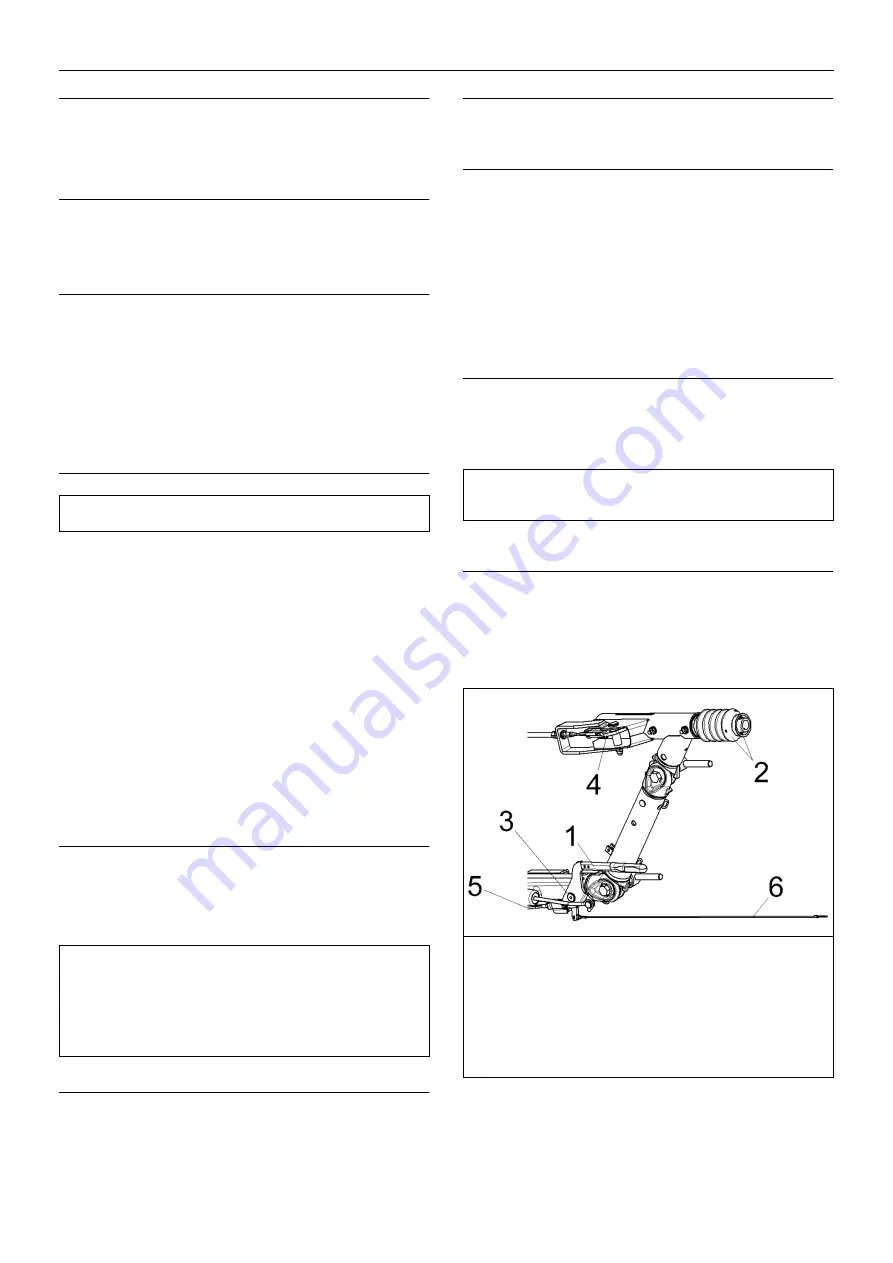
64
MAINTENANCE
12/154
FUEL FILTER WATER SEPARATOR
The fuel filter water separator contains a filter element which should
be replaced at regular intervals (see the SERVICE/MAINTENANCE
CHART).
CHARGE COOLER PIPEWORK
Inspect all hoses and clips on the charge cooler pipe work.
Engine damage will occur if the charge cooling system leaks.
HOSES
All components of the engine cooling air intake system should be
checked periodically to keep the engine at peak efficiency.
