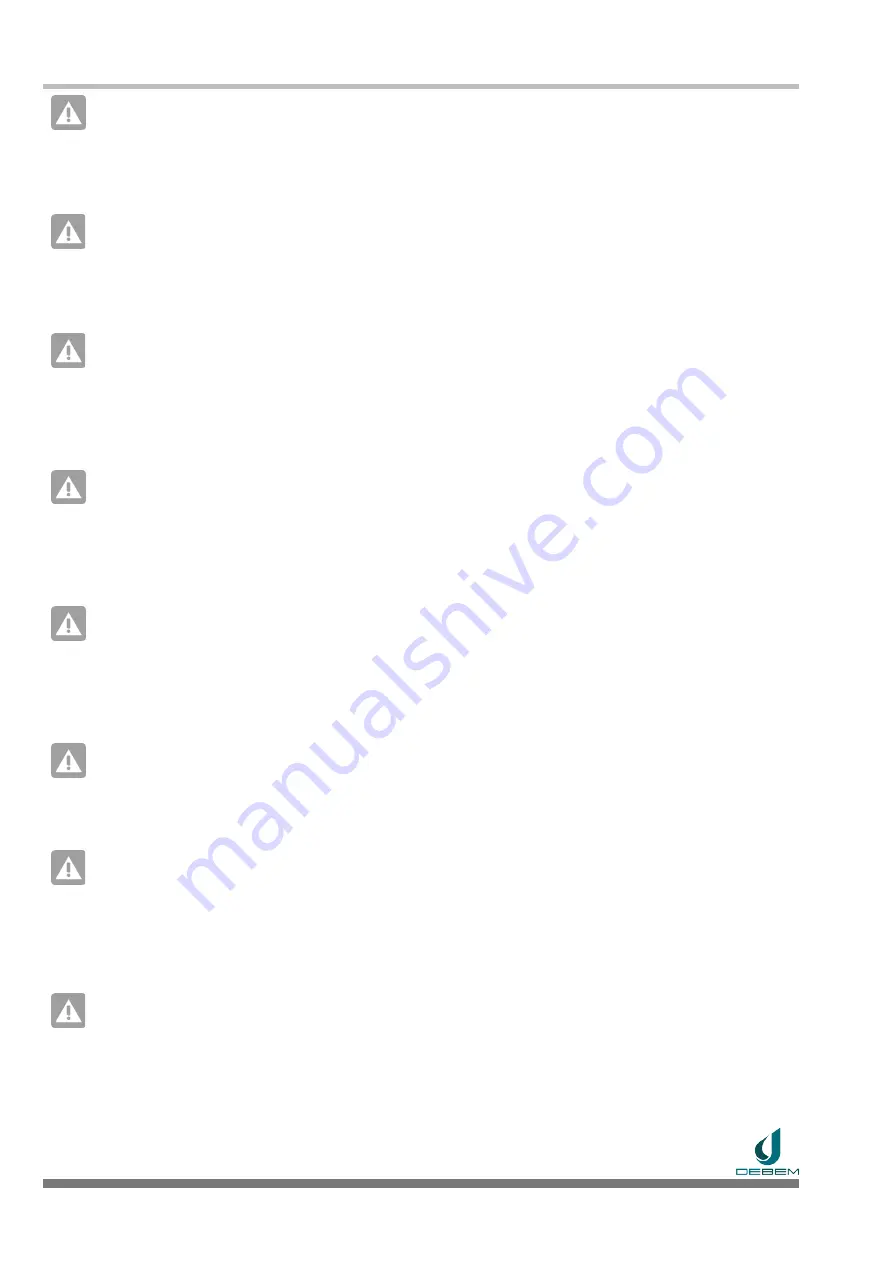
Page 26
of
68
INDUSTRIAL PUMPS
www
.debem.com
Chapter 3 - Warnings and Requirements
Translation of original instructions -
S
CUBIC-
S
BOXER
rev.
2021
CAUTION:
danger of uncontrolled product leakage.
Installations with high delivery head and/or with fluid of a high specific weight, can generate strong
back-pressures that prematurely wear the diaphragms and/or cause a possible breakage.
3.1.16
In installations where the presence of solid particulate suspended in the product is foreseen, install a
suitable strainer on the suction inlet, with a surface area of 2.5 or 3 times the area of the suction pipe and
passages smaller than the size of the particulate allowed by the pump.
CAUTION
: risk of damaging the pump
Installing the pump without a suitable strainer or with an insufficient and undersigned fluid flow rate and/
or passage larger than the particulate allowed by the pump model is forbidden.
3.1.17
In general, all fittings, ducts and valves and/or filters installed along the entire air circuit and product cir
-
cuit, upstream and downstream of the pump, must never have a flow rate lower than the nominal values
of the pump.
WARNING:
danger of rupture of membranes and product leakage
.
The presence of points of flow below the pump's nominal values along the air and product circuit lines
upstream and downstream of the pump, in addition to causing poor efficiency and performance, can
lead to premature diaphragm wear and/or possible rupture.
3.1.18
To install the pump, use fittings with cylindrical gas threads, made of the same construction material
as the pump. In general, all pump threads for connecting the fluid suction and discharge lines are not
intended to ensure hydraulic tightness; use suitable seals to ensure hydraulic tightness.
CAUTION:
risk of thread breakage and product leakage.
The use of fittings with conical threads or made of a different material than the pump is prohibited
.
The tightening of the suction and delivery fittings must ensure the mechanical seal of the ducts while to
ensure the hydraulic seal, use suitable seals.
3.1.19
Using the pump in a potentially explosive environment must always provide for an efficient earthing of the
same, regardless of any organ connected to it. When pumping
flammable liquids (allowed by the marking),
it is essential touse suitable "CONDUCT " pumps with the ATEX marking, with appropriate earthing.
CAUTION:
risk of explosions due to electrostatic charges.
Lack of earthing or incorrect earthing of the pump, will cancel the requirements for safety and protection
against the risk of explosion provided for by the affixed ATEX marking.
It is forbidden to use pumps made
of non-conductive material (which is electrostatically charged) for flammable liquids, and/or without ade
-
quate earthing.
3.1.20
The presence of vortices at the suction point creates cavitation and malfunctions. During operation, check
for any abnormal noise and that the outlet fluid does not contain “gas”.
CAUTION:
in the event of abnormal noise, stop the pump immediately.
Abnormal noise or the presence of "gas" in the fluid leaving the pump indicates an abnormal condition
for which the cause must always be determined before continuing use.
3.1.21
Depending on the configuration, place of installation of the pump and duration of exposure
near it, it is
necessary to detect the emitted noise.
CAUTION
: risk of exposure to noise.
If necessary, use suitable sound-absorbing barriers and/or Personal Protective Equipment (such as
sound-absorbing caps or headphones).
3.1.22
The diaphragms, (internal and in contact with the product) are components subject to wear. Their duration
is strongly affected by the conditions of use and by the chemical and physical stresses to which they are
subjected. Tests carried out on thousands of installed pumps (with a head of 0.5 m at 20°C) have shown
that they last more than 100,000,000 (one hundred million) cycles.
CAUTION
: risk of diaphragms breaking.
For safety reasons, the pump diaphragms must be dismantled and checked
every 10,000,000 (ten
million) cycles and replaced every 20,000,000 (twenty million) cycles
.
3.1.23
Pump operation can only be adjusted by shuttering the compressed air supply, by adjusting the network
pressure, or according to the piloting system installed (by shuttering the oscillator’s flow regulators or,
with a remote 2/3-way valve, by adjusting the speed from the PLC).