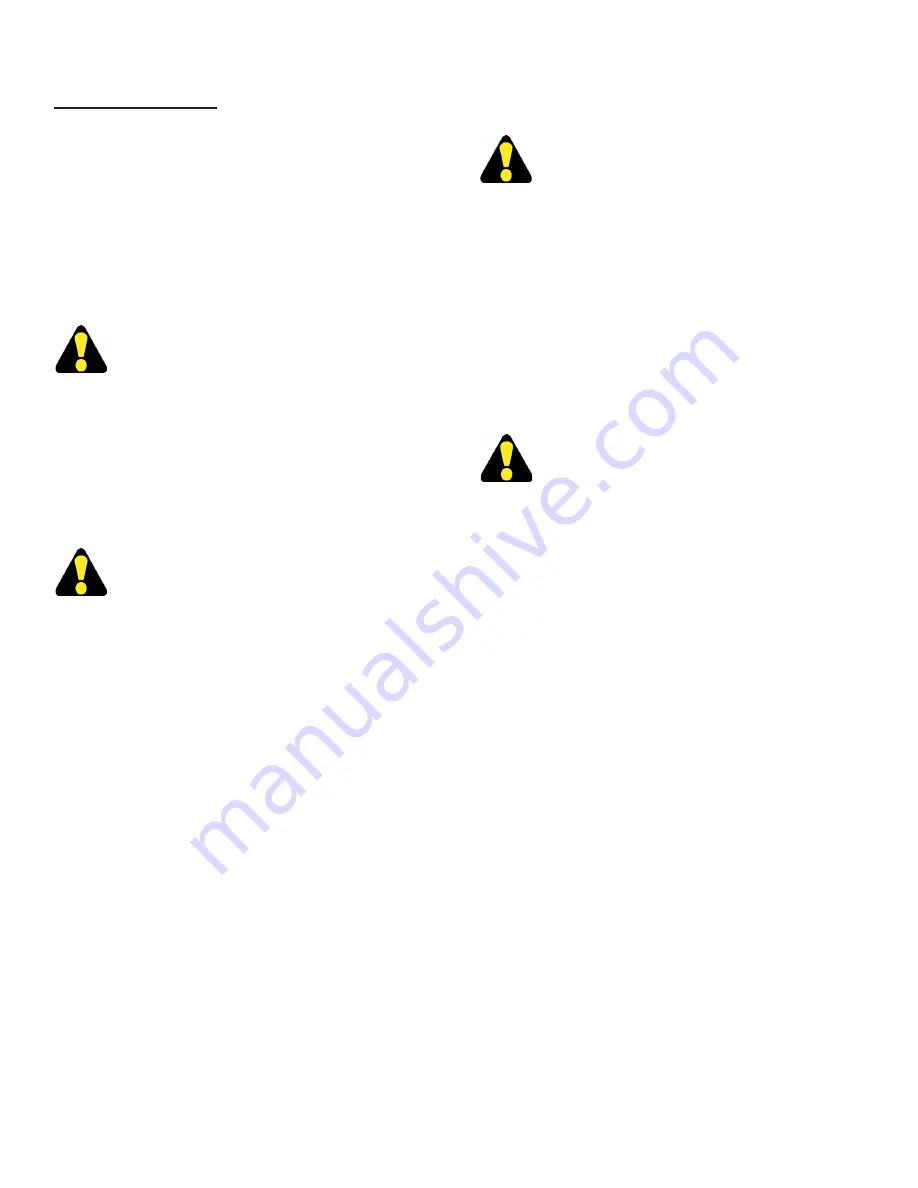
8
FLOOR INSTALLATION (Continued....)
Relocation Procedures
1.
Should machine relocation become necessary at a
later date, it will be extremely important to protect
the frame against undue stress. Before moving,
reinstall the shipping bracket (if supplied) or use
strapping to connecting the saw head to the base.
2.
To move the machine, follow the instructions on
lifting stated previously.
ELECTRICAL INSTALLATION
Electrical installation must be made by
authorized electrical maintenance personnel!
1.
Bring the incoming line circuit leads to the
disconnect switch terminals in the electrical control
box enclosure attached to the right side of the
machine base. Refer to the furnished electrical
schematic, if necessary.
2.
Turn the electrical supply and machine disconnect
switch to "ON".
See the
"Operation"
section later in this
manual on how to operate the workstation
controls such as starting the hydraulics,
etc.
3.
Start the hydraulics. Then raise the saw head.
If
the hydraulic motor rotates correctly, the saw head
will now raise from the full down position.
4.
If the saw head does not raise, it means that the
hydraulic motor’s rotation is reversed (this can
be verified by observing motor rotation). Motor
rotation must be according to the arrow on the
pump body.
Hydraulic system operation cannot
be maintained if the saw head is not raised.
5.
If hydraulic pump motor rotation is reversed:
(a)
Turn
the disconnect switch to "OFF" and remove power
at the source of electrical supply;
(b)
Interchange
two (2) of the L1, L2, or L3 leads to the disconnect
switch;
(c)
Restore power and perform Step 3
again.
PLANT AIR INSTALLATION
1.
Plant air is required to operate the optional mist
lubricator system.
2.
Plant air is connected at the air filter on the lower
base in the rear of the machine. Air pressure should
be in the range of 80 to 90 psi (5.5 to 6.2 bar or 5.6
to 6.3 kg/cm²).
DO NOT exceed 90 psi (6.2 bar or 6.3 kg/
cm²).
PREPARATION FOR USE
1.
If required, fill the coolant and hydraulic reservoirs
with fluid recommended in the Lubrication Chart.
Be sure that all other points listed in the Lubrication
Chart have been checked and/or serviced.
2.
Make electrical connections to the machine while
referring to the electrical schematic.
3.
All covers and guards must be in place and all doors
must be closed.
DO NOT defeat the purpose of any guard
or safety devise. They are there for YOUR
PROTECTION!
4.
The operator must understand the safety rules
and operation of the machine and has read
the instruction manual BEFORE operating the
machine.
Summary of Contents for 500SNC
Page 1: ...Instruction Manual 500SNC Serial No 592 13178 to Band Sawing Machine ...
Page 6: ...2 MACHINE DIMENSIONS Continued TOP VIEW INCHES 03 MILLIMETERS 1 mm ...
Page 7: ...3 MACHINE DIMENSIONS Continued FRONT VIEW INCHES 03 MILLIMETERS 1 mm ...
Page 8: ...4 MACHINE FEATURES FRONT VIEW ...
Page 9: ...5 REAR VIEW MACHINE FEATURES Continued ...
Page 10: ...6 SIDE VIEW MACHINE FEATURES Continued ...