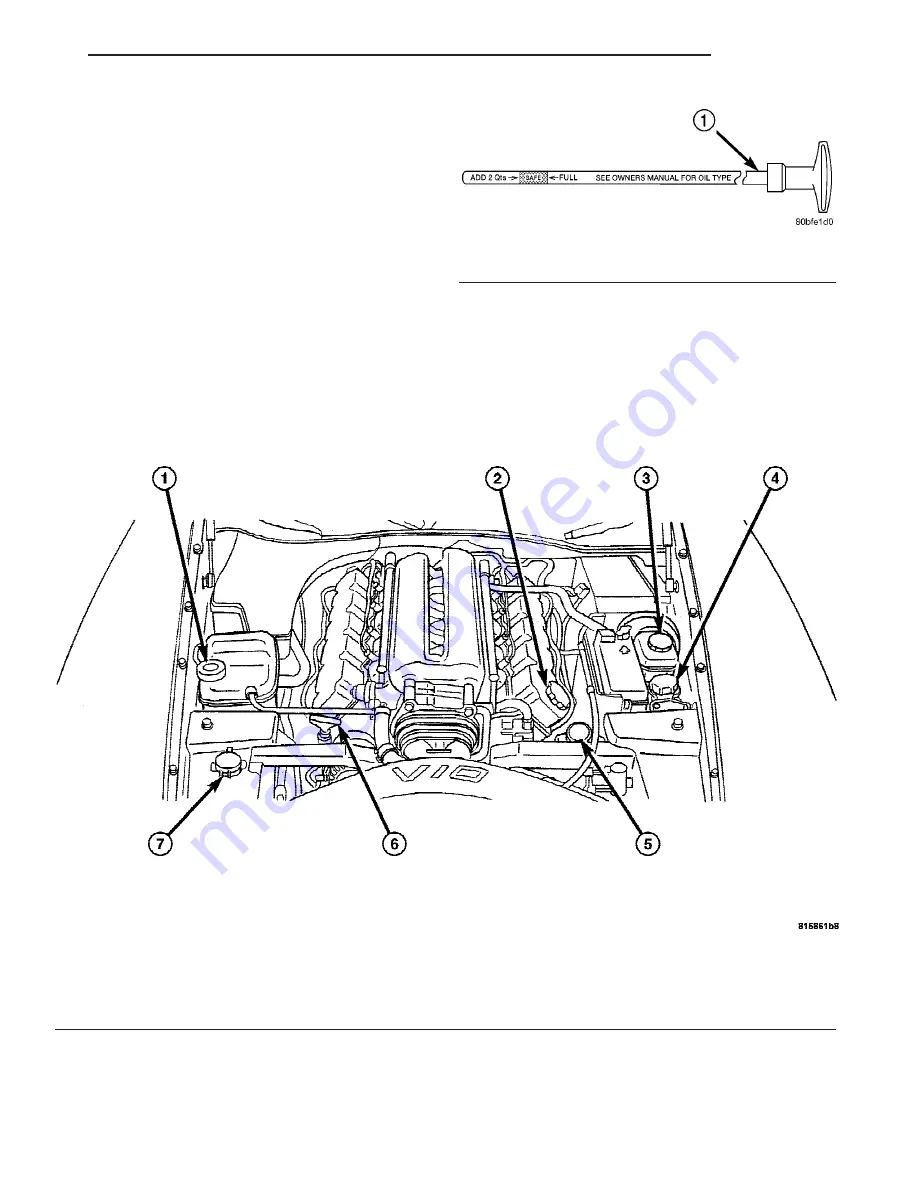
OIL
STANDARD PROCEDURE
CHECKING ENGINE OIL LEVEL
The best time to check engine oil level is after the
vehicle has sat overnight. If the engine has been run-
ning, allow the engine to be shut off for at least 5
minutes before checking oil level.
Checking the oil while the vehicle is on level
ground will improve the accuracy of the oil level
reading. Remove the engine oil dipstick (Fig. 61). The
dipstick is calibrated for 2 quarts within the SAFE
zone (Fig. 62).
