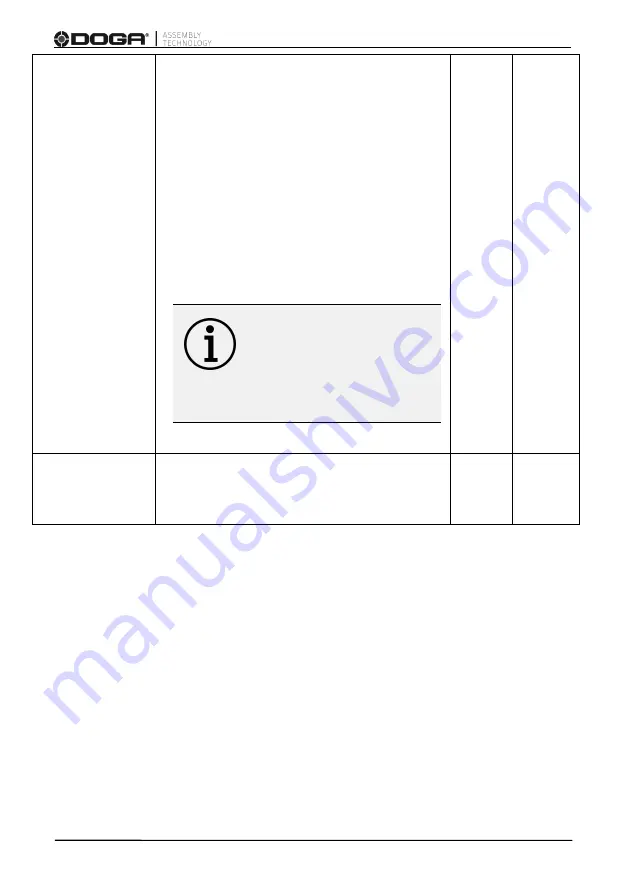
User manual DPC Touch V2
DOC.60352-11/20
22
Temporary
position loss
time, ms
If fastening is started (Motor Run signal is
received), then it is allowed to exit
position
OK
zone
(green)
into
approaching area (orange) for the
specified time without locking the tool. If
this time limit is passed the tool will be
instantly locked. If position NOK zone
(red) is entered the tool will be instantly
locked.
Information
this parameter is used to
avoid
interruptions
of
fastening process when position is
lost for short time due to vibrations.
0 -
3000
50
Judging time,
ms
Judging time is used if Fastening OK
signal is delayed after the fall of Motor run
signal.
0 - 500
100