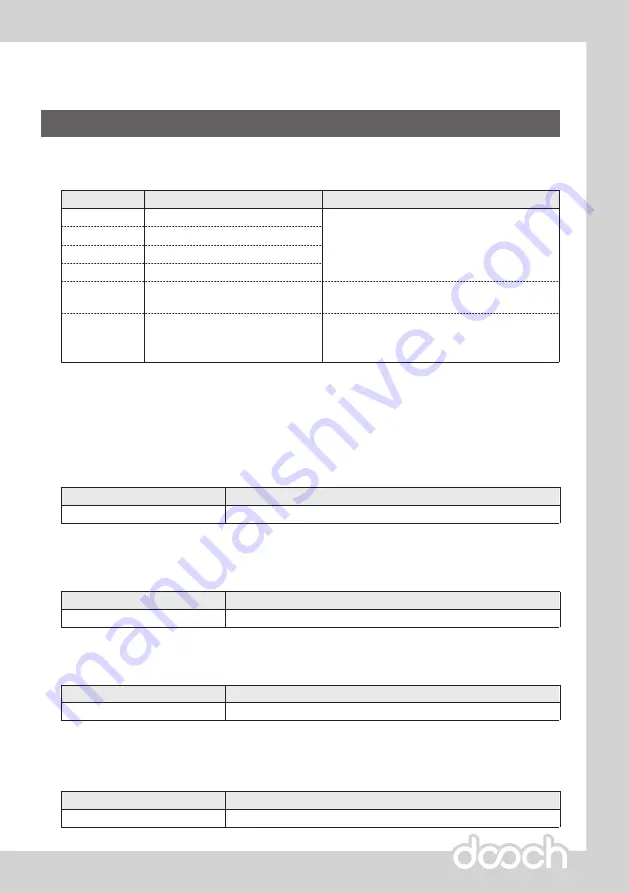
Chapter 6. Function Table & Description
53
Input Range
0.0 ~ 10.0[V]
Factory Settings
0.0[V]
Functional Description
Output Current of Inverter
Set-up Data
0
Output Freq. of Inverter
1
Output Power of Inverter
2
Output Voltage of Inverter
3
Setting Pressure of Inverter
4
Drive Display Max. Value
Display a value received from an AI1value
on the screen
Setting the AI1 signal regarding pressure setting
method of Drive 3
Setting the manual mode on Pump1
Setting the AI1 signal on Drive 2 regarding
frequency setting method.
Operating frequency reference value
under Manual-Mode
5
(Factory Setting)
Signal 8 : AI1 Attribute
It sets the attribute of AI1
Signal 11 : AI2 Mode (Analog Input 2)
When Pump Control Mode is manual mode and Pressure Setting is AI2, you can setup the pressure by settings
of external input current or voltage.
Signal 12 : V2 Minimum Input Voltage
When AI2 Mode is set as a Voltage Input and you would enter the minimum Voltage coming from the external
input.
Input Range
0.0 ~ 20.0[mA]
Factory Settings
0.0[mA]
Signal 13 : I2 Minimum Input Current
When AI2 Mode is set as a Current Input and you would enter the minimum Current coming from the external
input.
Input Range
0.0 ~ 600.0
Factory Settings
0
Signal 14 : AI2 applied Min. value of attribute
A min. value of attribute corresponds to a value of current and voltage received from signal No.12, 13.
Input Range
0.0 ~ 10.0[V]
Factory Settings
10[V]
Signal 15 : Maximum Input Voltage
When AI2 Mode is set as a Voltage Input and you would enter the maximum Voltage coming from the external
input.
Summary of Contents for XQ-0075T-2
Page 1: ...XQ Drive Premium V F D INSTALLATION INSTRUCTION MANUAL...
Page 2: ......
Page 78: ...MEMO...
Page 79: ......