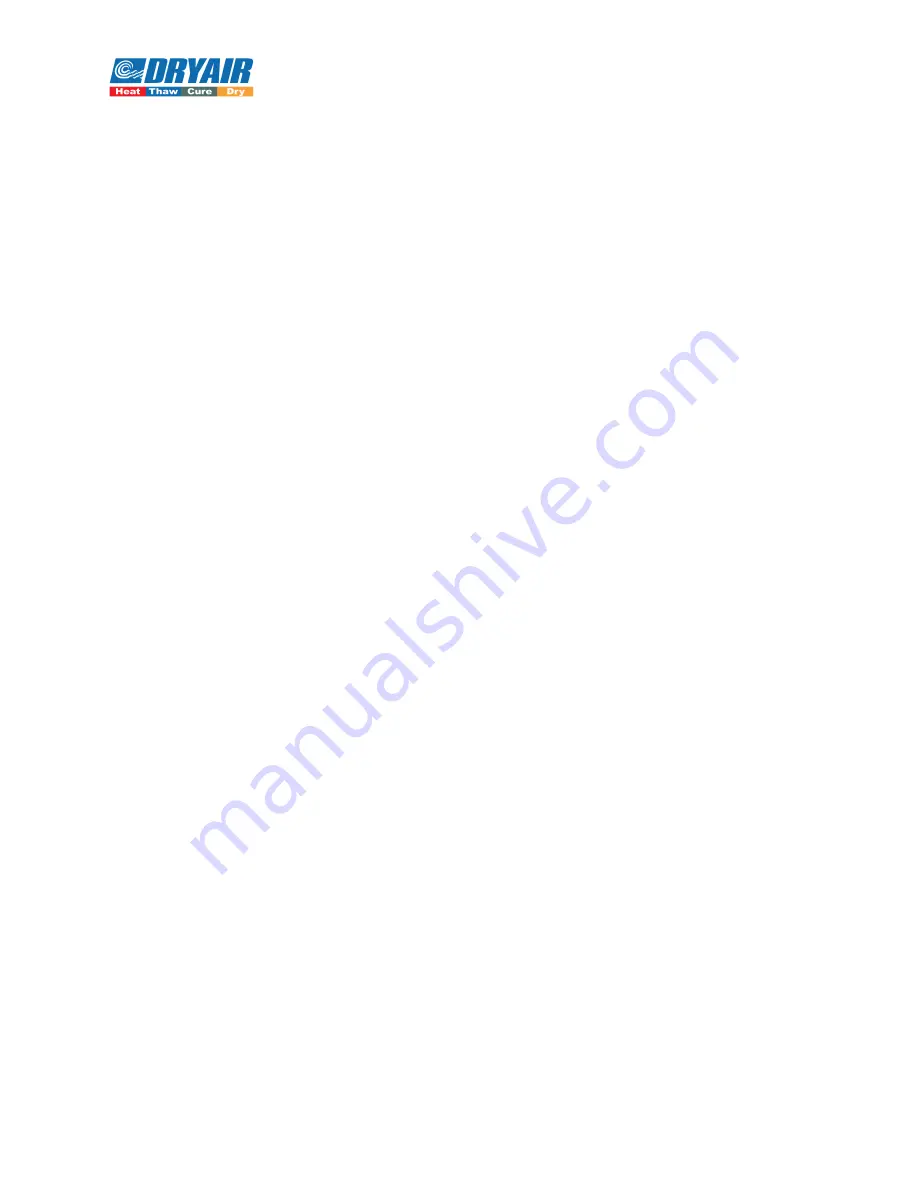
Appendix
will take but in any event, it will take much longer compared to using the preheater
on the DRYAIR unit.
•
If the unit does start in cold temperatures, there is potential for the heat exchanger to
accumulate soot due to not having a controlled environment of air and fuel going into
the burner. Sooting will stop after the unit warms up if the settings on the burner are
correct. Every 1 mm of soot accumulated on the heat exchanger results in a 5% loss
of efficiency compared to a clean exchanger. Running the preheater on the DRYAIR
unit eliminates the need to adjust burner settings in reaction to changing weather
conditions.
•
Decreases heat exchanger service life.
•
Increases maintenance costs due to added stress on all components during cold
startups.
In Conclusion:
Using the preheater as instructed in the manual will allow you to operate DRYAIR units in
colder climates without sacrificing efficiency or long term reliability of the unit. DRYAIR
recommends planning ahead and starting the preheater to allow it to run while the units is in
transit to the jobsite (running on generator power) and while operators are reeling out and
placing hose on the site. This will still make for productive use of the time while allowing the
unit to benefit from the patented preheater feature. If the operator decided they do not want to
wait for the preheater to work, the DRYAIR unit will perform just like any of our competitor’s
units that do not have a preheater option.
9-8
Summary of Contents for 600 GTS Series
Page 2: ......
Page 47: ...Appendix 9 3 Electrical Schematics Figure 56 600 GTS sub 40 Electrical Schematic...
Page 48: ...Appendix 9 4 Figure 57 600 GTS Electrical Schematic...
Page 49: ...Appendix 9 5 Figure 58 HR2250 Electrical Schematic...
Page 50: ...Appendix 9 6 Figure 59 Trailer Wiring Schematic...