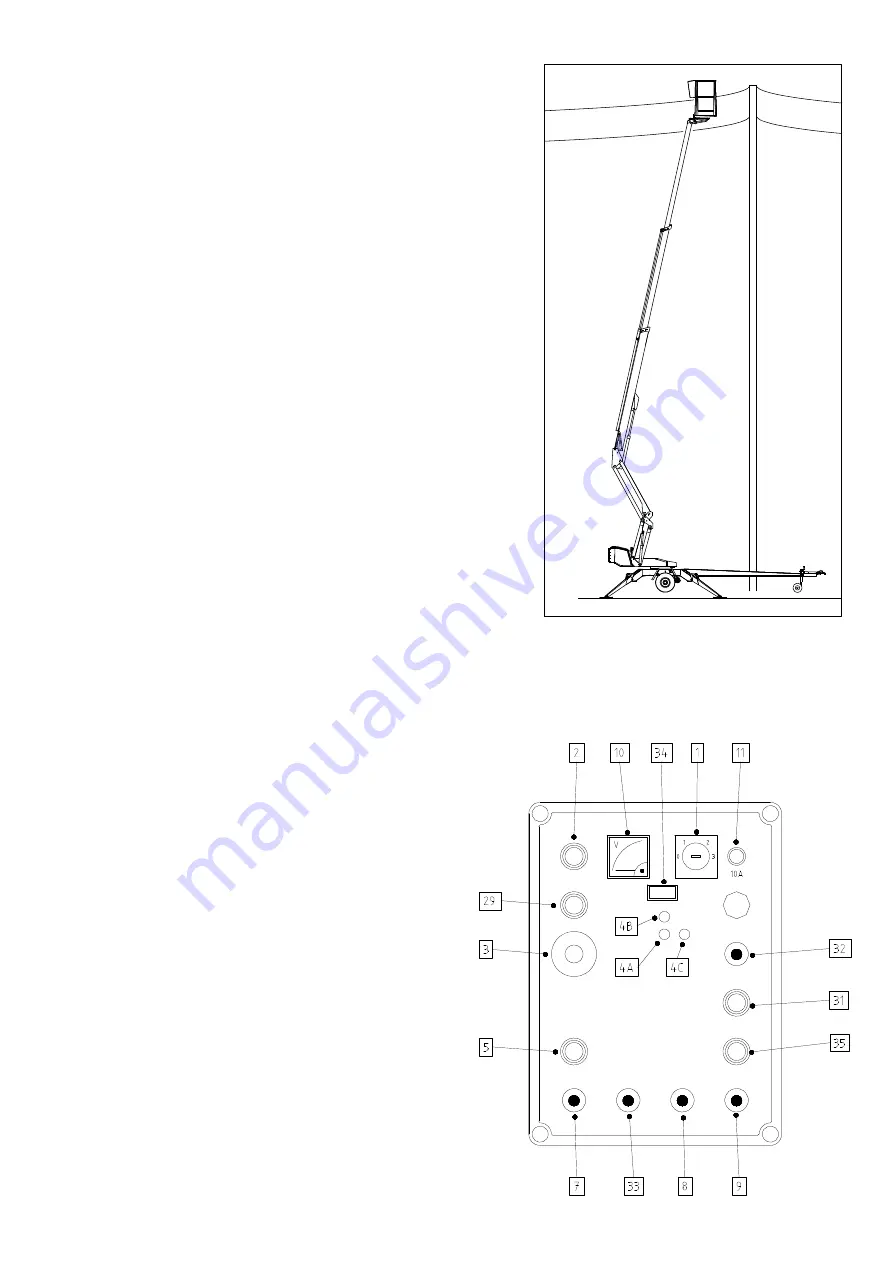
DINO 180XT
30
19. When moving the platform, remember the following
- special care should be taken in the vicinity of high voltage
cables
- do not exceed the max. allowed sideways load (400N)
(88 lbs)
- make sure that no part of the platform or the operator can
come into contact with open-wire cables
- objects may under no circumstances be thrown out of the
platform
- avoid damaging the unit
- when working do not take additional load onto the platform
- avoid damaging external objects or constructions
- do not overload the platform from working area
20. When the lift is left alone
- move the unit into a safe, steady position, preferably into transport position
- switch off the power unit
- prevent unauthorized use of the unit by locking the main operating panel cover
21. Adjusting the position of the work platform
The platform angle (horizontal) can be adjusted
from the lower control panel as follows:
- Put the operating switch (1) into position 1
- Push the platform operating switch (31) and
choose the direction with the operating lever (32)
Activate the controls simultaneously.
Use the platform positioning control when the
boom is horizontal.
No persons are allowed on the platform when
adjusting.
Use the positioning adjustment when the lift is
supported (outriggers lowered)
Summary of Contents for Dino 180XT
Page 2: ...DINO 180XT 2...
Page 3: ...DINO 180XT 3 OPERATION INSTRUCTIONS Valid from serial number 18154...
Page 6: ...DINO 180XT 6 REACH DIAGRAM m kg...
Page 8: ...DINO 180XT 8 REACH DIAGRAM ft lbs...
Page 14: ...DINO 180XT 14 LIMIT SWITCHES RK4 AND RK5 PRESSURE SPRING LINK LIFT CYLINDER...
Page 16: ...DINO 180XT 16...
Page 20: ...DINO 180XT 20 Notes...
Page 22: ...DINO 180XT 22...
Page 24: ...DINO 180XT 24...
Page 40: ...DINO 180XT 40 LUBRICATION PLAN...
Page 42: ...DINO 180XT 42 1...
Page 55: ...DINO 180XT 55...
Page 86: ...DINO 180XT 86 ELECTRIC SCHEMA 110 230VAC 18094...
Page 92: ...DINO 180XT 92 ELECTRIC SCHEMA 12VDC 230VAC DIESEL AGGREGATE 18154 18222 18226 18228 PRC 26A...
Page 94: ...DINO 180XT 94 Notes...
Page 95: ...DINO 180XT 95 ELECTRIC SCHEMA PETROL GASOLINE AGGREGATE 18069...
Page 96: ...DINO 180XT 96 ELECTRIC SCHEMA DIESEL AGGREGATE...
Page 97: ...DINO 180XT 97 ELECTRIC SCHEMA DIESEL AGGREGATE...
Page 99: ...DINO 180XT 99 HYDRAULIC SCHEME 230VAC 18001...
Page 101: ...DINO 180XT 101 HYDRAULIC SCHEME 110VAC 18001...
Page 102: ...DINO 180XT 102 Notes...