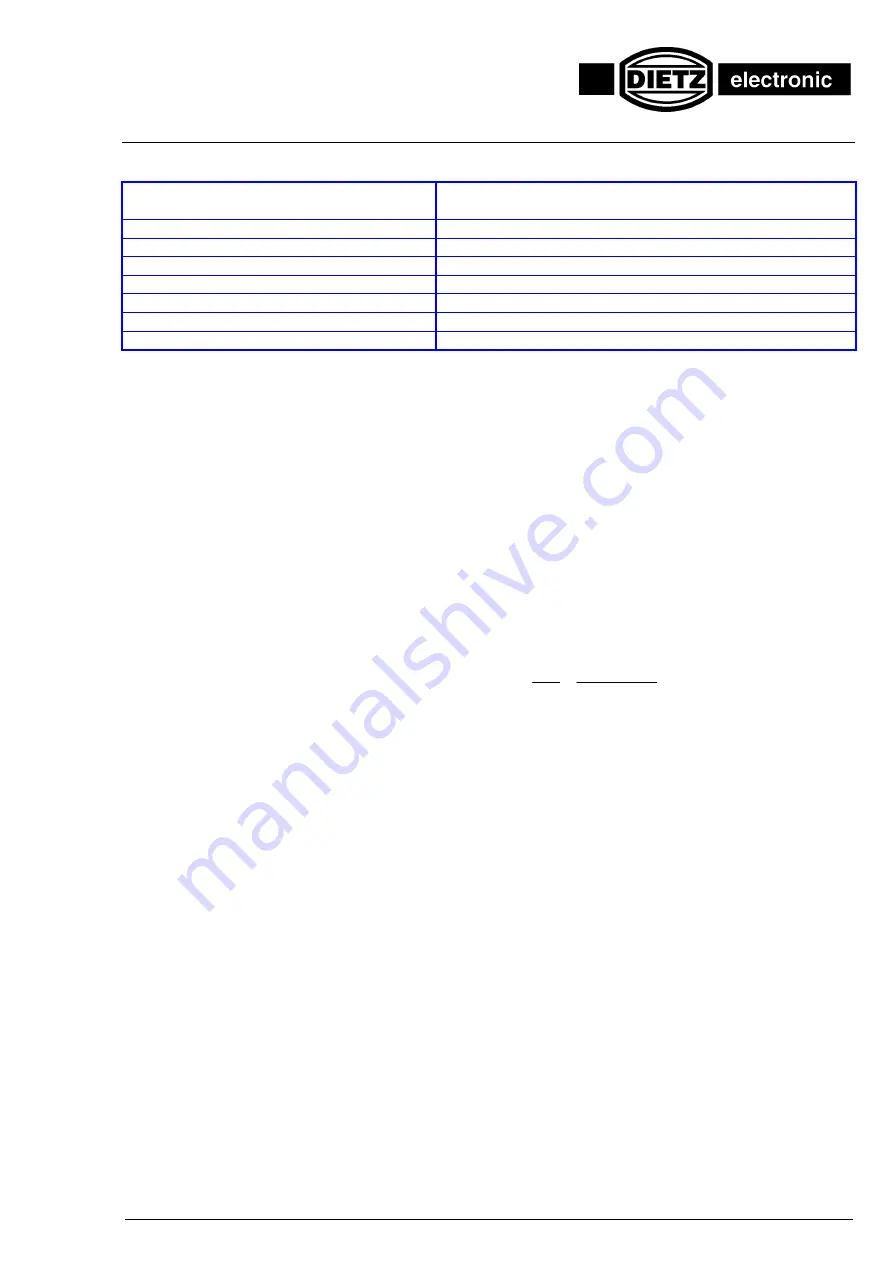
VECTORDRIVE DSV 5444
Top technology in drive electronics
07.07.04 10:12
Dietz-electronic
page 23 of 60
High-flexibility coupling between motor
and load
Rigid coupling between motor and load
F5 = F1 / 2 (speed for second root sector)
F5
≤
F1 (speed for second root sector)
Halve Y0
Y0 = F4 (run-up ramp)
Y1 = F4 + 16
Y1
≥
F4 + 16 (return ramp)
F4 = Y0 / 2
F4 = Y0 target ramp of position control)
F3 = 20 - 40
F3 = 50 - 80 (gain in position control)
F6
≤
4
×
i
F6 = 2
×
i (time constant of speed control in position control)
F7 = K
F7 = K (time constant of speed control in position control)
The drive must now be run with position control. If the setting is correct, the drive will run in the target position
without overshooting. If this does not occur, the target ramp (parameter F4) must be set at a flatter angle.
The setting for the control parameters F3, F6 and F7 given in the table is normally sufficient. If the required
control properties are not achieved, these parameters must be adapted to suit the installation. The perform-
ance of the position control loop is best assessed with the graphic actual value display (function key F9).
With synchronous operation, the values for the ramps (parameters F4, Y0 and Y1) are doubled on the fol-
lower drive.
The positioning speed ("G" command, parameters F11 and F27), reference travel speed (parameter F12)
and standardization factor for position control (parameter F21) and the zero position offset (parameters F8
and F26) must likewise be adapted to suit the purpose if necessary.
5.3 Standardization
Parameters F1, F2 and F5 are generally stated in revolutions per minute.
The speeds for the "O" and "G" commands and parameters F11, F12 and F27 can be standardized with pa-
rameters F10 and F22 to enable input in customer units. If data input in rpm is required, the parameters are
set according to the following formula (IZ_AKT = effective number of increments):
Effect on standardized speed (parameters F10 and F22):
F
F
IZ AKT
b c
22
10
4
=
×
×
_
b = Number of path units per motor revolution (standard value: b = 1)
c = Number of scans per time unit (standard value c = 75000).
For gearing ratio or expression in a customer unit (e.g. metres per second), the break must be multiplied by
the corresponding factors. For both parameters, two integer number values lower than 32767 must be found.
With standard settings (rotary position transducer with 1024 points, no gearing and IZ_AKT = 65536) and
expression of speed in rpm, the following values are obtained:
F22 = V_FKT = 6994
F10 = V_TEIL = 2001