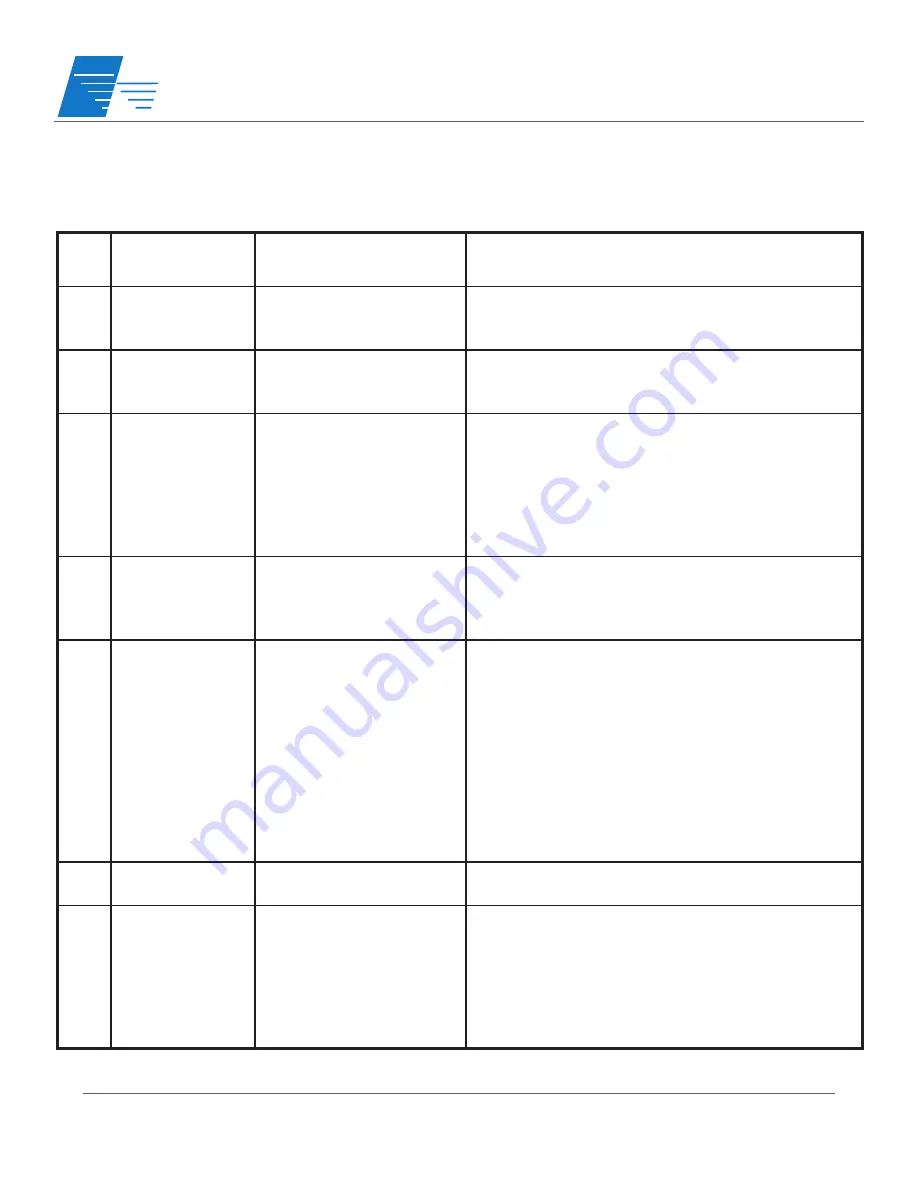
BECT832-SSO Screwdriver Controller
Operation Manual
DELTA REGIS
Tools Inc.
www.deltaregis.com
Page 14
During operation of the counting controller and screwdriver, the LED display may indicate an error code.
These codes indicate a fault that was encountered during the operation of the tool/controller.
Code Indicates
Error Description
Possible Cause / Solution
E3
Low Voltage
Protection
Screwdriver has stopped
because the operating
voltage is too low.
- tool supply voltage has dropped below acceptable
levels due to excessive current draw or malfunction.
If problem persists, send in for evaluation.
E4
High Temperature
Protection
Screwdriver has stopped
because the operating
temperature is too high.
- excessive duty cycle; allow tool/controller to cool
down and re-test at lower duty cycle
- internal issue; send for evaluation/service
E5
Stall Protection
Screwdriver has stopped
because the motor stalled
abnormally.
- prevailing torque (eg. soft joint, thread cutting)
is causing the tool’s motor to slow down and stall
before reaching final torque; evaluate suitability of
tool for the application
- internal damage to gearing, clutch, or lack of
lubrication is affecting motor’s ability to complete the
rundown; inspect gearing and clutch
E7
FWD/REV Switch
Error
Controller detected a
change in the position of
the FWD/REV switch while
the tool was running.
- FWD/REV Button was moved by the operator
during rundown
- switch PCB improperly positioned in tool housing
or magnetic switching element has failed
E8
Brake Error
Controller detected an
abnormal brake (clutch)
signal before the tool was
started.
- clutch is stuck at the top of the clutch ramp,
possibly caused by operator releasing trigger too
early in anticipation of shut-off. Turn off power to the
driver, put a 1/4” hex key in the output shaft and turn
the output shaft to reset the clutch - you will here
a click when it resets. Ensure that operators are
instructed to hold the trigger until the tool clicks over
the clutch and shuts off.
- internal push rod mechanism for clutch shut-
off is sticking or of incorrect length. Send tool for
evaluation/service.
E9
Flash Memory
Error
The internal flash memory
has failed.
- reset the controller to see if the error clears; if error
persists, send in for evaluation and service.
PC
Power Change
An error or change in the
tool supply voltage has
been detected.
- Hi/Lo speed switch position was changed with the
key lock turned ON. Lock must be off to change
speed setting.
- voltage setting incorrect for screwdriver being
used. (eg. 40V setting selected for a 32V driver)
- very soft joint causing power drop during rundown
- faulty tool cable/connection; test with a new cable.