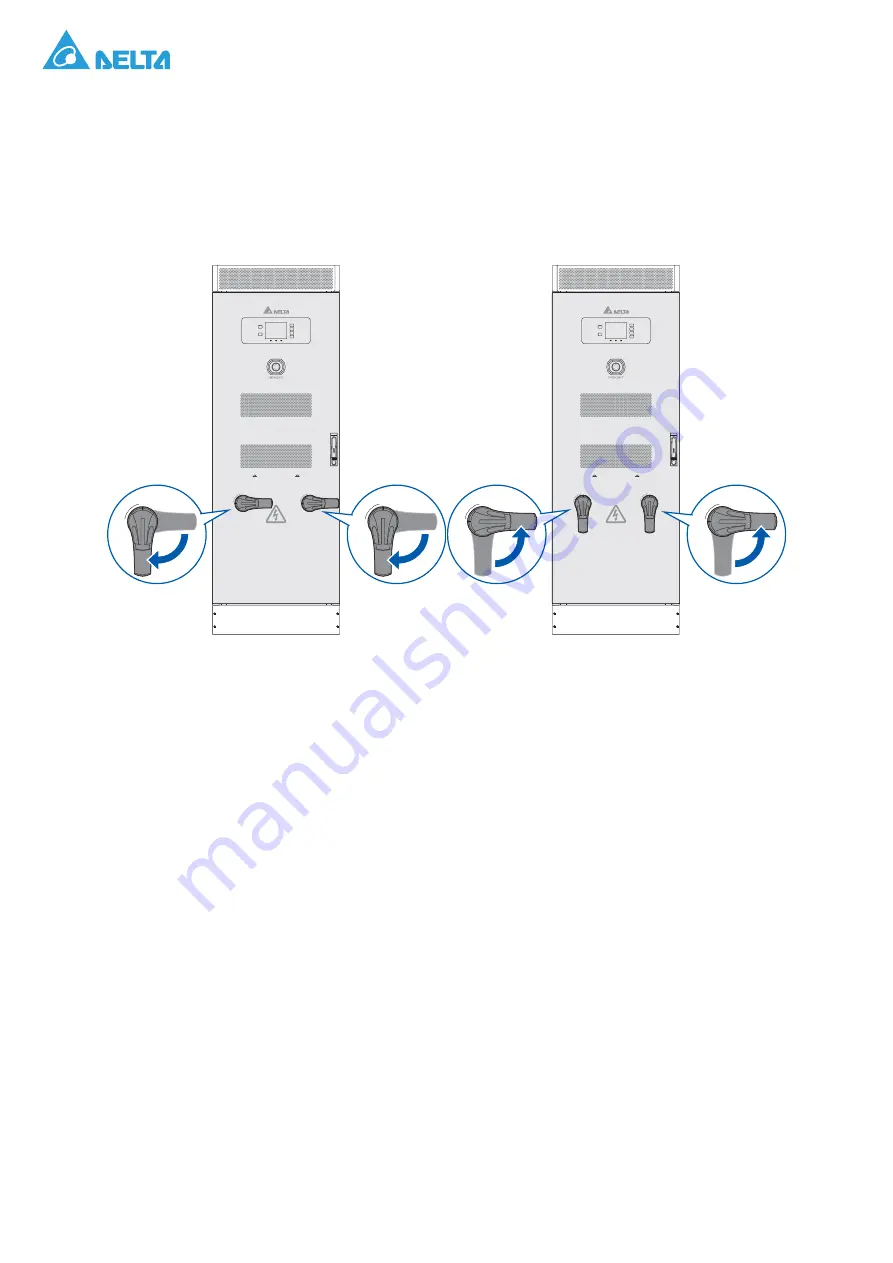
Wiring Instructions
Installation Manual
38
AC, DC Disconnect Position
The following figures show the status of AC and DC disconnects.
ON: Vertical, turn counterclockwise to horizontal position to OFF state.
OFF: Horizontal, turn clockwise to vertical position to ON state.
Figure 37.
PCS Front View with AC, DC Disconnects Status
ON
OFF
STANDBY
RUN
FAULT
ON
AC DISCONNECT
OFF
ON
DC DISCONNECT
OFF
ON
AC DISCONNECT
OFF
ON
DC DISCONNECT
OFF
ON
OFF
STANDBY
RUN
FAULT
ON
AC DISCONNECT
OFF
ON
DC DISCONNECT
OFF
ON
AC DISCONNECT
OFF
ON
DC DISCONNECT
OFF
Switch on for PCS
Switch off for PCS