Fig. 61 Fluid Level Service Locations
1 - COOLANT PRESSURE CAP
2 - ENGINE OIL FILL
3 - BRAKE FLUID RESERVOIR
4 - CLUTCH FLUID RESERVOIR
5 - POWER STEERING FLUID
6 - ENGINE OIL DIPSTICK
7 - WINDSHIELD WASHER FLUID RESERVOIR
Fig. 62 Engine Oil Level
1 - ENGINE OIL DIPSTICK
ZB
ENGINE
9 - 45
Summary of Contents for ZB 2005
Page 4: ......
Page 8: ...FASTENER STRENGTH ZB INTRODUCTION 3 FASTENER IDENTIFICATION Continued...
Page 11: ...METRIC CONVERSION CHART 6 INTRODUCTION ZB METRIC SYSTEM Continued...
Page 13: ...TORQUE SPECIFICATIONS 8 INTRODUCTION ZB TORQUE REFERENCES Continued...
Page 29: ......
Page 103: ...Fig 24 Dynamic Toe Pattern Graph 2 74 WHEEL ALIGNMENT ZB WHEEL ALIGNMENT Continued...
Page 125: ......
Page 233: ......
Page 237: ......
Page 245: ......
Page 275: ......
Page 295: ......
Page 339: ......
Page 355: ......
Page 373: ......
Page 375: ......
Page 391: ......
Page 395: ......
Page 396: ......
Page 397: ......
Page 398: ......
Page 399: ......
Page 400: ......
Page 401: ......
Page 402: ......
Page 403: ......
Page 404: ......
Page 405: ......
Page 406: ......
Page 407: ......
Page 408: ......
Page 409: ......
Page 410: ......
Page 411: ......
Page 412: ......
Page 413: ......
Page 415: ......
Page 416: ......
Page 417: ......
Page 418: ......
Page 419: ......
Page 420: ......
Page 421: ......
Page 422: ......
Page 423: ......
Page 424: ......
Page 425: ......
Page 427: ......
Page 428: ......
Page 429: ......
Page 431: ......
Page 432: ......
Page 433: ......
Page 435: ......
Page 436: ......
Page 437: ......
Page 439: ......
Page 440: ......
Page 441: ......
Page 442: ......
Page 443: ......
Page 444: ......
Page 445: ......
Page 446: ......
Page 447: ......
Page 448: ......
Page 449: ......
Page 450: ......
Page 451: ......
Page 452: ......
Page 453: ......
Page 455: ......
Page 456: ......
Page 457: ......
Page 459: ......
Page 460: ......
Page 461: ......
Page 462: ......
Page 463: ......
Page 465: ......
Page 466: ......
Page 467: ......
Page 468: ......
Page 469: ......
Page 470: ......
Page 471: ......
Page 473: ......
Page 474: ......
Page 475: ......
Page 477: ......
Page 478: ......
Page 479: ......
Page 480: ......
Page 481: ......
Page 482: ......
Page 483: ......
Page 485: ......
Page 486: ......
Page 487: ......
Page 489: ......
Page 490: ......
Page 491: ......
Page 492: ......
Page 493: ......
Page 495: ......
Page 496: ......
Page 497: ......
Page 498: ......
Page 499: ......
Page 500: ......
Page 501: ......
Page 502: ......
Page 503: ......
Page 504: ......
Page 505: ......
Page 506: ......
Page 507: ......
Page 508: ......
Page 509: ......
Page 510: ......
Page 511: ......
Page 513: ......
Page 514: ......
Page 515: ......
Page 516: ......
Page 517: ......
Page 519: ......
Page 521: ......
Page 522: ......
Page 523: ......
Page 524: ......
Page 525: ......
Page 527: ......
Page 528: ......
Page 529: ......
Page 530: ......
Page 531: ......
Page 533: ......
Page 534: ......
Page 535: ......
Page 537: ......
Page 538: ......
Page 539: ......
Page 541: ......
Page 543: ......
