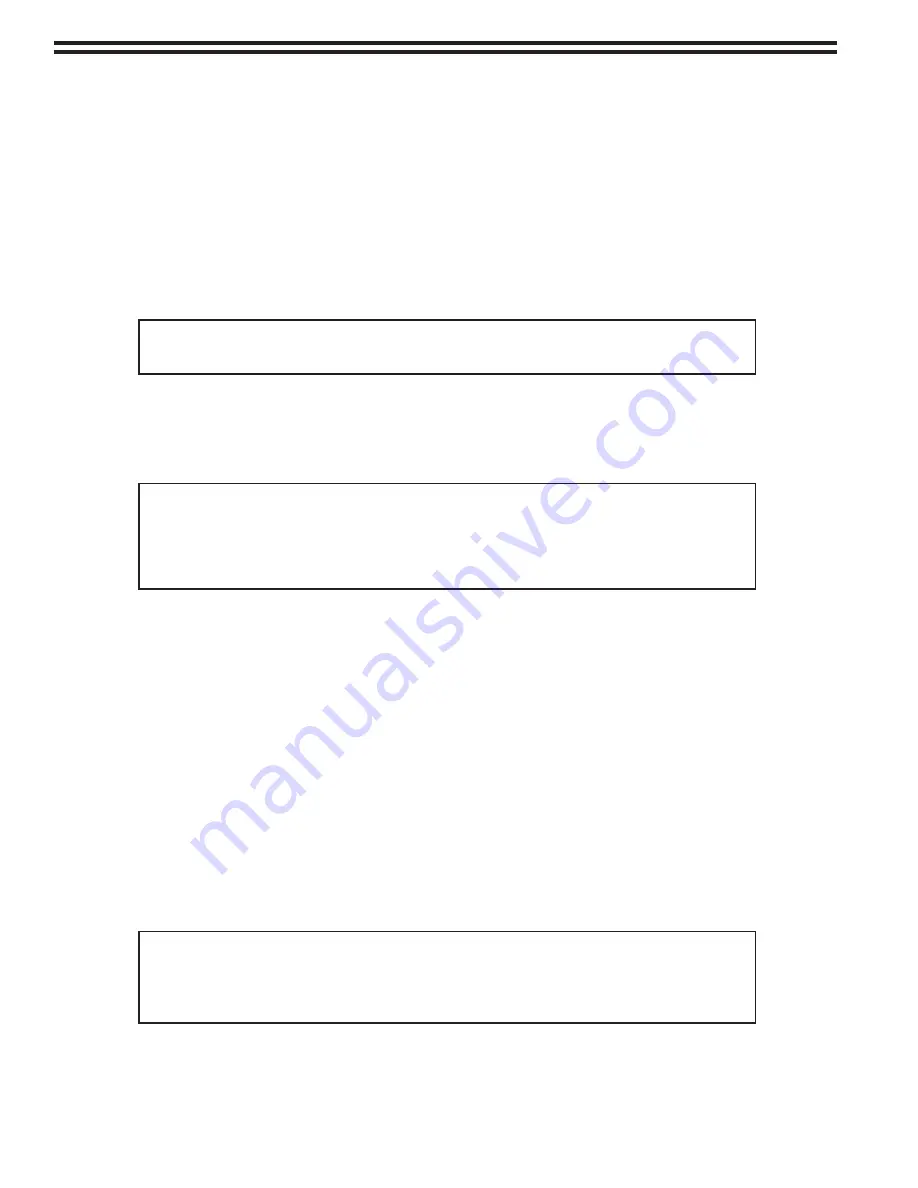
115.6031.0
- 34 -
8) Disconnect and remove all sensor extensions from the vaporizing chamber cover and support flanges. Then
remove the mounting bolts from the support flange (i.e., the bolts which extend through the lip of the water
chamber); and lift the vaporizing chamber from the water chamber using the lifting eyes (provided in the
support flange for this purpose) and a one ton capacity overhead chain hoist.
NOTE:
A clean vaporizing chamber weighs approximately 340 lbs.
9) Swing the vaporizing chamber free of the water chamber and lower it to the floor, tipping it and placing it on its
side for subsequent cleaning and inspection. Then clean and flush the water chamber free of all accumulated
deposits and inspect the surfaces of the heating elements of the electric immersion heater; removing the heater,
if necessary to clean the elements.
10) Clean and flush the outer surface of the vaporizing chamber free of all accumulated deposits.
WARNING
Steps 11, 12 and 13 below must be performed outdoors or in a well ventilated area.
11) Remove the mounting bolts from the vaporizing chamber cover flange and separate the flange from the
chamber, complete with inlet tube and superheat baffle.
12) Using steam, clean all surfaces of the inlet tube and superheat baffle and the internal surface of the vaporizing
chamber free of all accumulated deposits of non-volatile residue.
NOTE
Inspection of the inlet tube (refer to Figure 1), attached to the cover flange,
provides a quick visual means of estimating the degree or severity of corrosion.
If the corrosion is completely through the inlet tube, the gas chamber should be
thoroughly inspected internally for corrosion and replaced if necessary.
To facilitate the cleaning of the vaporizing chamber, place the chamber in a partially inverted position (bottom
end up) so that the hot condensate can serve as the carrying agent to remove the entrained oily deposits from
the chamber.
If a source of steam (hot water is not an effective cleaning agent) is not available on site, these components will
have to be sent to an outside facility which provides this service.
13) After cleaning, inspect both the inner and outer surfaces of the vaporizing chamber for corrosion. It is expected
that the most severe corrosion will appear in the area corresponding to the normal water level on the outside
and the normal liquid gas level on the inside. Measure the depth of any pits by placing a straight-edge length
wise on the chamber to act as a reference. The Vaporizer chamber pressure rating allows for up to 1/8 inch of lost
metal due to corrosion of the chamber wall. Any pitting found must not exceed a total of 1/8 inch or have a
chamber wall thickness less than 0.300 inches. If pitting is found in excess of these amounts, the chamber must
be removed from service and replaced.
Spent liquid indicates contamination. Another industry practice is to shine a black light at the cleaned surface.
Most oils and grease will fluoresce under this examination. Any fluorescence should be taken to indicate
contamination.
NOTE
The practice of weighing the chamber to determine the amount of material lost
due to corrosion is not recommended since this method may not reveal any
structural defects or pin holes.
14) Upon reassembly, install a new gasket in the flanged connection between the top of the vaporizing chamber
and the cover flange. The ultimate torque specification is 200 ft. lbs. The procedure is to tighten the bolts snugly by
hand and then to tighten the bolts sequentially in diametrically opposite fashion to 50, 100, 150 and finally 200 ft. lbs.
In this manner the gasket is not distorted as the torque is gradually increased to its ultimate value.
Summary of Contents for Capital Controls 71V3B Series
Page 1: ... 1 115 6031 0 Instruction Manual Series 71V3B Electrically Heated Vaporizer CAPITAL CONTROLS ...
Page 9: ... 9 115 6031 0 Figure 1 Sectional Diagram ...
Page 17: ... 17 115 6031 0 Figure 4 Outline Mounting Dimensions 12 kW 15 kW Heaters ...
Page 18: ...115 6031 0 18 Figure 5 Outline Mounting Dimensions 18 kW Heater ...