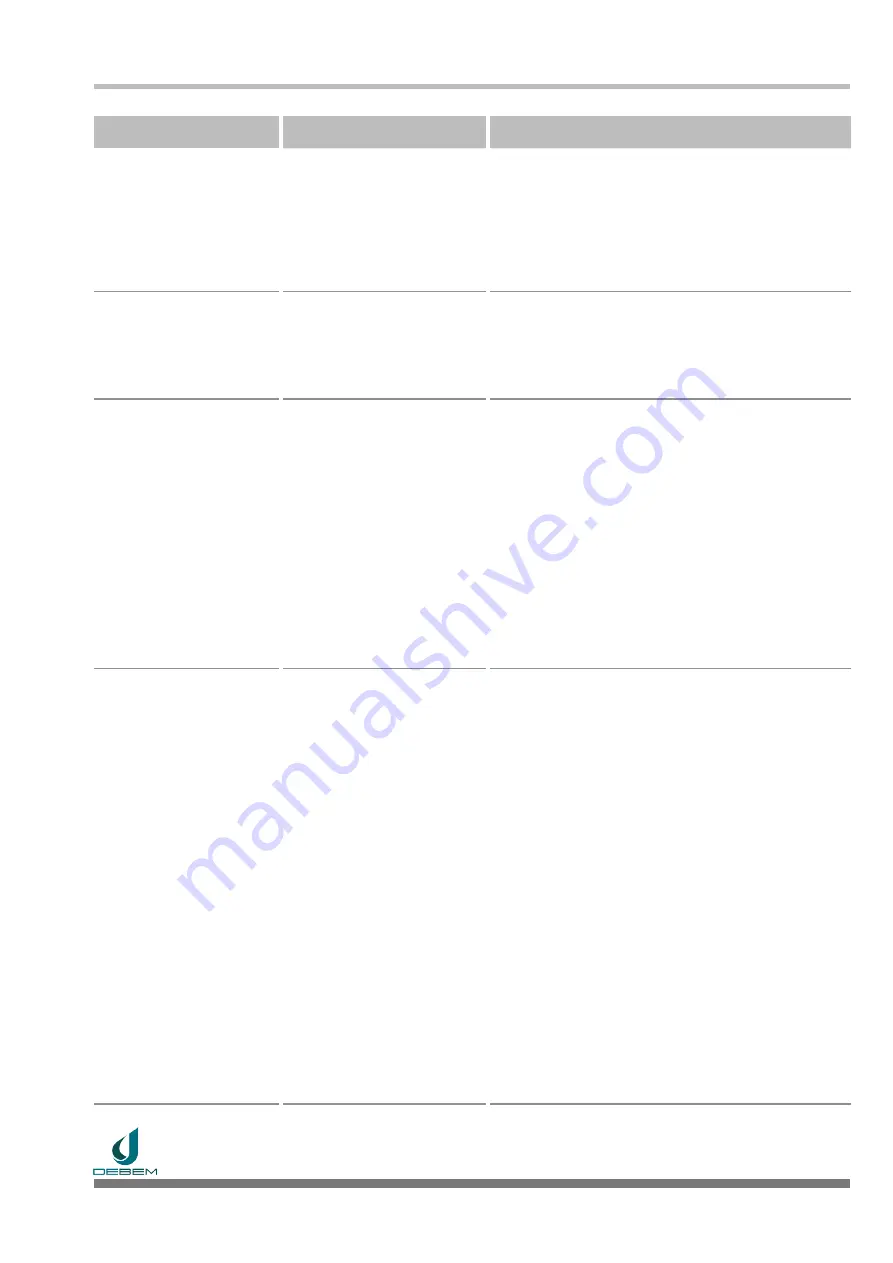
Page 59
of
68
INDUSTRIAL PUMPS
www
.debem.com
Chapter 7 - problems and solutions
Translation of original instructions - S
CUBIC -
S
BOXER
rev
. 2021
Continued from the previous page
ANOMALY
POSSIBLE SOURCE
ADVICE
2. The pump exchanges
but does not move the
fluid.
2.5
Internal pneumatic insert
worn or defective.
2.6
Worn shaft.
2.7
Ice on the drain.
2.8
Lack of air volume.
2.9
Dirty pneumatic insert.
2.5a
Replace the pneumatic insert.
2.6a
Replace the shaft.
2.7a
Dehumidify and filter the air.
2.8a
Check all air control accessories, especially the
quick-release couplings.
2.9a
Clean or replace the pneumatic insert
.
3. The pump works with
slow cycles.
3.1
Fluid too viscous.
3.2
Supply pipe clogged.
3.3
Suction clogged.
3.4
Needle valves are too
closed.
3.1a
No remedy.
3.2a
Check and clean.
3.3a
Check and clean.
3.4a
Check the setting of the needle valves of thepneu-
matic oscillator for speed regulation
.
4. The pump does not
exchange.
4.1
Intake obstructs during
operation.
4.2
Dirty air, full of condensate
or oil.
4.3
Insufficient air flow or
pressure
4.4
Shutdown procedure not
complied with.
4.1a
Replace the suction hose.
4.2a
Check the air line.
4.3a
Check the pressure with a pressure gauge installed on the
pump and when the pump is running
see fig. 4.4.3 page 35
.
If the pressure at that point is too low in relation to the
at mains pressure, check all connections air, especial-
ly those with quick-release couplings.
Check that all air control devices have sufficient
capacity.
ATTENTION: 90% of cases depends on
quick couplings.
4.4a
Comply with the shutdown procedure see
Section 5.2
page 41
.
5. The pump does not de-
liver the table scope.
5.1
Product intake hose is badly
connected.
5.2
Clogged pipes.
5.3
Fluid too viscous.
5.4
The balls do not close.
5.5
Insufficient air volume.
5.6
Possible pressure losses
on the supply line air to the
pump.
5.7
Probable back pressure
or head higher than those
allowed by the model of the
pump used, in relation to
the flow rate delivered.
5.1a
Check and reconnect.
5.2a
Check and clean.
5.3a
Install oversized pipes, especially in the suction and
decrease pump cycles.
5.4a
Dismantle the manifolds and clean the seats or
replace the balls and seats.
5.5a
Check the pressure with a pressure gauge installed on
and with the pump running:
see fig. 4.4.3 page 35
.
If the pressure at that point is too low in relation to
the at mains pressure, check all connections air,
especially those with quick-release couplings.
Check that all air control devices have sufficient
capacity.
CAUTION: in 90% of cases, stall occur
-
rences are caused by snap-on fittings.
5.6a Check the pressure at the entry point of the
pump.
Eliminate pressure losses on the line supply-
ing compressed air to the pump.
5.7a Check the actual pressure of the product deliv-
ered by the pump at the outlet of the delivery
manifold.
Eliminate backpressures on the product
delivery line or use the pump model suitable for the
desired flow rate.