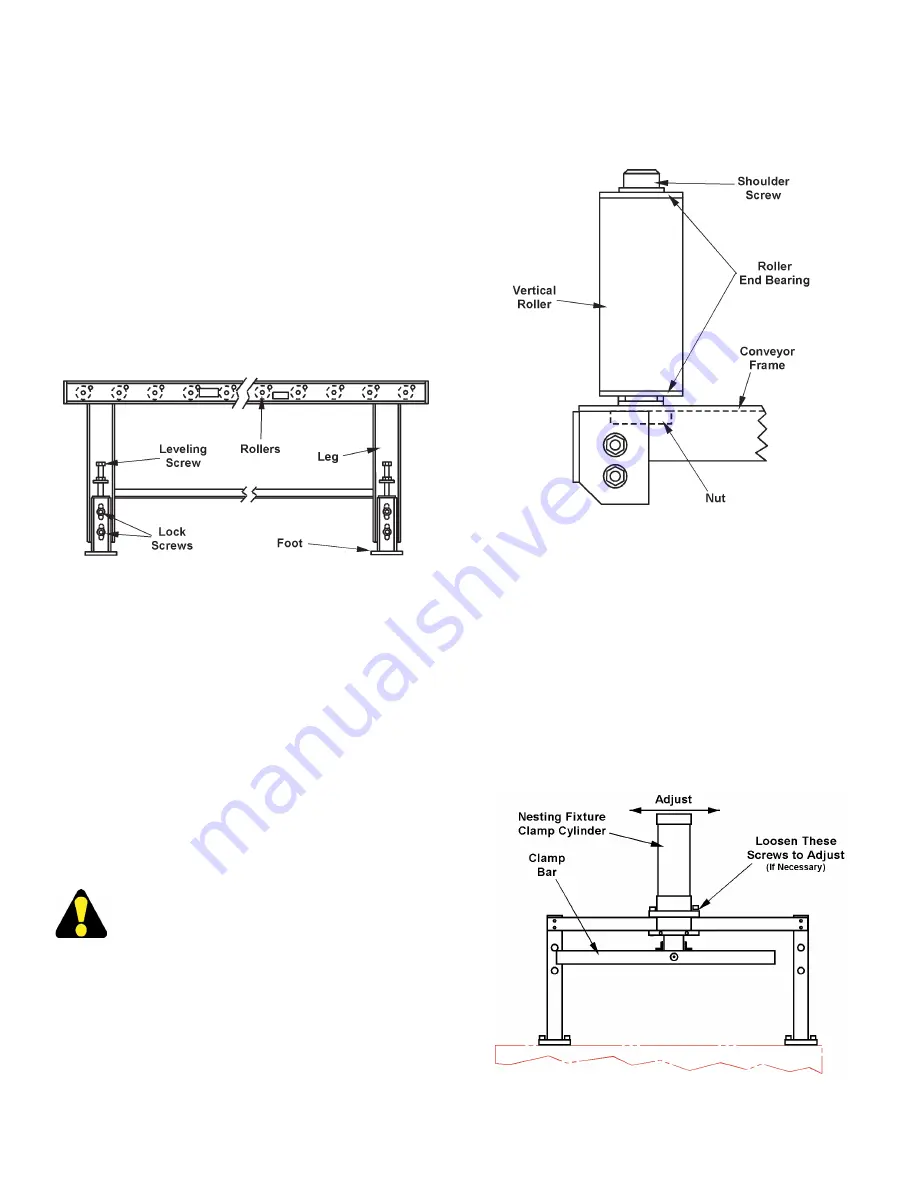
29
ACCESSORIES
ROLLER STOCK CONVEYORS
1.
Your machine may be equipped with one of the
following roller stock conveyors for moving long
stock into cutting position (or as an unloading add-
on). The following conveyors are available:
•
Stock conveyor five (5) feet (1525.0 mm) long by
18 inches (457.2 mm) wide rollers with a weight
capacity of 750 pounds (340.2 kg) per roller.
•
Stock conveyor ten (10) feet (3050.0 mm) long by
18 inches (457.2 mm) wide rollers with a weight
capacity of 750 pounds (340.2 kg) per roller.
Roller Stock Conveyor.
2.
To install a roller stock conveyor:
(a)
Position
the assembled conveyor(s) behind or in front of
the machine base; (b) Adjust the conveyor to the
machine with the leveling screws on the conveyor
legs. The top of the front conveyor roller should be
inline to 0.010-inch (0.25 mm) above the vise bed
wear plate.
3.
The remaining rollers must be parallel to, and in the
same plane with the vise beds to within 0.010-inch
(0.25 mm) per 24 inches (609.6 mm) of travel.
4.
Depress the roller shafts for ease of installation or
removal of rollers.
The conveyor DOES NOT attach to the machine
base. Anchor the conveyor to the floor after
all leveling and adjustments are made.
VERTICAL GUIDE ROLLERS (Conveyors)
1.
Vertical guide rollers are effectively used to help
maintain correct positioning of long stock on the
conveyor.
2.
These can be installed between the discharge tray
and conveyor or between conveyors (if more than
one is supplied).
Vertical Guide Roller.
NESTING FIXTURE
1.
This optional feature is designed for high-production,
multiple sawing of stacked bars, rounds and tubing.
Its jaws have the capacity to hold stock from 1.00
minimum to 19 inches (25.4 to 482.6 mm) wide, and
from 1.00 minimum to 14 inches (25.4 to 355.6 mm)
high.
2.
Vertical nesting clamp cylinders are mounted to
the machine’s roller bed rail and index vise. The
cylinders operate simultaneously with the regular
vise clamping cylinders.
Nesting Fixture Vise Adjustments.
Summary of Contents for 500SNC
Page 1: ...Instruction Manual 500SNC Serial No 592 13178 to Band Sawing Machine ...
Page 6: ...2 MACHINE DIMENSIONS Continued TOP VIEW INCHES 03 MILLIMETERS 1 mm ...
Page 7: ...3 MACHINE DIMENSIONS Continued FRONT VIEW INCHES 03 MILLIMETERS 1 mm ...
Page 8: ...4 MACHINE FEATURES FRONT VIEW ...
Page 9: ...5 REAR VIEW MACHINE FEATURES Continued ...
Page 10: ...6 SIDE VIEW MACHINE FEATURES Continued ...