Page 544: ......
Page 545: ......
Page 547: ......
Page 548: ......
Page 549: ......
Page 550: ......
Page 551: ......
Page 553: ......
Page 555: ......
Page 556: ......
Page 557: ......
Page 659: ......
Page 751: ......
Page 764: ...Fig 15 X Y AND Z PLANES ZB FRAME BUMPERS 13 13 FRAME Continued...
Page 765: ...Fig 16 FRAME SIDE VIEW FRONT SECTION Z DIMENSIONS 13 14 FRAME BUMPERS ZB FRAME Continued...
Page 766: ...Fig 17 FRAME SIDE VIEW REAR SECTION Z DIMENSIONS ZB FRAME BUMPERS 13 15 FRAME Continued...
Page 767: ...Fig 18 FRAME SIDE VIEW FRONT SECTION X DIMENSIONS 13 16 FRAME BUMPERS ZB FRAME Continued...
Page 768: ...Fig 19 FRAME SIDE VIEW REAR SECTION X DIMENSIONS ZB FRAME BUMPERS 13 17 FRAME Continued...
Page 769: ...Fig 20 FRAME TOP VIEW FRONT SECTION X AND Y DIMENSIONS 13 18 FRAME BUMPERS ZB FRAME Continued...
Page 770: ...Fig 21 FRAME TOP VIEW REAR SECTION X AND Y DIMENSIONS ZB FRAME BUMPERS 13 19 FRAME Continued...
Page 773: ......
Page 891: ......
Page 906: ...Vehicle Lead Correction Diagnosis Chart ZB TIRES WHEELS 22 15 TIRES Continued...
Page 911: ......
Page 925: ...Fig 1 EXPLODED VIEW 23 14 CONVERTIBLE TOP ZB CONVERTIBLE TOP Continued...
Page 1009: ...Fig 6 TRUNK OPENING DIMENSIONS 23 98 BODY STRUCTURE ZB OPENING DIMENSIONS Continued...
Page 1011: ...Fig 8 FRONT OF DASH PANEL AND FRAME 23 100 BODY STRUCTURE ZB SEALER LOCATIONS Continued...
Page 1012: ...Fig 9 REAR CLIP FRAME ZB BODY STRUCTURE 23 101 SEALER LOCATIONS Continued...
Page 1016: ...Fig 13 FRONT FRAME STRUCTURE 1 OF 4 23 104 BODY STRUCTURE ZB WELD LOCATIONS Continued...
Page 1017: ...Fig 14 FRONT FRAME STRUCTURE 2 OF 4 ZB BODY STRUCTURE 23 105 WELD LOCATIONS Continued...
Page 1018: ...Fig 15 FRONT FRAME STRUCTURE 3 OF 4 23 106 BODY STRUCTURE ZB WELD LOCATIONS Continued...
Page 1019: ...Fig 16 FRONT FRAME STRUCTURE 4 OF 4 ZB BODY STRUCTURE 23 107 WELD LOCATIONS Continued...
Page 1020: ...Fig 17 FLOOR PAN 1 OF 5 23 108 BODY STRUCTURE ZB WELD LOCATIONS Continued...
Page 1021: ...Fig 18 FLOOR PAN 2 OF 5 ZB BODY STRUCTURE 23 109 WELD LOCATIONS Continued...
Page 1022: ...Fig 19 FLOOR PAN 3 OF 5 23 110 BODY STRUCTURE ZB WELD LOCATIONS Continued...
Page 1023: ...Fig 20 FLOOR PAN 4 OF 5 ZB BODY STRUCTURE 23 111 WELD LOCATIONS Continued...
Page 1024: ...Fig 21 FLOOR PAN 5 OF 5 23 112 BODY STRUCTURE ZB WELD LOCATIONS Continued...
Page 1025: ...Fig 22 REAR FRAME 1 OF 5 ZB BODY STRUCTURE 23 113 WELD LOCATIONS Continued...
