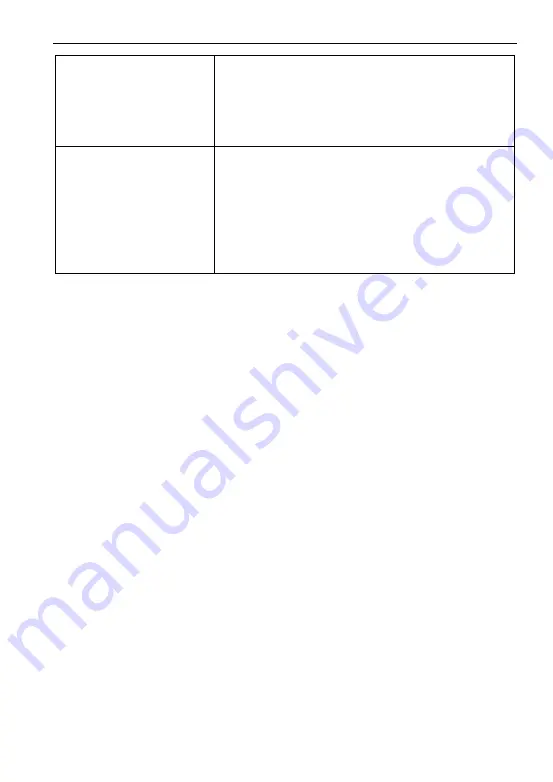
NO.7 Maintenance and Fault Information
81
Unfavorable
acceleration/deceleration of
motor
Improper setting of acceleration/deceleration time.
Too low current limit is set.
Overvoltage protection during deceleration.
Improper setting of carrier frequency, overloading or
oscillation.
Overhigh or overlow motor
speed
Improper selection of V/F characteristic.
Improper selection of reference for V/F characteristic and
resetting shall be performed.
Substandard or non-standard rated voltage of the motor.
Low voltage of power supply.
Wrong setting of frequency signal gain.
Wrong setting of output frequency.