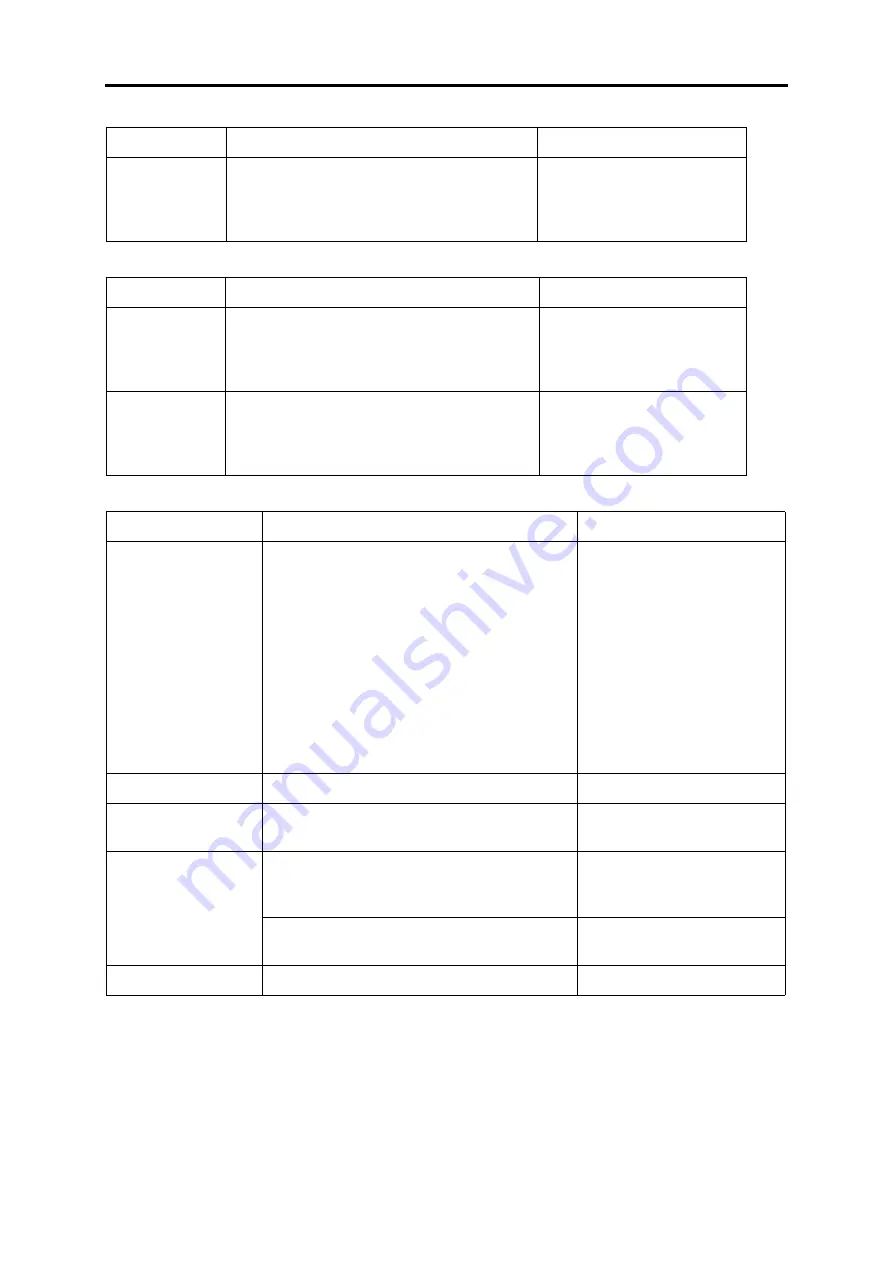
Electric and Instrument
EL-4
Fog light doesn't go on
Position light doesn't go on
Windshield and wiper
Trouble
Cause
Remedy
Fog light doesn't
go on
Fuse burnt
Earth line contacts not well
Bulb burns out
Fog light switch damages
Replace
Tighten
Replace
Replace
Trouble
Cause
Remedy
Position light
doesn't go no
when turn on the
fog light
Fog light switch damages
Bulb burns out
Replace
Replace
Position light
doesn't go on
when turn on the
signal light
Harness connecting is not firm
Combination switch circuit contacts not well
Combination switch damages
Check the connection
Connect
Repair or replace
Trouble
Cause
Remedy
Wiper doesn't operate
Fuse burnt
Circuit breaks or contacts not well
Wiper switch failed or contacts not well
Synchronous connecting board breaks away
Wiper arm's tightening bolt loosens
Wiper motor assembly failed
1.Internal coil burns out
2.Wiper motor overlade because of current over-
powering
(The rectifier is polluted, carbon, rotary bearing
is seized, wiper arm connect not well, motor
wears, constant speed gear fails)
Find out cause and replace fuse
Check and repair
Replace wiper switch
Check and repair
Tighten bolt
Check and repair wiper motor
assembly if necessary replace
parts
Motor creaks
The lube grease in the gearbox qualitative change
Replace lube grease
Wiping picture is not
correct
Wiper arm spring fatigue (pull force descends)
Wiper blade rubber damages
Replace wiper arm
Replace blade
The wiper can't return
to its original position
when turn off the
switch
Main guideline and contactor
Wilding is not good
The contactor has not good contact
Repair
Repair
Cam switch
The joint is not good
Repair or replace switch
Wiper doesn't stop
The contact is not good
Repair or replace switch
Summary of Contents for DFA1101GZ5AD6J-907
Page 1: ...DFA1101GZ5AD6J 907 SERVICE MANUAL DONGFENG AUTOMOBILE CO LTD 2006 05 ...
Page 24: ...Clutch CL 8 ...
Page 34: ...Transmission MT 9 16 Lift the countershaft out by using crane or hoist Transmission mainshaft ...
Page 63: ...Transmission MT 38 ...
Page 123: ...Brake System BR 12 ...
Page 131: ...Cab BF 7 Cab External Trims ...
Page 133: ...Cab BF 9 Front and rear window Cab door seal strip ...
Page 134: ...Cab BF 10 Door outside molding Foot step shield and mat ...
Page 149: ...Air conditioner and Heater BF 25 Schematic Circuit of Air condition System ...
Page 150: ...Air conditioner and Heater BF 26 ...
Page 165: ...Electric and Instrument EL 14 Electric wiring diagram ...