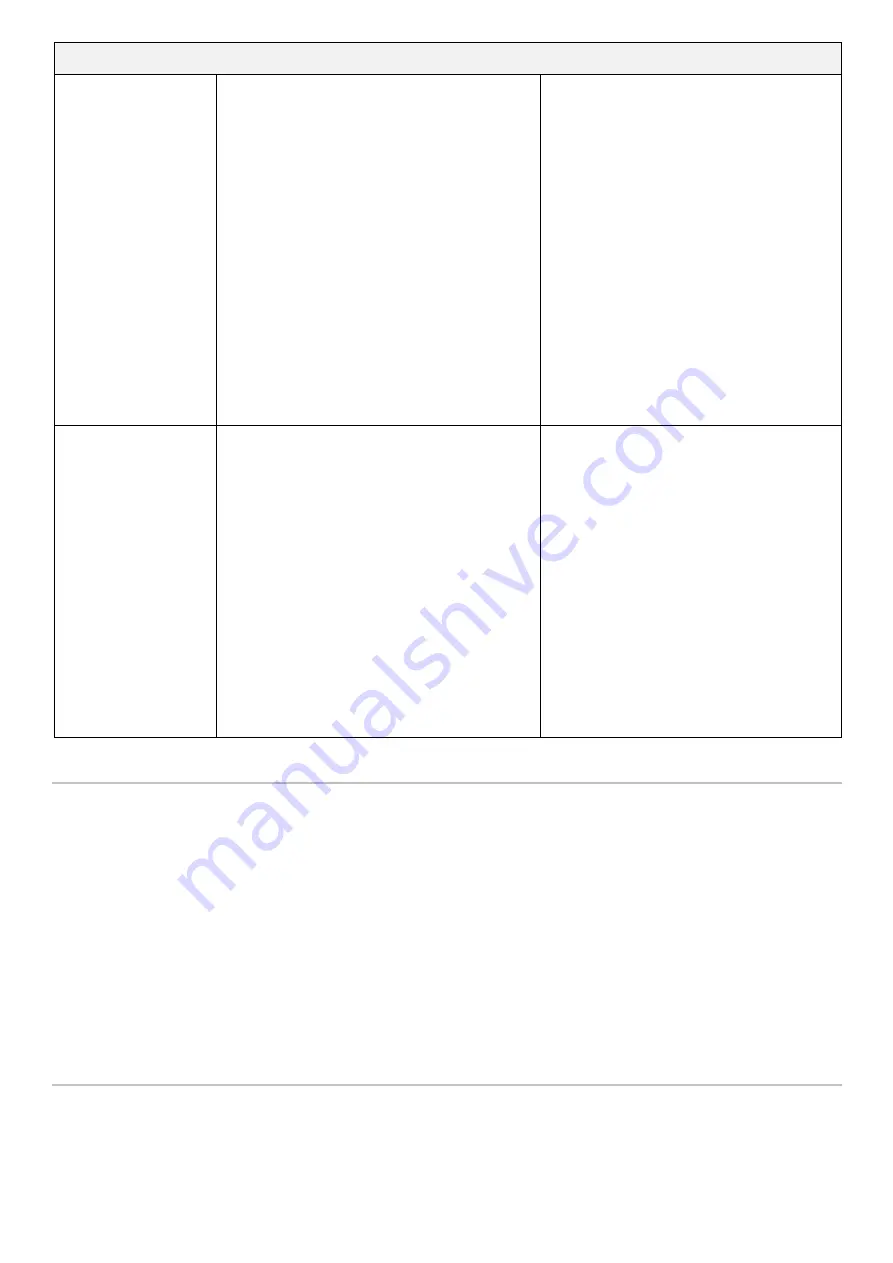
17/ 22
Lubrication installation accessories
METERING UNIT AG6
Alarm signal indicating
non-delivery
of
lubricant. The small rods
visible
inside
the
metering unit turrets
must move sequentially
up
and
down
and
activate
the
control
microswitch when the
pump is working. If this
is not the case the two
outlets or the single
outlet of that metering
unit will not deliver
lubricant.
Metering unit small piston jammed.
Piping between metering unit outlet and point
requiring lubrication obstructed.
Pressure on the line too low (the lubricant is not
delivered by any outlet or only by a few outlets).
Metering unit arranged for two outlets by used for
only one outlet.
Replace the metering unit with another one
having the same characteristics. However it is
advisable to make sure that the metering units
have been correctly assembled, particularly
with regard to fixing. Over-locking of the fixing
screws may damage the metering unit and
cause the small piston to jam.
Remove the outlet pipe and check to see if the
metering unit is delivering lubricant.
Change the pressure control valve adjustment
(bypass) or the adjustment of the control
pressure gauge (and of line).
Check that, when one single outlet is used, the
right pad is assembled and that the other
outlet is sealed.
See instruction sheet for AG6 metering units.
END OF LINE PRESSURE
GAUGE
The pressure gauge is
not sending the signal to
the electric command
and control panel.
The
pressure
gauge
sends the signal before
the
end
of
the
lubrication cycle.
Electrical connection incorrect.
Incorrect adjustment of the control pressure
gauge. The pressure value set is too high and the
pressure adjustment valve (bypass) intervenes
before the pressure gauge can be activated.
Incorrect adjustment of the control pressure
gauge. The pressure value set is too low.
Check the electrical connection.
Reduce the pressure gauge calibration pressure
until an electrical contact is obtained.
Increase the pressure gauge calibration valve.
The optimum calibration value is the one which
allows a pressure of 50-70 bar (735 – 1029 psi)
at the end of the lubrication line.
9. MAINTENANCE PROCEDURES
Use the individual protective devices needed to avoid contact with mineral oil or grease.
Regular inspection
The following regular checks must be carried out:
the lubrication status
1000 hours
Cleanliness of the loading and suction filter
4000 hours
The machine does not require any special equipment for any checking and/or maintenance activity, however the
recommendation is to use suitable equipment which is in a good condition in order to avoid causing damage to persons or
machine parts (according to current regulation).
If necessary clean the tank paying due attention (when the machine is off and without it being possible to restart it). Remember
to reseal the tank once the operation has been completed.
Make sure that the electric and hydraulic supply has been disconnected before carrying out any maintenance intervention.
10. DISPOSAL
In the course of machine maintenance, or if the machine is scrapped, do not dispose of polluting parts into the environment.
Refer to local regulations with regard to their correct disposal. When scrapping the machine the identification plate and any
other documents must be destroyed.