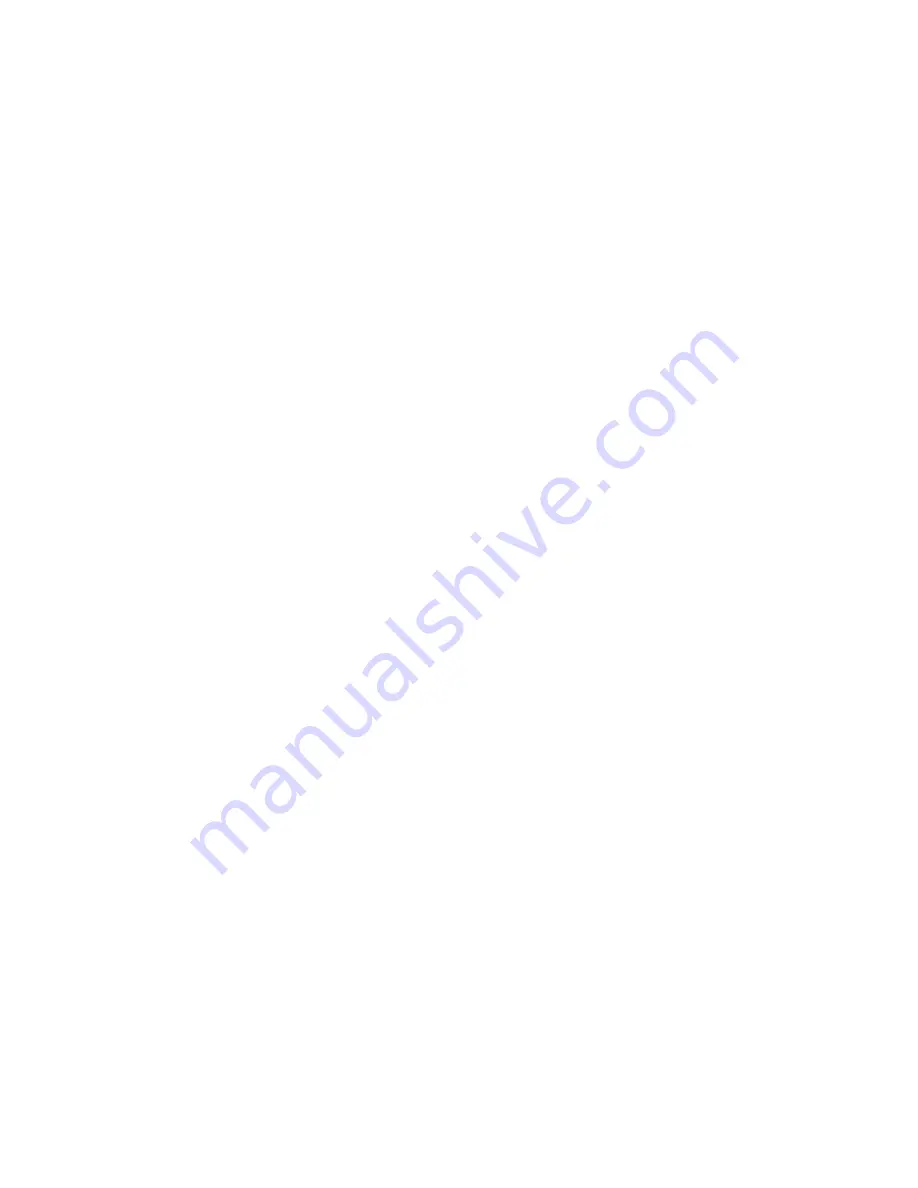
Copyright © 2022 Dive Gear Express
All Rights Reserved.
Revision 2 Published 09/23/2022
Revision Date
Changes
1 02/19/2021
Initial publication
1a 03/25/2022
Replaced photo for Fig. 28
2 09/23/2022
Minor technical edits for clarity; replaced Fig. 3, removed
Figs. 4 and 5 and renumbered subsequent Figs.; replaced
Figs. 24, 25, and 26
Summary of Contents for DGX Gears D6
Page 1: ...DGX Gears D6 Second Stage Service Manual...
Page 32: ......