At the recommended intervals, (see the SERVICE/MAINTENANCE
CHART), inspect all of the intake lines to the air filter, and all flexible
hoses used for air lines, oil lines and fuel lines.
Periodically inspect all pipework for cracks, leaks, etc. and replace
immediately if damaged.
ELECTRICAL SYSTEM
When removing connectors from electrical devices and sensors,
inspect the terminals to ensure they have electrical grease on them. If
electrical grease is not present or very minimal, then add a small
amount of Doosan Part No. 22409114 electrical grease to the
terminals. Dirty and or corroded electrical terminals can be cleaned
using electrical contact cleaner.
Inspect the safety shutdown system switches and the instrument
panel relay contacts for evidence of arcing and pitting. Clean where
necessary.
Check the mechanical action of the components.
Check the security of electrical terminals on the switches and relays
i.e. nuts or screws loose, which may cause local hot spot oxidation.
Inspect the components and wiring for signs of overheating i.e.
discolouration, charring of cables, deformation of parts, acrid smells
and blistered paint.
BATTERY
Keep the battery terminals and cable clamps clean and lightly
coated with petroleum jelly to prevent corrosion.
The retaining clamp should be kept tight enough to prevent the
battery from moving.
PRESSURE SYSTEM
At 3 month intervals it is necessary to inspect the external surfaces
of the system (from the airend through to the discharge valve(s))
including hoses, tubes, tube fittings and the separator tank, for visible
signs of impact damage, excessive corrosion, abrasion, tightness and
chafing. Any suspect parts should be replaced before the machine is
put back into service.
TYRES/TYRE PRESSURE
Tyre Pressure: 600kPa.
RUNNING GEAR/WHEELS
Check the wheel nut torque 20 miles (30 kilometres) after refitting
the wheels. Refer to the
TORQUE SETTING TABLE
later in this
section.
Lifting jacks should only be used under the axle.
The bolts securing the running gear to the chassis should be
checked periodically for tightness (refer to the
SERVICE/
MAINTENANCE CHART
for frequency) and re-tightened where
necessary. Refer to the
TORQUE SETTING TABLE
later in this
section.
BRAKES
Check and adjust the brake linkage at 500 miles (850km) then every
3000 miles (5000km) or 3 months (whichever is the sooner) to
compensate for any stretch of the adjustable cables. Check and adjust
the wheel brakes to compensate for wear.
ADJUSTING THE OVERRUN BRAKING SYSTEM
(KNOTT RUNNING GEAR)
1. Preparation
Jack up the machine
Disengage the handbrake lever [1].
Fully extend the draw bar [2] on the overrun braking system.
Requirements:
During the adjustment procedure always start with the wheel brakes.
Always rotate the wheel in the direction of forward movement.
Ensure that an M10 safety screw is fitted to the handbrake pivot.
WARNING: Always disconnect the battery switch before
performing any maintenance or service.
CAUTION:
Exercise extreme caution when using booster battery. To
jump battery, connect ends of one booster cable to the positive (+)
terminal of each battery. Connect one end of other cable to the
negative (-) terminal of the booster battery and other end to a ground
connection away from dead battery (to avoid a spark occurring near
any explosive gases that may be present). After starting the
compressor, always disconnect cables in reverse order.
CAUTION:
Check the wheel nut torque 20 miles (30 kilometres) after
refitting the wheels (Refer to the TORQUE SETTING TABLE later in
this section).
1. Handbrake lever
2. Draw bar and bellows
3. Handbrake lever pivot
4. Transmission lever
5. Brake cable
6. Breakaway Cable
Summary of Contents for 12/154
Page 2: ......
Page 4: ......
Page 84: ...80 MACHINE SYSTEMS 12 154 page ...
Page 86: ...82 MACHINE SYSTEMS 12 154 ...
Page 88: ...84 MACHINE SYSTEMS 12 154 ...
Page 90: ...86 MACHINE SYSTEMS 12 154 ...
Page 92: ...88 MACHINE SYSTEMS 12 154 ...
Page 94: ...90 MACHINE SYSTEMS 12 154 ...
Page 108: ......