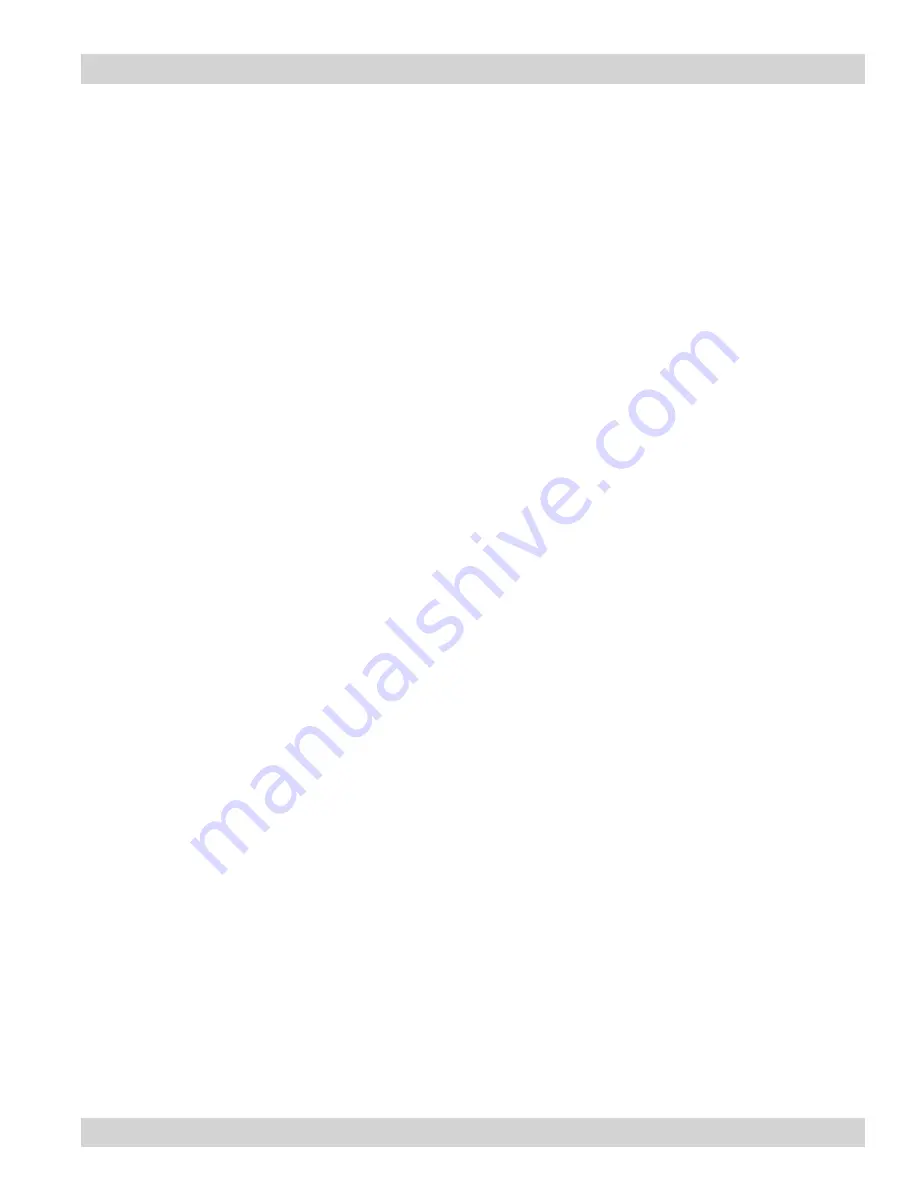
Dryflo, MMA and MMB
2
Combustible Mist Hazards
Among other considerations, the current NFPA standards require owners whose processes involve potentially combustible
materials to have a current Dust Hazard Analysis, which can serve as the foundation for their process hazard mitigation strategy.
Mitigation may include but is not limited to:
• Prevention of all ignition sources from entering any dust collection equipment.
•
Selection and implementation of fire and explosion mitigation, suppression, and isolation strategies appropriate for the
risks in their process.
• Development and use of work practices to maintain safe operating conditions, and to ensure combustible dust does not
accumulate within their plant or process equipment.
Donaldson designs, manufactures, and sells industrial air filtration products for a wide variety of applications. Some applications
may include processes or materials with inherent fire and explosion hazards. Donaldson is neither an expert nor a certified
consultant in fire, spark, or explosion detection, suppression, or control. Donaldson does not provide engineering consulting
services related to process or dust hazard analyses, or code and standard compliance. Complying with applicable codes and
standards and managing the risks associated with the process or materials remains the responsibility of the process owner/
operator. Donaldson may provide referrals to consultants, suppliers of equipment or services related to the detection and/
or mitigation of sparks, fires and/or explosions, but Donaldson does not assume responsibility for any such referrals, nor does
Donaldson assume any liability for the fitness of a mitigation strategy or product for a particular installation or application. The
process owner’s final selection of dust collectors and risk mitigation strategies should be based on the outcome of a Dust Hazard /
Process Hazard Analysis performed by the process owner. Although early engagement of a dust collector supplier provides helpful
insights on the availability and features of various products, process owners should consult with a combustible dust expert and/or a
process safety expert before making actual product and mitigation strategy selections.
Donaldson recommends that all industrial air filtration system designs be reviewed and approved by an expert consultant who is
responsible for the integrity of the system design and compliance with applicable codes and standards. It is the process owner’s
responsibility to understand the risks in their process and mitigate those risks in accordance with all applicable laws, regulations
and standards, including those published by the NFPA. Donaldson also recommends that proper maintenance and housekeeping
procedures and work practices be evaluated, developed, and followed to maintain any industrial air filtration products in safe
operating condition.
Many factors beyond the control of Donaldson can affect the use and performance of Donaldson products in a particular
application, including the conditions under which the product is used. Since these factors are uniquely within the user’s knowledge
and control, it is essential the user evaluate the Donaldson products to determine whether the product is fit for the particular
purpose and suitable for the user’s application. All products, product specifications, and data (airflow, capacity, dimensions, or
availability) are subject to change without notice, and may vary by region or country.