Page 1026: ...Fig 23 REAR FRAME 2 OF 5 23 114 BODY STRUCTURE ZB WELD LOCATIONS Continued...
Page 1027: ...Fig 24 REAR FRAME 3 OF 5 ZB BODY STRUCTURE 23 115 WELD LOCATIONS Continued...
Page 1028: ...Fig 25 REAR FRAME 4 OF 5 23 116 BODY STRUCTURE ZB WELD LOCATIONS Continued...
Page 1029: ...Fig 26 REAR FRAME 5 OF 5 ZB BODY STRUCTURE 23 117 WELD LOCATIONS Continued...
Page 1089: ......
Page 1111: ......
Page 1121: ...NOTES vi...
Page 1136: ...7 0 DIAGNOSTIC INFORMATION AND PROCEDURES 15...
Page 1341: ...NOTES 220...
Page 1344: ...8 4 FUEL SYSTEM C O M P O N E N T L O C A T I O N S 223 COMPONENT LOCATIONS...
Page 1345: ...C O M P O N E N T L O C A T I O N S 224 COMPONENT LOCATIONS 8 4 FUEL SYSTEM Continued...
Page 1355: ...C O N N E C T O R P I N O U T S 234 CONNECTOR PINOUTS...
Page 1362: ...10 0 SCHEMATIC DIAGRAMS S C H E M A T I C D I A G R A M S 241 SCHEMATIC DIAGRAMS...
Page 1363: ...S C H E M A T I C D I A G R A M S 242 SCHEMATIC DIAGRAMS...
Page 1364: ...S C H E M A T I C D I A G R A M S 243 SCHEMATIC DIAGRAMS...
Page 1365: ...NOTES 244...
Page 1368: ...11 4 EELD C H A R T S A N D G R A P H S 247 CHARTS AND GRAPHS...
Page 1369: ...NOTES 248...
Page 1371: ...Dealer Technical Operations 800 Chrysler Drive CIMS 486 02 76 Auburn Hills MI 48326 2757...
Page 1381: ...NOTES x...
Page 1407: ...NOTES 26...
Page 1408: ...7 0 DIAGNOSTIC INFORMATION AND PROCEDURES 27...
Page 1789: ...NOTES 408...
Page 1795: ...NOTES 414...
Page 1803: ...10 2 AUDIO SYSTEM S C H E M A T I C D I A G R A M S 422 SCHEMATIC DIAGRAMS...
Page 1804: ...10 3 CHIME SYSTEM S C H E M A T I C D I A G R A M S 423 SCHEMATIC DIAGRAMS...
Page 1805: ...10 4 COMMUNICATION S C H E M A T I C D I A G R A M S 424 SCHEMATIC DIAGRAMS...
Page 1808: ...10 7 2 REAR FOG LAMPS EXPORT ONLY S C H E M A T I C D I A G R A M S 427 SCHEMATIC DIAGRAMS...
Page 1809: ...10 8 HEATING A C SYSTEM S C H E M A T I C D I A G R A M S 428 SCHEMATIC DIAGRAMS...
Page 1813: ...10 11 INTERIOR LIGHTING S C H E M A T I C D I A G R A M S 432 SCHEMATIC DIAGRAMS...
Page 1814: ...10 12 POWER DOOR LOCKS RKE S C H E M A T I C D I A G R A M S 433 SCHEMATIC DIAGRAMS...
Page 1815: ...10 13 POWER WINDOW SYSTEM S C H E M A T I C D I A G R A M S 434 SCHEMATIC DIAGRAMS...
Page 1817: ...10 15 VEHICLE THEFT SECURITY SYSTEM S C H E M A T I C D I A G R A M S 436 SCHEMATIC DIAGRAMS...
Page 1819: ...NOTES 438...
Page 1829: ...NOTES 8...
Page 1830: ...7 0 DIAGNOSTIC INFORMATION AND PROCEDURES 9...
Page 1868: ...C O N N E C T O R P I N O U T S 47 CONNECTOR PINOUTS...
Page 1871: ...NOTES 50...
Page 1873: ...NOTES 52...